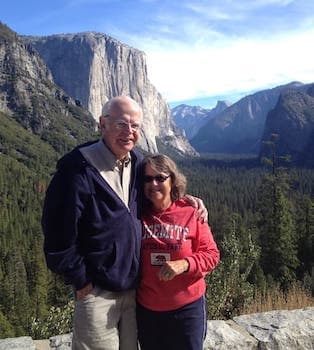
Curated with aloha by
Ted Mooney, P.E. RET
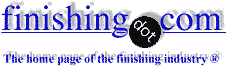
The authoritative public forum
for Metal Finishing 1989-2025
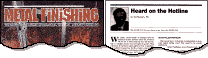
-----
If pickle is strong enough for adhesion, can't get Hydrogen Embrittlement Relief
I am having a problem with small spring clips. They are heat-treated steel, that must be zinc plated, baked and clear chromated. I do not have an electrocleaner in-line, so when I soak clean, then remove the scale with 40-50% muriatic acid, then zinc plate - perfect adhesion. However, after baking at 400 degreeF for 8 hrs, part breaks from hydrogen embrittlement. Tried a less aggressive 30% muriatic acid to decrease hydrogen - parts do not break so no hydrogen present, but get poor adhesion. Any advice?
Shane MooreProcess Engineer - Clarkesville, Georgia, USA
2007
2007
Shane,
What is the strength or hardness of the steel? Spring steels tend to have high tensile strength and high hardness, especially in the fully heat treated state.
How quickly are you getting the parts in the bake oven? Ideally they should be in the oven within 1 hour and certainly should be in within 4 hours. Note embrittlement damage can happen rapidly and once damaged is irreversible so getting the parts in the oven as soon as possible is critical to success of the de-embrittlement operation.
It also sounds like your bake time is too short. For ultra high strength steels (usually considered to be steels with a tensile strength of 1800 MPa (260 ksi) or above) you should be de-embrittling for 24 hours at 375-400 7deg;F, for high strength steels (usually considered to be steels with a tensile strength of 1450-1800 MPa (210-260 ksi)) 18 hours is usually considered sufficient. Note these times are minimums, anything over and above these times will not be detrimental, less than these times are generally considered unsafe.
Aerospace - Yeovil, Somerset, UK
Brian is kind! For your material, it should be in the oven ASAP and not longer than 15 min after the final rinse and it should not be allowed to sit idle in any tank after the acid pickle. One answer is an abrasive blast after heat treat. Another solution is to use a vacuum furnace or a reducing atmosphere furnace with an inert gas cool down. Stainless steel baggies are not practical for your parts.
I would certainly try a rust removing formulation of the electroclean with periodic reverse. One that contains cyanide would be optimum, but most facilities are paranoid about it being in the shop.
- Navarre, Florida
2007
Thank you for the responses. The parts go directly in the oven as soon as they are dryed (around 15-20 minutes after plating). What do you guys think about using anodic current in the 35% HCl? Do you think there would be less hydrogen embrittlement since oxygen would be generated at the surface of the part instead of hydrogen (when cathodic)? I was thinking the gas scrubbing would help remove the heat scale.
Another thought... precleaning in a vibratory bowl with ceramic media small enough to affect the inside of the clip, removing the heat scale on both sides of the part. I have the capabilities, just want advice on this idea.
- Clarkesville, Georgia, US
2007
Both of your ideas are viable. I like the vibratory the best.
Another thought, do not rack the parts under any tension as they will tend to fail during unracking or fairly soon afterwards.
- Navarre, Florida
2007
Got to agree with James, like the idea of a vibratory method, eliminate the possibility of hydrogen embrittlement. Plus has the benefits of saving on the lengthy de-embrittlement times.
If you were to go with the HCl method I think you would need to enter the bath live, with a slight trickle of current. HCl is notorious for hydrogen embrittlement so the shorter time in the acid without current the better. The vibratory method sounds neater though.
Aerospace - Yeovil, Somerset, UK
2007
Q, A, or Comment on THIS thread -or- Start a NEW Thread