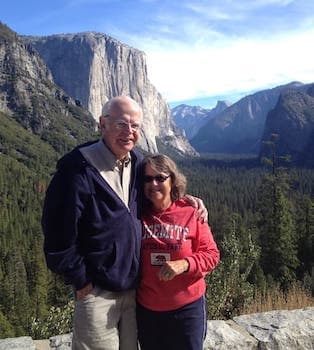
Curated with aloha by
Ted Mooney, P.E. RET
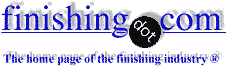
The authoritative public forum
for Metal Finishing 1989-2025
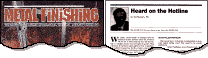
-----
Maximum Corrosion resistance for Minimum Thickness Needed
We sell volumes of fasteners that we plate and coat and have a requirement for improved corrosion resistance. I would like to achieve the most number of cycles of Kesternich testing for a thickness of no more than .0009 inches. What do you suggest?
Peter MorganFastener supply - Brampton, Ontario, Canada
2007
Plating thickness is not uniform, but is greater on the thread crown than on the root. I hope someone corrects me and offers you hope, Peter, but I think .0009" is too low for the minimum thickness of the plating let alone the maximum thickness.
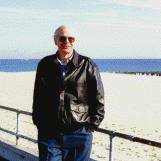
Ted Mooney, P.E.
Striving to live Aloha
finishing.com - Pine Beach, New Jersey
2007
Ed. note: I've corrected myself. Somehow I had read the thickness as .00009 inch :-(
.0009" is not a thin plating; sorry for the misread.
2007
We are a fastener manufacturer who needs to improve the corrosion resistance of our plated/coated fasteners, particularly case hardened mild steel wood screws near the ocean. The test condition of note is the ASTM G85 -A5 test which is cycles of dilute acid and salt sprayed for an hour and then dried for an hour, which is a difficult test. The total coating thickness can not be more than .oo1 inches. The sharp edges of threads can be a problem area for corrosion.
The question is, what would be the best combination of coatings to achieve the best possible test result, i.e., the longest time to any red rusting ?
One of the coatings tried so far that was not good enough is 13 microns of Zinc followed by yellow passivation and leach back with an inorganic aluminium rich topcoat. This only gave us about 1/3 of the protection we are looking for.
Things yet to try would be combinations of plating such as tin-zinc, copper-zinc, nickel-zinc any suggestions or knowledge would be appreciated. Must be commercially available.
Product Engineer - Toronto, Ontario, Canada
Zinc alloy plating will deliver significantly better corrosion resistance than straight zinc. The plating process suppliers should be able to give you laboratory plated samples of zinc -nickel and zinc-cobalt plus chromate which may satisfy you.
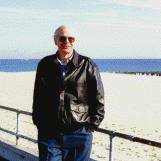
Ted Mooney, P.E.
Striving to live Aloha
finishing.com - Pine Beach, New Jersey
2007
Q, A, or Comment on THIS thread -or- Start a NEW Thread