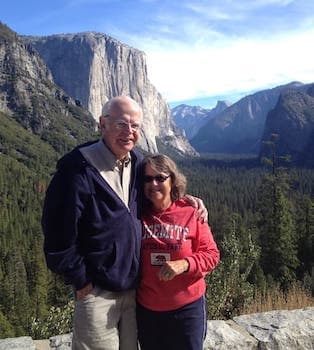
Curated with aloha by
Ted Mooney, P.E. RET
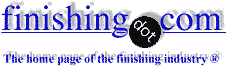
The authoritative public forum
for Metal Finishing 1989-2025
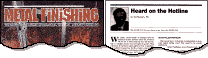
-----
Flaking nickel plate when grinding, wheel and/diamond suggestion needed ASAP
Grinding brushed nickel and having problems with peeling,and bubbling. Using a C36J8, 16"x1" silicone carbide crystalline wheel and supposedly a grade 3 diamond, both provided by employer. Diamond is showing 2 1/2 10ths wear on a dress. Using a Karstens OD Grinder, Running 90 RPM's on a 2" diameter.
Suggestions were to use a SG wheel. What can I can I do nothing is working?!
Grinder - Massachusetts
2007
At an airline plating conference many years ago a talented panel stated: 1. If you are thinking about grinding nickel-do not. 2. If you need to grind nickel-do not. If you are going to do it anyway, use a wheel that breaks down fairly rapidly, use a gross excess of cutting fluid and take thin cuts, dressing the wheel very often. That said, can you diamond turn the part and only grind the last half a thou a side? A larger diameter wheel would probably help some, with the same surface speed. James Watts
- Navarre, Florida
2007 -- 1st of two simultaneous responses
2007 -- 2nd of two simultaneous responses
Before we change the grinding wheel, let's study the metallurgy of the nickel plating.
What is the base metal? Leaded?
What kind of nickel electroplate? Bright? Low Stress Sulfamate? What is the surface preparation prior to plating?
Properly bonded low stress electroplated nickel is ground all the time with very little adhesion problems.
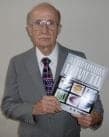
Robert H Probert
Robert H Probert Technical Services

Garner, North Carolina
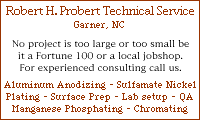
Nickel has too many different metallurgies and mechanical properties when brush plated (BP). It can be very hard, brittle, highly stressed but with an innocent coarse grain face that invites you to give it quick heavy passes. The stone just clogs and starts to bump out and burn. Or it could be very fine grained, almost bright and tough, so damn stubborn it prefers to flake than to let go with the cut. Not to talk about bonding. This is the "issue" with BP. Blame it on the plater, the chemicals, the general processing conditions, the lack of information about base metal, whatever. James advise is very wise. Don't let the stone clog and the heat develop at the point of contact. Make sure adhesion is optimum. G. Marrufo-Mexico
Guillermo Marrufo- Monterrey, Mexico
2007
Q, A, or Comment on THIS thread -or- Start a NEW Thread