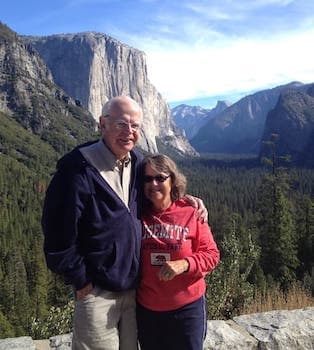
Curated with aloha by
Ted Mooney, P.E. RET
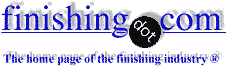
The authoritative public forum
for Metal Finishing 1989-2025
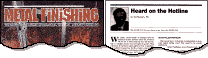
-----
Is Passivation or Black Oxide Finish better for Stainless Steel?
Q. Can some tell me where I can get information about black oxide/passivation process. I mean website. I design opto-mechanical components for Nortel Networks. The material of the components are either steel or stainless steel. These components need to be coated black. At this point, I have very little knowledge of the process. I want to know the basic fundamental of this process so I can talk to the vendors.
Thanks,
Lee A.Nortel Networks - Billerica, Massachusetts
2001
A. Lee -
Black oxide is a common choice for optical components because it doesn't change any part dimensions and will stay black even in some pretty extreme conditions.
Dan Brewerchemical process supplier - Gurnee, Illinois
Q. I am trying to evaluate two supplied metal threaded studs. Both are manufactured using 'CRES' (Corrosion Resistant Steel?). The stated finish on one is 'passivated' the other is 'black oxide'
My questions are:
What are relative advantages or disadvantages of using one finish over the other?
Is there a non-destructive test to confirm passivation has been performed? (Is visual sufficient?)
Consumer - Knoxville, Tennessee
2007
![]() |
A. The passivated one will be more corrosion resistant, unless the black oxide is oiled or waxed. - Navarre, Florida A. No definite answer. Depends upon the particular CRES alloy, supplemental treatment given the black oxide, usage and corrosive environment. - Goleta, California ![]() Rest in peace, Ken. Thank you for your hard work which the finishing world, and we at finishing.com, continue to benefit from. |
Q. If one of these two processes were to be used in an interior of a vehicle on a very small piece of SS (430L or 434L) what would the best process be? This small piece is made to blend with other black items in the interior of a vehicle.
Thank you
- Janesville, Wisconsin USA
October 24, 2016
A. The main thing I try to point out in these situations is, if you want a coating anyway (black oxide, paint, powder coat, etc.), why use stainless steel in the first place? You may as well save on material costs and use mild steel.
The main point of stainless steel is the surface is more corrosion resistant as the bare metal (usually with passivation, of course).
If you must, then stainless can be painted or powder coated without too much trouble, but processes like black oxide and electroplating typically require stainless to be activated using a very harsh acid mix.
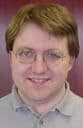
Ray Kremer
Stellar Solutions, Inc.

McHenry, Illinois
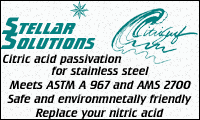

this text gets replaced with bannerText
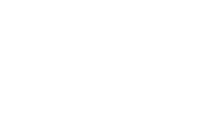
Q, A, or Comment on THIS thread -or- Start a NEW Thread