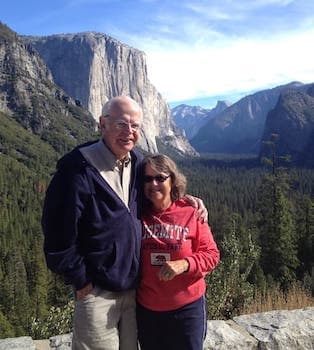
Curated with aloha by
Ted Mooney, P.E. RET
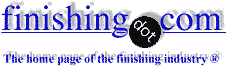
The authoritative public forum
for Metal Finishing 1989-2025
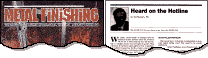
-----
Shot blasting vs. 7-Tank phosphating process
< Prev. page (You're on the last page of the thread)
Q. We are making 5 & 6.5 Gallon fuel tanks using 3 mm HR sheets. Before welding the panels are degreased and post welding the fuel tanks are shot blasted.
Post shot blasting tanks are cleaned by air pressure and then powder coated.
We are facing problem of painting peel off on the larger surfaces of tanks after 30-45 days and find the surface below the coating rusty.
Need help in assessing the possible cause of rusting & coating peel off.
Thanks,
- Delhi, India
October 21, 2016
A. Hi Bharat. In my opinion, and that of some other people on this thread, your process consisting of shot blasting followed by powder coating is no good. As a minimum, the tanks should be phosphatized before powder coating. Good luck.
Regards,
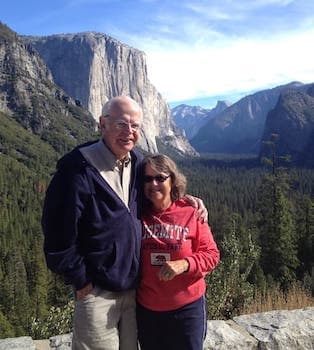
Ted Mooney, P.E. RET
Striving to live Aloha
finishing.com - Pine Beach, New Jersey
Can we skip cleaning and de-rusting before phosphatizing if the parts are blasted?
Q. Dear sir,
We are doing 9-tank phosphate process using annealing over components after shot blast; no oil/rust, is it necessary to do degreaser & de-ruster & activator before phosphating?
- India, Karnataka,Bangalore
January 8, 2017
A. Hi Prahalada. If I am understanding correctly you would need to do the activator because this is also a grain refiner pretreatment.
Whether you need to degrease and de-rust will probably have to be determined empirically rather than from first principles. But actually, you'll consume very little cleaning chemicals if the parts are already clean, and you'll consume very little de-ruster if the parts are free of rust and the de-ruster is inhibited, so there may actually be little value in experimenting to see whether those steps can be safely skipped anyway.
Regards,
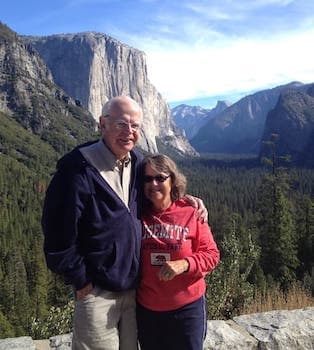
Ted Mooney, P.E. RET
Striving to live Aloha
finishing.com - Pine Beach, New Jersey
January 2017
Q. Hello,
I'm a manufacturer of hospital furniture in India. I use Cold Rolled Mild Steel material for hospital beds and other furniture. My question is, Is it advisable to sand blast the material before undergoing the 7-tank pre-treatment process (for better finish) which is then followed by powder-coating of the CR MS material?
- Gujarat, India
August 1, 2017
August 2017
A. Hi Panchal. Phosphatization of cold rolled steel without sandblasting is probably adequate, but it is easy to picture, for example, welding slag not being thoroughly removed and then breaking off after phosphatization and powder coating, or one fabricated bed being set aside for a few weeks and becoming too rusted to handle without blasting. Although metal finishing is a science, some aspects must still be resolved empirically rather than from first principles :-(
Regards,
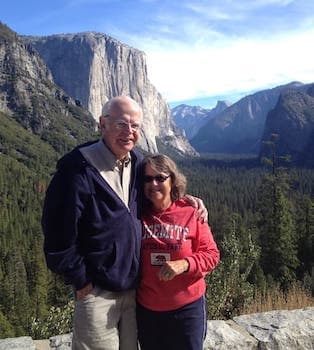
Ted Mooney, P.E. RET
Striving to live Aloha
finishing.com - Pine Beach, New Jersey
Q. Hello Ted,
Your response is highly appreciated.
So let me get this straight ... if I am fabricating the bed and keeping it aside for a couple of weeks, then it is advisable to first sandblast the fabricated bed (since it will probably be too rusted), then undergo the 7-tank pre-treatment process which is then followed by a powder coating process.
Am I getting this correct?
- Gujarat, India
August 12, 2017
August 2017
A. Hi again Panchal. Yes, that is what I am suggesting, i.e., that your phosphatization process might not be capable of removing heavy rust. It's obviously hard to say from half a world away exactly how much rust your phosphatization system can reliably handle.
Regards,
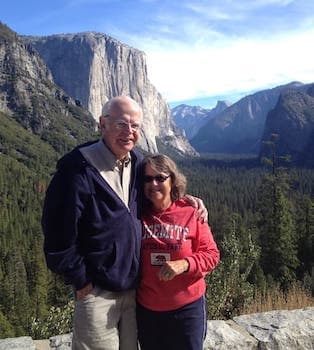
Ted Mooney, P.E. RET
Striving to live Aloha
finishing.com - Pine Beach, New Jersey
October 23, 2017
Q. We are receiving some pipe jobs (fuel pipes) only for Pickling. they don't need Galvanizing. However the problem is we need to provide the pickled pipes to customer without rust inside. The outside of the pipes are shot blast and painted. What are the acceptable methods to prevent rust inside pipes until they are put into service?
Prabath GunasekaraQuality Assurance Manager - Colombo, Sri Lanka
October 2017
Hi Prabeth. I think a better answer might be to phosphatize the pipes, in and out, and then paint the outsides. Iron phosphatizing may be good enough; zinc phosphatizing would be better.
Regards,
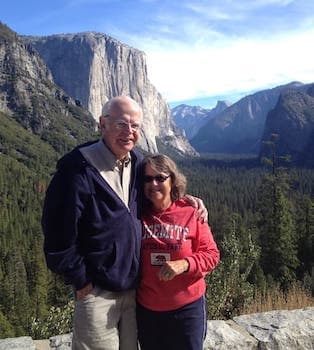
Ted Mooney, P.E. RET
Striving to live Aloha
finishing.com - Pine Beach, New Jersey
Pretreatment for CRCA/HRCA welded components
Q. Dear Sir/Madam,
Currently we are doing 7 tank pre treatment process for CRCA/HRCA component assemblies before powder coating and painting.
As the pollution level in 7-tank pre treatment process is very high, is it possible to use 3-in-1 solution cleaning for the component assemblies instead of 7-tank pre treatment?
Kindly confirm whether the adhesion of primer or powder in CRCA/HRCA after cleaning in 3 in 1 solution will pass the salt spray test and peel off test.
Regards,
- Bangalore, Karnataka, India
May 6, 2018
A. Hi Anil. Iron phosphating (3-step process) should suffice for components used indoors and protected from the weather. But the 7-step process is better for moderate to severe exposure for the same reason that a 7-course dinner is better than trying to make it into a 3-course dinner by putting the customer's salad into their soup and their apple pie into their coffee. When you are able to keep separate and thereby optimize the cleaning, derusting, grain refinement activation, phosphatization, and passivation steps, I think everyone would agree that it is always going to be a significantly better process.
opinion! If people worry about the environmental consequences of each ounce of phosphate while ignoring the consequences of re-mining, re-smelting, re-fabricating, re-painting, re-packaging, and re-landfilling each ton of steel every 3-4 years instead of it lasting 20 years, I think they are misunderstanding pollution & sustainability issues. It's not a matter of passing a salt spray and adhesion test, but of optimally finishing components based on decades of real-life experience which recognizes the many different types and causes of corrosion. In my own limited experience, if no galvanizing or electrocoat priming will be applied, iron phosphatizing plus powder coating will often not comprise a robust anti-corrosion sequence for outdoor exposure.
Regards,
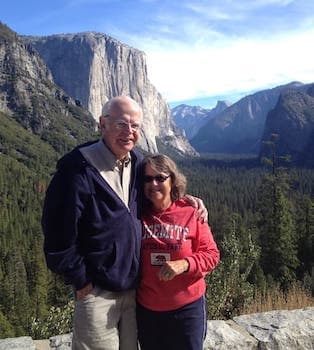
Ted Mooney, P.E. RET
Striving to live Aloha
finishing.com - Pine Beach, New Jersey
May 2018
Q. Hi, please let me know what are the pro and cons of the shot blasting and chemical pretreatment. Which one is the best? I have 7 tank treatment process which is not in running condition last 2 years and I have restored some of the things to run the this system. But cost is the main factor for me. I have two options, either 7 tank process or shot blasting, but for shot blast I have to go for out source to do shot blast and primer -- do not know which process will be best and easy to use in terms of easy, Cost and Quality.
Please help me out.
Devendra
- Chennai,up, India
June 16, 2018
June 2018
A. Hi Devendra. The pros & cons of shot blasting vs. chemical pretreatment is mostly what the previous 33 entries on this thread have been about :-)
Please ask for clarification about anything which you did not understand or which appeared ambiguous rather than simply starting the thread over again -- because it exasperates the responders and is therefore usually the kiss of death to a thread.
- What are your parts, are they welded, what are their sizes, how heavy is the rust, hot rolled or cold finished?
- What environment will the parts see: controlled environment in an office, inside and out of the weather, lawn furniture, automobile components interior or exterior, etc.?
- Do you still have the necessary knowledge to operate your phosphating system properly?
- How much will the vendor charge you to shot blast them?
As already noted, the quality of phosphating is superior without doubt. The cost of shot blasting might well be less, but it's very hard to say without knowing something about your parts. Good luck.
Regards,
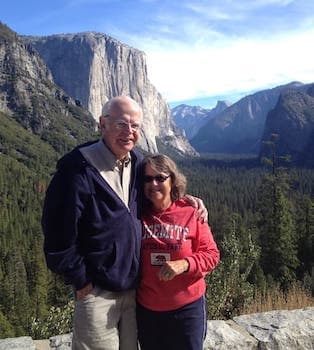
Ted Mooney, P.E. RET
Striving to live Aloha
finishing.com - Pine Beach, New Jersey
Iron plate finishing
My situation: Could you please recommend the best solution (steps) for finishing Iron plates as well as cast iron. Starting from degreasing to phosphating and finally powder coating.
Wilhelm RudolphConsultant - Ho CHi Minh City, Vietnam
July 3, 2018
A. Hi cousin Wilhelm. There is almost never such a thing as 'best', and the most corrosion resistant processes ones are often rejected on the basis of cost anyway. If this iron is used inside a building, you really don't need best. If the shape of the castings is such that pore-free, even-thickness, powder coating isn't possible you may need electrocoating between the phosphatizing and the powder coating for outdoor exposure. If this is an architectural feature, you probably need architectural powder coating. That's why we ask for "your situation". You may also need blasting before the 'degreasing' whether you like it or not.
But for a quick answer, I think William Doherty's posting, 2 paragraphs above yours, covers most of the bases, including the need for a tight specification. Best of luck!
Regards,
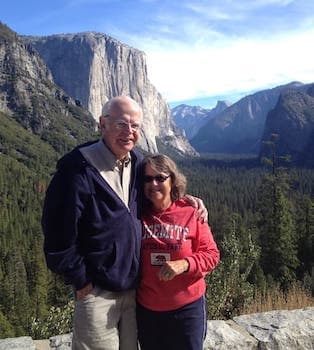
Ted Mooney, P.E. RET
Striving to live Aloha
finishing.com - Pine Beach, New Jersey
July 2018
Q. Hi, We need to choose the best practice for HR/CR components which are 5mm to 20 mm thickness. we have iron phosphating (3 step) facility and would like to add shot blasting facility before that also due to rust & scales. but could shot blast enough to achieve good adhesion & corrosion property? Can 500 hrs be achieved by shot blasting. What will be the overall advantage if we use both processes?
Please help me out.
- Tamil Nadu
February 8, 2019
A. Hi Mohan. Steel should always be phosphated. It is important for paint adhesion, to minimize galvanic hot spots, and to prevent filiform corrosion & undercutting corrosion.
Blasting before phosphating is required if the rusting & scaling is severe enough that the phosphating line cannot practically and reliably remove it. Good luck.
Regards,
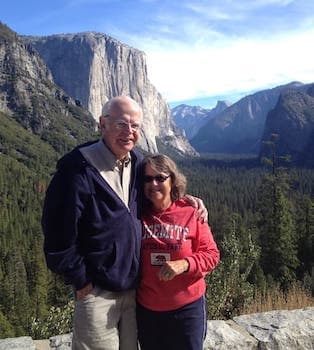
Ted Mooney, P.E. RET
Striving to live Aloha
finishing.com - Pine Beach, New Jersey
February 2019
Sandblasting Versus 5 Step Dipping Process
Q. I am opening a Thermo Coating Plant, PVC Coating Plant and Powder Coating Plant and would like to know the pros and cons of Sandblasting, 5 Step Dipping Process and which process is better? I would also like to know diffs between Thermo Plastic and PVC, and which is better, and is spray cleaning booth advisable.
Regards
Andes
- Cape Town, Western Cape, South Africa
May 20, 2020
May 22, 2020
⇦ Tip: Readers want to learn from Your Situation 🙂
many readers skip abstract questions.
Q. Is there pre-treatment required before powder coating for Electrogalvanized steel (cold rolled steel)?
If yes, please which process can we do?
Please advise us. Thank you.
- Coimbatore, Tamil nadu, India
A. Hi Janakar. Pretreatment is required, and zinc phosphating is best.
But you haven't yet told us who you are, or what you company does, or what the components are, or about their exposure and corrosion resistance needs, so it's hard to offer advice about whether you can practically do it in-house, or whether you must farm it out, or whether you must settle for "Plan B", a less satisfactory pretreatment. Good luck.
Regards,
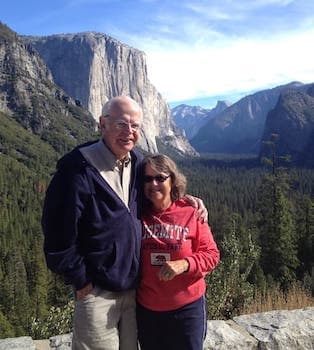
Ted Mooney, P.E. RET
Striving to live Aloha
finishing.com - Pine Beach, New Jersey
May 2020
Q, A, or Comment on THIS thread -or- Start a NEW Thread