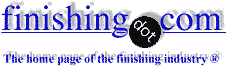
-----
Is DIY home sputtering possible?
Q. I have been able to silver glass using ⇦ on eBay or Amazon [affil links] , potassium hydroxide [affil links] a little dextrose [affil links] and some ammonia ⇦ on eBay or Amazon [affil links] - it works great other than the tarnishing problem.
However I need to re-coat a very hard-to-get projector bulb - as although I can insert a new discharge capsule into the reflector, the aluminium coating inside the glass has come away quite extensively in places.
I have tried silvering with my usual mixture - and despite my best efforts, it "doesn't take" - the glass (quartz?) is squeaky clean (acetone ⇦ on eBay or Amazon [affil links] Warning! Flammable! washed).
I am wondering if there is a way to sputter metal on in a DIY situation - I know I have done it with copper before by mistake - when VERY heavy duty switchgear has "flashed" a fine copper sheen onto plastic cases. Quite impressive.
I have a vacuum pump - though of little use as I do not have the resources to easily make a vacuum chamber - I do however have access to aluminium bar, foil, powder and "dust". I can also provide arcs or heat easily enough. So far however my experiments have not been terribly impressive.
I am sure the right answer is "send it to an optical house and pay the man" - but at least part of this is "wanting to be able to do it myself" - even if it is not worth it from a time - v - money point of view.
Any helpful suggestions would be welcome - or funny but unhelpful ones too :)
Mark Tibberthobbyist / a little experience - Wellingborough, Northamptopnshire, England
2007
A. Mark
By all means have a try. The 'official' kit costs £ thousands but for a one off you may be able to knife & fork it.
The good news is that if you fail, it is unlikely to harm your reflector.
Sputtering requires 5 kv or so of DC but aluminium is easily deposited by simple evaporation. You need a stout tungsten wire filament and hang some small "U"-shaped pieces of pure Al wire on it. Deposition is 'line of sight' so position it with care. You will need better than about 10 -2 torr of vacuum and your vacuum chamber could be possibly a short piece of copper pipe.
Ramp up the current on the filament to first melt and then evaporate the Al. This is much easier if you have a glass vacuum chamber so that you can watch the proceedings - but use a safety screen (perspex sheet) in case of implosions.
Good luck. Please let us know if it works
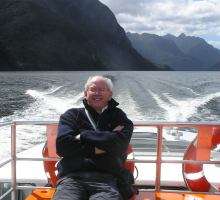
Geoff Smith
Hampshire, England
Q. I'm actually working on a DIY sputter coater at the moment. I don't know how old this article is, but I'd be interested to see if you went along with it.
Right now I'm stuck trying to get the chamber together, but I'm relatively confident that my gun and power supply will work. How big of an area are you coating?
Everything I'm using is off the shelf, nothing fancy except for the vacuum pump. You need to get down to around .1 Torr for most sputtering. I generally run at .07 Torr.
//Glis
- Mesa, Arizona, USA
February 29, 2012
Argon regulator for desktop sputter coater
Q. Determined to get into sputter coating on a limited budget, I purchased a desktop sputter coating machine as salvage. I'm in the process of restoring my 1980s Polaron E5200, and the plan at first is to use it for creating small beamsplitters. My ultimate aim is to be able to apply decent MgF2 coatings to camera optics -- and to that end, I got a RF power source and I'll either make a new water cooled sputter head or adapt another salvaged water cooled head I recently acquired.
Anyway, there is something that concerns me. To start with, I'll be using high purity argon (but not ultra high lab quality) and understand it has to be fed to the vacuum chamber at about 5 psi. While I'm happy that most regulators are capable of doing that very well, I'm not so sure how they work under vacuum conditions. Obviously catastrophic failure of the contents of the gas bottle suddenly getting dumped into the vacuum chamber wouldn't be a good thing. I wondered if anyone had experience of this?
Alan Starkiecameraworks-uk, co-owner. Optical repairs. - Manchester, Lancashire, United Kingdom.
February 2, 2018
A. You cannot connect the regulator to the vacuum chamber directly. Either a needle valve or a mass flow controller should be fixed to the vacuum chamber. This is essential to control either the pressure in the chamber or the gas flow rate through it. These are important parameters to control during sputtering. This cannot be done with a regulator alone.
H.R. Prabhkara- Bangalore, Karnataka, India
Thanks. The unit does contain a needle valve as standard but I'll probably hook up a flow rate monitor of some sort too. I was more concerned that normal regulators, presumably designed to work at atmospheric pressures might fail under vacuum :)
cameraworks-uk - BURY, Lancs, UK
! It is absolutely possible to do your own PVD -- and due to the trends of old-fashioned but functional technology, homemade gadgets, and all the big silicon valley companies sending their junk to eBay , it can be surprisingly inexpensive -- but still requires a significant startup investment in vacuum pumps.
Like electroplating, trying to develop the ability to do this yourself to "just do something" is probably a nonstarter except in some specific situations. However it may be a bit more favorable for some cases due to the extreme cost of commercial PVD services.
I have successfully sputtered silver and copper oxide (reactive sputter) onto glass and paper.
- San Jose, California, USA
November 3, 2019
Q, A, or Comment on THIS thread -or- Start a NEW Thread