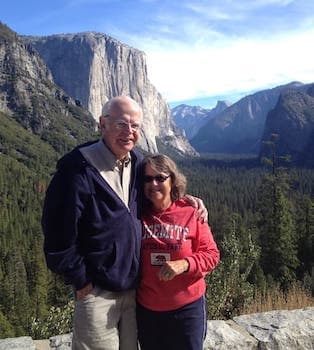
Curated with aloha by
Ted Mooney, P.E. RET
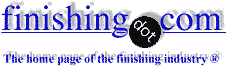
The authoritative public forum
for Metal Finishing 1989-2025
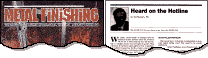
-----
Tumble finishing stainless steel plate and screws
2007
My UK based company is developing a range of very high end leather on carbon fiber cases for guitars, violins and laptops.
The structural element of the handle is a 316 stainless steel strip approx. 3mm thick x 30 mm wide x 300 mm long. This strip has a 20mm wide x 270mm long x 1mm deep recess into which we lay a strip of leather which matches the exterior of the case. The plate has 4 countersunk holes to take 4mm machine screws which attach the whole handle to the case.
Currently the strip is brush finished and I am using stock machine head screws with allen key sockets. I am not satisfied with this look
- it does not match the quality of the rest of the case. We have tried hand polishing the strip but this gives too shiny a look and it is v difficult to polish the heads of the screws to match the finish on the strip.
I want to give the stainless steel quality finished which is discreet
- not flashy - and which will look good after many years use.
My current thinking is to give the steel a very high quality matte finish - probably by tumbling. I hope I can tumble the machine screws as well so the heads match the finish of the plate.
I am looking for advice on 1) how to achieve the finish on the steel
- is tumbling the best route? 2) Should any such processing be done before or after the recess is cut ? 3) Can I apply the same process to the machine screws so the heads have a finish which exactly matches the strip?
Thanks
product designer - Exeter, Devon, UK
Even though you furnished visuals, it is difficult to see the exact texture you are trying to match. If you are considering mass finishing and are looking for a satin/semi-brushed surface finish, I would suggest a dry process and a product that we call 6A. It is about 60% organic product (mostly wood sawdust) and 40% inorganic (pumice). Because of its light weight (about 30-35#'s/cu.ft.) it is a slower process than a wet system. There are other alternatives, but it does give an excellent brush like finish. We stock it.
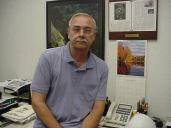
AF Kenton
retired business owner - Hatboro, Pennsylvania
2007
Q, A, or Comment on THIS thread -or- Start a NEW Thread