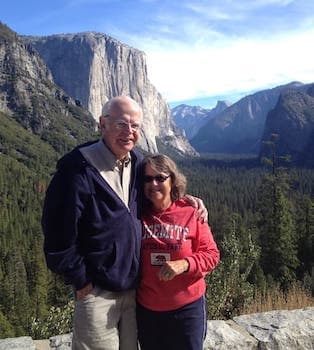
Curated with aloha by
Ted Mooney, P.E. RET
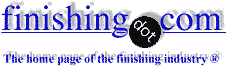
The authoritative public forum
for Metal Finishing 1989-2025
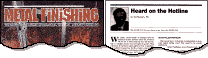
-----
Can I use etching on 316L to remove buildup on micro end mills?
2007
Howdy,
I'm a student at Texas A&M University and I am doing my thesis on micro-machining (tools 1 mm in diameter or less). I am machining stainless steel 316L, but I need a way to remove the build-up on the end-mill prior to measuring the tool wear. I have researched this site and know that several of you readers are very familiar both with 316L and etching.
The two solutions I have been able to obtain thus far are using oxalic acid (concentration unknown) or 100 ml ethanol 96%, 100 ml HCl 32%, and 5 g copper II chloride.
I am a mechanical engineer and have no idea if either of those solutions will work or if anyone has a better idea. Any help would be much appreciated. Thanks in advance,~ Meagan
student - College Station, Texas
First of two simultaneous responses --
Hard to say. Most etchants that dissolve stainless steel will also attack high speed cobalt base alloys or tungsten carbide which is "glued" with nickel or cobalt. Perhaps a reverse treatment in an alkaline cleaner if burrs are not totally welded. Just a thought, why don't you use
TiN coated tools? They resist build-up.
Monterrey, NL, Mexico
2007
Second of two simultaneous responses -- 2007
Follow up to the question:
I have also read that ferric chloride
⇦ this on
eBay or
Amazon [affil links] with small amounts of HCl will work, but I don't know concentrations or temperatures however.
Thanks again, ~Meagan
- College Station, Texas
The beauty of 316 is that it is more resistant to acids than most SS and for anything except pure carbide that the drills might be made of. That is bad for you, however.
You might try using an ultrasonic jewelry cleaner
⇦ this on
eBay
or
Amazon [affil links] . Harbor freight sells small ones a lot cheaper than the laboratory supply houses. You can set a beaker [beakers on
eBay
or
Amazon [affil links] with your brew of choice in the tank with the water at the prescribed height. This is to protect the ultrasonic tank as they are normally cheap SS. If you are only concerned about the tips of the drill, find a SS rack to put into the tank to elevate the beaker. The beaker will float if it does not have enough liquid and drills in it and it will tip over. Ultrasonics will speed up the process by several fold over just immersion.
- Navarre, Florida
Thank you both for the advice. Unfortunately, I can't use TiN coated tools because they also help prevent tool wear, which is what I'm trying to induce so I can model it. I think the ultrasonic cleaner is a great idea and I already have a setup, but I'm still lost with what acid to use. I have a few options now and will run some experiments and post any results I might find. Thanks again, ~Meagan
Meagan Makarenko- College Station, Texas
2007
Ultrasonic cleaning does not basically depend on acids or alkalies to clean but rather on a scrubbing action carried out by the bubbles that form on the object surface. It works well to remove loose particles and contamination but will not be very effective if the metal chips are welded to the tool. G. Marrufo-Mexico
Guillermo MarrufoMonterrey, NL, Mexico
2007
That is true, BUT it will speed up the chemical reaction because it rapidly refreshes the chemical at the surface by basically eliminating the boundary or diffusion layer.
James Watts- Navarre, Florida
2007
Q, A, or Comment on THIS thread -or- Start a NEW Thread