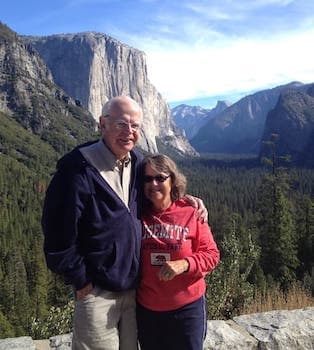
Curated with aloha by
Ted Mooney, P.E. RET
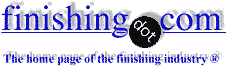
The authoritative public forum
for Metal Finishing 1989-2025
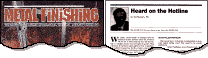
-----
Nylon or Powder Coating for bicycle parking racks?
We produce Bicycle Parking. Are there any comparative studies of nylon, powder coated, or galvanised finishes for steel bicycle racks, and/or shelters? Many of the powder coated racks we see have the coating flaking off. Nylon (with a zinc primer) seems to offer a good mix of advantages. Any issues? The racks are subject to heavy use, as they are outside, and hit frequently by steel parts of bicycles!
1) Photo of a galvanised bicycle rack, with a powder coating. Typical site - finish coming off, looking very poor.
We prefer to use nylon (2 coats, then baked in an oven), over an electro-statically applied zinc primer - also baked on. However, we do not have any comparative quality information.
2) On a different topic, what is the best way to ensure a good finish if a customer requests galvanised racks. The quality we get back is very variable.
Peter DavenportCompany - Hampshire, UK
2007
If you don't nominate a standard for the galvaniser to comply with, then you probably will get variable results. If no particular quality standard is requested, then no particular quality standard will be supplied.
You have a perfectly good galvanising standard in BS ISO 1461, so I suggest you use it to state what you want, then hold the galvaniser to the contract by refusing to accept non-complying product.
The various organic coatings you mention won't stand up too well to the mechanical impacts, scrapings, etc that are part of typical use of a bicycle rack, even if the racking is not exposed directly to the sun and rain.
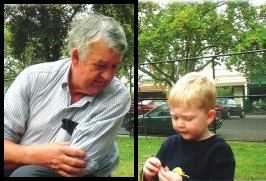
Bill Reynolds [deceased]
consultant metallurgist - Ballarat, Victoria, Australia
We sadly relate the news that Bill passed away on Jan. 29, 2010.
2007
2007
The galvanizer has little or no influence on the finish of powdercoated galvanized steel.
The pictures you posted suggest inadequate pretreatment of the galv by the powdercoater. (I am involved in both, so no axe to grind between Galvanizing and powdercoating).
Unless a competent pretreatment of perhaps 10 stages is performed on the galv then the powder will not stick.
Doing it right will allow the coater to offer an adhesion guarantee of up to 25 years.
There is often an argument between a galvanizer and a powdercoater about the finish of the galv being unsuitable for the powdercoating. A good solution is find a coater that does both under one roof, then any issues stay there, and the customer does not require tobe a mediator between 2 subcontractors.
The pretreatment might involve either chromate or zinc phosphate. Do NOT settle for "T Wash" or some other excuse for a pretreatment.
ISO 1461 is the standard for galv in the UK, and you should specify BS13436 for the powdercoating. If possible use an applicator who is approved by one of the major powdermakers, but ensure that its an approval on Galvanized steel. (Some who are approved for aluminium only will just state "approved applicator").
To get the best finish on powder over galv, its necessary to fully linish the galvanizing. Most powdercoaters will not do this, but you should be able to expect a finish as good or very nearly as good as on aluminium. A coater who does both galv and PC will do this. There are several in the UK. All of the above applies to either polyester or nylon PC over galv. Choosing nylon seems unusual for this application. Did you want its lubricity? Or its slightly warmer touch? If the latter you could also use plastic. But if you want long lasting hard to take the knocks (I'd guess this for a bicycle rack), then I suggest polyester.
Using a zinc primer powder with a top coat over has the disadvantage of not being metallurgically bound to the steel. A scratch through the powder will still rust. Your image shows no signs of rust, just a lack of adhesion. (pretreatment lacking)
To demonstrate toughness of PC over galv, I once ran a competition. The challenge was using a coin, to scratch through the PC layer (a single coat) and reveal the zinc of the galvanizing. Prize was a bottle of whisky. Of the 300 tries, only 22 succeeded. With that incentive, PC was too tough.
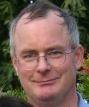
Geoff Crowley
Crithwood Ltd.
Westfield, Scotland, UK
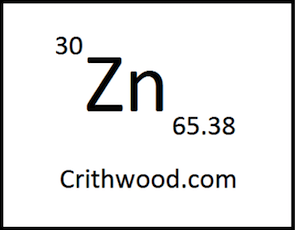
2007
For nylon powder coating you can try and use a product with the brand name Rislan manufactured and sold my Arkema of France. You can obtain coating thickness of 200 microns. I do not have the UV exposure performance data with me but I am sure the supplier will be able to help you with that.
This is really an encapsulating layer and could be an alternative to thin film powder coating.
Mohali, Punjab, India
2007
Hi Peter,
I go along with the evaluation that Geoff has already submitted - that the powder adhesion defect is caused by inadequate pretreatment.
Anoprime was specifically formulated for use under powder coating. Our customers use it on ferrous and non-ferrous substrates. The one thing that keeps coming back to us is "how good it is on galvanized metal". As the mf, all I can say is that one of the first coating jobs (some seven years ago) that it was used on as a pretreatment for galvanized substrates (prior to powder coating) was crash barriers. These were destined for the heavy goods parking area of the channel tunnel and to-date we have not been informed of any problems.
Regards,
Birmingham, United Kingdom
----
Ed. note: Generic names of the types of coatings, please, readers -- not proprietary names -- or this advertiser-supported website may not exist next time you look for it :-)
Q, A, or Comment on THIS thread -or- Start a NEW Thread