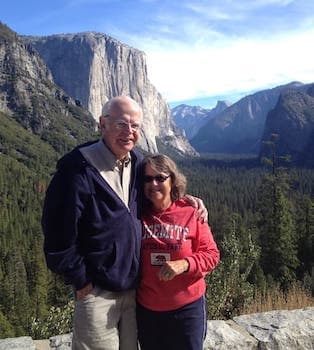
Curated with aloha by
Ted Mooney, P.E. RET
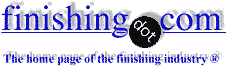
The authoritative public forum
for Metal Finishing 1989-2025
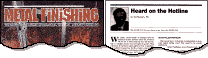
-----
Nickel plating on Beryllium Copper
Q. I am planning to use a part made from Beryllium copper for agricultural use. But I am wary of the ammonia ⇦ this on eBay or Amazon [affil links] fertilizers used in agriculture since it has a tendency to corrode Beryllium copper. Is there any remedy to protect Beryllium Copper from Ammonia?
Ranjit Nair- Bangalore, KARNATAKA
March 1, 2021
A. Hi Ranjit. A typical way to treat beryllium copper is to electroplate it for a measure of corrosion resistance plus good electrical conductivity, or optionally to add gold plating on top of that for best conductivity. Electroless nickel can offer greater corrosion resistance and wear resistance at the cost of some of the conductivity. Unfortunately, your inquiry is rather vague, not telling us what the component is, why it's beryllium copper, what properties you need to retain, or what the exposure situation is except than agriculture and ammonia is involved. So I can't even say whether a heavy coating of plastisol or some other totally different technology might be better for your needs. Give us some data please :-)
Luck & Regards,
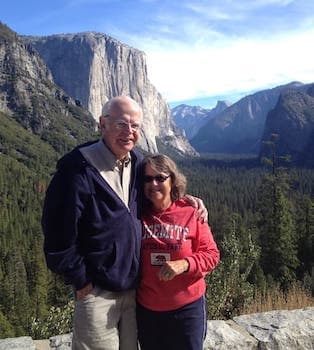
Ted Mooney, P.E. RET
Striving to live Aloha
finishing.com - Pine Beach, New Jersey
March 2021
⇩ Related postings, oldest first ⇩
Q. I need to plate nickel on Beryllium Copper. I have a Wood's Nickel Bath and also a Nickel Sulfamate Bath. Question 1 - Does the Beryllium Copper need to be plated with Wood's Nickel before the Nickel Sulfamate? Question 2 - Does the Beryllium Copper need any special cleaning before nickel plating?
Thanks.
Engineering - Laurens, South Carolina
2007
A. The only thing special about beryllium copper is that it must be first plated in an acid solution. The only reason for "striking" is to leave copper in the sewer strike solution so that the main plating solution "sees" nickel instead of copper hence preserving the purity of your main plating solution. Just be sure you plate in an acid solution first.
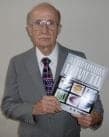
Robert H Probert
Robert H Probert Technical Services

Garner, North Carolina
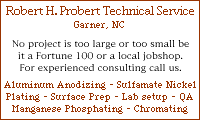
2007
A. A process I have used in the past is as follows:
1) Degrease the part(s)
2) Anodic alkaline clean
3) sulfuric acid dip
4) Sulfamate Ni plate
This process ensures a copper rich surface prior to Ni plate, and the removal of Be compounds that form on and just below the surface of the substrate. It is always a good idea to double check with your Ni supplier regarding cleaning and activation cycles. I have seen and plated BeCu successfully without a Wood's Ni strike. Good Luck!
Process Engineer - Syracuse, New York
2007
A. Hi Martin,
If the component is not having complex geometry and plain surface then Wood's nickel strike can be attempted.
Because the covering power of Wood's nickel is poor, when the job is of complex geometry I prefer the sulfamate strike as otherwise the bath attacks the copper exposed and copper metal builds up in the bath. Sulphamate bath also keep it at 50 °C and max of 30 gm/lit of boric acid only to get fairly good coverage.
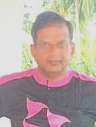
Vasudevan Narayanan
- Chennai, Tamil Nadu, India
April 8, 2011
April 1, 2015
Q. Hi,
We have started beryllium copper parts for gold plating, process details below:
solvent degreasing
electrocleaner (cathodic)
sulfuric acid dip (20%)
acid copper plating -- 4-5 microns
nickel sulfamate plating -- 3-5 microns
activation bath -- citric acid
⇦ this on
eBay
or
Amazon [affil links]
gold plating
dry
oven -200 °C 1 hour.
Here, after two successful load/production, now I am facing blister issue in Nickel plating. It's barrel plating, small sheet metal parts.
I changed new nickel bath also, but still problem not solved,
nickel bath
Ni -- 58 g/l
pH 3.8-4
boric acid -- 41 g/l
chloride -- 9
Please suggest on this process any help to solve this issue.
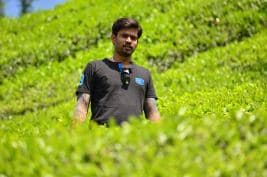
m. karthikeyan
- Bangalore, Karnataka, India
One factor to examine is the rinsing. Barrel plating can allow small drops of solution to be trapped in certain regions and unless very good rinsing and drag-out is performed there can be defects such as you described. Too many parts in a barrel can also be a factor. I would be sure to use a triple cascade DI H20 rinsing system and probably spray rinse as well whenever possible. Suppose two parts are nestled closely in the barrel and don't move about much. Suppose they have a couple of surfaces either in contact with each other or very, very close. In this circumstance, liquids may remain on the given surfaces and then when the barrel is brought to the next tank the excess solution is not immediately diluted into the tank but stays on the surface long enough to cause a defect/blister.
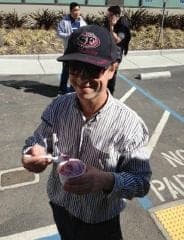
Blake Kneedler
Feather Hollow Eng. - Stockton, California
April 8, 2015
![]() |
A. Hi. - Penang Malaysia April 9, 2015 April 9, 2015 A. Good day Karthi. Lab Tech. - Whitby, On, Canada April 9, 2015 Q. Thanks for the input. ![]() m. karthikeyan [returning] - Bangalore ,Karnataka |
April 9, 2015
A. It is important to know if the blistering is between the base and the nickel - a cleaning problem, or between the nickel and the gold - a nickel passivation problem
Solvent cleaning is good
Soak cleaning should be sufficient - electrolytic cleaning does not work well in barrel plating
Rinse
sulfuric activate
Rinse
Nickel plate A standard watts nickel bath is all you need
Dragout
Rinse and immediately
Gold plate. Any delay will allow the nickel to passivate and cause poor adhesion
Dragout
Hot Deionised rinse
Warm air dry 200C is far too hot but will certainly show up any adhesion problems as you have seen.
Beryllium copper can have a Be rich phase at the surface that makes it extremely difficult to plate onto. You may need a light microetch like ammonium persulphate if this happens.
Actually, plating Be/Cu is easy. It is heat treating Be/Cu springs that causes sleepless nights!!
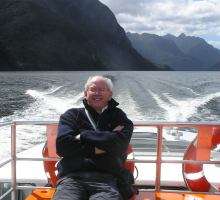
Geoff Smith
Hampshire, England
April 10, 2015
Q. Thanks all for the input,
Ya, I checked blister after gold stripping; it's in nickel layer only. For confirmation I stripped nickel layer also; no blister in copper layer.
After plating not observed any blisters; only after oven curing 1 hour at 200 °C we found blisters. It's the sheet metal (small size -square) parts, most of issue found on the sharp edge area only.
And the raw material was imported from France; after stamping they did heat treatment -- I have report for that.
And after acid copper introduced 10% sulfuric acid activation also, after plating all rinses and next process are quick move only, not given time to passivate the parts.
Dear Mr. Smith,
As per customer specification:
Copper 4-5 microns have to plate and nickel sulphamate 3-5 microns and gold 0.3-0.7 microns.
After plating oven 1 hour at 200 °C.
And I cross checked after copper plating; I kept some samples at oven 200 °C, no blister found. But same lot after nickel found blisters; I have a doubt with current parameters, for nickel going to apply 0.2 amps/dm2 -- will update after trial.
Again before copper plating going to introduce phosphoric acid etching, after that 20% sulfuric acid dip, acid copper and nickel.
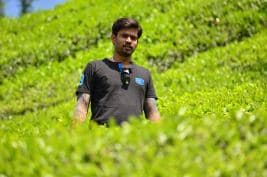
m. karthikeyan [returning]
- Bangalore ,Karnataka
Q, A, or Comment on THIS thread -or- Start a NEW Thread