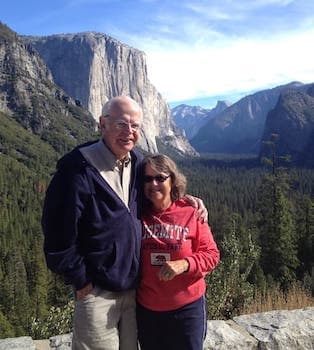
Curated with aloha by
Ted Mooney, P.E. RET
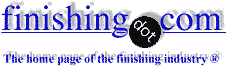
The authoritative public forum
for Metal Finishing 1989-2025
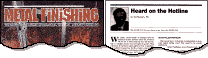
-----
Secondary blast profile
Q. Hi, I would just like to introduce myself. My name is Dean Wilson, I work for a grit blasting and specialized coatings company in Dubai UAE. I am currently working on a project blasting and TSA coating various size dia. pipes. Let me tell you my scenario:- I have fully grit blasted my 12 meter length pipes using garnet 12/25 grade size which is producing an average surface profile of around 106 microns. The ends of the pipe are then masked up approximately 250 mm, balance pipe is then TSA coated with a sealer top coat applied. When loading out of shop the masking tape is removed and a light coat of sealer is applied to the ends of pipes solely for transportation purposes,because once at site these will be welded together and a field joint carried out. Next step, pipes are welded together and re-blasted(same size garnet)the spec requires minimum 100 microns, I can only achieve in the region of 84 to 98 maximum surface profile. Is it at all possible that I am burnishing the existing profile of the first blast, or is there another reason for my dilemma please could you help in resolving this matter.
Many thanks, Dean
Shop supervisor - Dubai, UAE
2007
A. Hi Dean,
The base material may be harder in the weld area and therefore will not 'roughen' up as much and give you as good a profile.
Best regards
- New Zealand
September 10, 2012
Q, A, or Comment on THIS thread -or- Start a NEW Thread