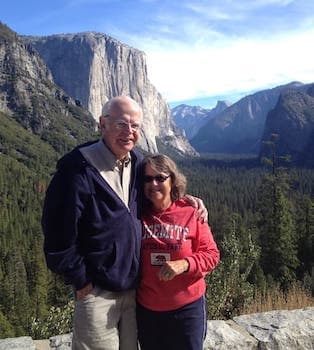
Curated with aloha by
Ted Mooney, P.E. RET
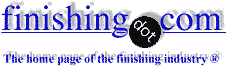
The authoritative public forum
for Metal Finishing 1989-2025
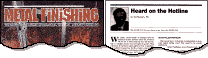
-----
Ball milling to reduce hexavalent chromium to trivalent
Q. It is claimed by a company producing chromate chemicals that it is pretreating the chromite ore processing residue from a high lime-soda process in a ball mill using ferrous chloride as a reducing agent. Does it work? The regulatory limit for disposal of the waste in a landfill is 0.5 mg/l of hexchrome (TCLP). Does this process work at all for the highly alkaline waste at about pH 12?
K. Babu RaoEmployee - Hyderabad, AP, India
2007
A. Chromite contains trivalent chromium, not hexavalent chromium, which would be chromate. If there is no hexavalent chromium present in this waste, then no low pH chemical reduction step would be needed.
Lyle Kirmanconsultant - Cleveland Heights, Ohio
A. Probably, no to both questions. The waste must be properly tested for hexavalent chromium, both before and after the proposed treatment. Test fully digested samples, as treated solids may pass short-term leachate tests but resume leaching over time.
For other readers, the post refers to sodium dichromate production. From Shreve's Chemical Process Industries
⇦[this on
Amazon
or
on AbeBooks affil links], 5th Edn., pp. 364-5:
A schematic diagram shows 3-stage leaching, with the water flow counter to the solids.
The chromite ore processing residue (COPR) is actually a cement contaminated with hexavalent chromium typically at 0.1-1 wt%. It is difficult to treat, especially from silicaceous ores. Even with pH reduction, COPR treated with ferrous iron has resulted in soil and water contamination. For some background info, complete with scary yellow soil photographs, read 'Chromite ore processing residue in Hudson County, New Jersey':
http://www.pubmedcentral.nih.gov/articlerender.fcgi?tool=pubmed&pubmedid=1935843 updated by editor Sept. 2023:
https://www.ncbi.nlm.nih.gov/pmc/articles/PMC1519394/
Some observations (guesses) on the original post: Ball milling suggests that the grinding after roasting is inadequate. The residual pH of 12 suggests that the leaching steps are inadequate. Finer grinding prior to leaching may improve yield and eliminate the need for ball milling later. Counterflow leaching may further improve yield as well as lower both pH & Cr+6 content of the waste. For Cr+6 treatment, some studies have found success using ferrous iron + sodium hydrosulfite
⇦ this on
eBay or
Amazon zincaffil links] ; another, with calcium polysulfide. A small particle size is important for minimizing the residual Cr+6.
Do an Internet search for chromite ore processing residue. There are many recent studies and patents. A sampling --
"Laboratory batch studies indicated that ferrous iron (as ferrous sulfate
⇦ this on
eBay or
Amazon [affil links] ) in the presence of sodium hydrosulfite was highly effective in treating the chromite ore":
http://www.epa.gov/ada/research/waste/research_04.pdf updated by editor Sept. 2023:
https://web.archive.org/web/20061002164604/http://www.epa.gov/ada/research/waste/research_04.pdf
'Calcium polysulfide remediation of hexavalent chromium contamination from chromite ore processing residue,' M. C. Graham et al., Sci. Total Environ. p. 32-44 (July 2006). [abstract is free, $30 for complete article] http://www.ncbi.nlm.nih.gov/sites/entrez?cmd=Retrieve&db=PubMed&list_uids=16442591&dopt=Abstract updated by editor Sept. 2023:
https://pubmed.ncbi.nlm.nih.gov/16442591/
International patent application: 'METHODS OF TREATMENT OF CHROMITE ORE PROCESSING RESIDUE' (WO/2006/031590) Describes failures of conventional treatment with ferrous iron and gives improved methods:
http://www.wipo.int/pctdb/en/wo.jsp?IA=WO2006031590&DISPLAY=DESC updated by editor Sept. 2023:
https://patents.google.com/patent/WO2006031590A1/
'The Soda-Ash Roasting of Chromite Ore Processing Residue for the Reclamation of Chromium; (2001) [1st page is free]
"The residue generated from the lime-based process contains 0.1 to 0.2 pct hexavalent chromium and the treatment to reduce the Cr6+ concentration from this residue is very difficult. The landfill sites of these residues are now major sources of Cr6+ contamination."
http://doc.tms.org/ezMerchant/prodtms.nsf/ProductLookupItemID/MMTB-0112-987/$FILE/MMTB-0112-987F.pdf?OpenElement updated by editor Sept. 2023:
https://link.springer.com/article/10.1007/s11663-001-0087-6
'Long-term treatment issues with chromite ore processing residue (COPR): Cr6+ reduction and heave,'
updated by editor Sept. 2023:
https://www.sciencedirect.com/science/article/abs/pii/S0304389407000386
and 'Assessment of calcium polysulfide for the remediation of hexavalent chromium in chromite ore processing residue (COPR),'
updated by editor Sept. 2023:
https://www.sciencedirect.com/science/article/abs/pii/S0304389407000374
both articles in Journal of Hazardous Materials Volume 143 (17 May 2007) [abstracts free, $30 per complete article].
http://www.sciencedirect.com/science?_ob=PublicationURL&_tockey=%23TOC%235253%232007%23998569996%23651259%23FLA%23&_cdi=5253&_pubType=J&view=c&_auth=y&_acct=C000050221&_version=1&_urlVersion=0&_userid=10&md5=ad542b9fcc484369e9dce5fc342b4664
- Goleta, California

Rest in peace, Ken. Thank you for your hard work which the finishing world, and we at finishing.com, continue to benefit from.
Ed. note: The finishing industry lost one of its greatest resources when Ken passed -- the least we could do was update the broken links.
Thank you Ken Vlach for a detailed response. I have read some of the articles you have referred to.
- Hyderabad, India
2007
Q, A, or Comment on THIS thread -or- Start a NEW Thread