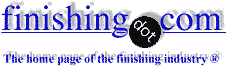
-----
Corrosion Protection Alternatives Free of Hexavalent Chromium
Q. I am looking to provide corrosion resistance for mild steel parts mated with stainless steel or Aluminum surfaces. The parts will be used to connect heavy machinery components to structural steel (think movable bridges). Long life is an important issue. I am currently using a Zinc Chromate finish but would very much like to find an alternative due to the hazards of hexavalent chromium. What alternatives provide similar corrosion protection? What about Zinc Phosphate, Zinc Chromate w/ trivalent chromium, or a Zinc-rich primer covered with an epoxy and then a urethane? Do any of these stand out to you (good or bad)? Thanks.
Benjamin Lee SorensenBridge Engineer - New York, New York
2007
A. Well, you posted this about a week ago. So, I'll put in my two cents.
"Heavy machinery mated to steel surfaces" tells me two things. One: there's vibration. Two: there's going to be a little space in between the two parts where water, the world's most widely distributed corrosive fluid, will hang up.
You say "zinc chromate." Yellow chromate? Olive drab? In what way are you concerned about the health hazards of hexchrome? To the workers handling the parts?
If so, any such hazard is negligible. My best advice to you would be: if it ain't broke, don't fix it. Stay with what you're using.
If you are determined to make a change, I would look at some kind of alloy plating, perhaps zinc-nickel. Trivalent chromates generally, to the best of my knowledge, are used in conjunction with some type of sealer. I am not sure how that will stand up under the kind of service you discuss. For safety's sake, if I were you, I'd want some enhanced protection under it, greater than that afforded by plain zinc.
Zinc phosphate coatings are rarely used as a stand alone surface protection, but as a preparation for painting.
As for epoxy, urethane, and other organic finishes, I'm quite unqualified to discuss them. Perhaps one of the other folks on here will help you.
I hope this has been of some assistance.
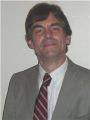
Dave Wichern
Consultant - The Bronx, New York
I would not quite agree with Dave that the personnel hazards are negligible; and, with most of the world moving away from hex-chrome conversion coatings, you will eventually be the target if you stick with it. To address this, employees should be wearing gloves.
But I do agree that you should be among the last to shift to trichromate, not the first. Lots of people are still having plenty of trouble with trichromates, which were rushed to market as soon as they could meet salt-spray test requirements, with no long-term testing of their overall suitability as a replacement. We see many reports of poor paint adhesion, poor chemical resistance in subsequent processing steps, etc. You don't want to be the guy holding the bag with a 25 or 30 year old bridge collapsing because it used a finish whose corrosion-fighting ability had not been adequately tested in real-world conditions. We have very little accumulated history yet, so nobody actually knows yet what will happen in the long run in a thousand and one different situations.
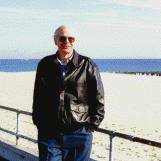
Ted Mooney, P.E.
Striving to live Aloha
finishing.com - Pine Beach, New Jersey
2007
2007
! Ted & Dave, thank you for your responses.
Your hypotheses were correct. First, these contact areas do experience vibrations via the machinery and the bridges themselves. Secondly, these components are exposed and subject to corrosion by precipitation and salt fog.
In our previous designs, we have called for (yellow) Zinc-Chromate shims wherever there is a structural steel/stainless steel (or aluminum) interface. We have found that some suppliers no longer offer this finish. Like Ted said, most of the world is moving away from hex-chrome.
Our options are to:
a) change our design specs to a hex-free alternative.
or
b) find someone that will hex-chrome our parts.
Many industries are under pressure to reduce hexavalent chromium. For example, ocean shipping vessels must have structural/stainless steel interfaces under similar corrosion conditions. What do they do?
It seems like hex-chrome regulations are geared towards (at) manufacturers and finishers. Are there any regulations for industries that purchase and use their products? Could you build an entire bridge out of hex-chromed steel if the steel manufacturer could provide it? Is this a state or a federal issue? Blah blah.
Anyways, the big push to reduce hexavalent chromium has created an equally big void in corrosion protection for many industries. It seems that nothing really stands out as a cost effective safe alternative to zinc chromating parts with hexavalent chromium. If I were a business man I would bet that someone's going to hit it big with a safe equivalent to hex-chrome. Until then maybe I'll stick with the latter for safety's sake . . .
Engineering - New York, New York
Q. Ted, you mentioned that people using trivalent chrome are facing some issues. Can you tell us what those issues are? Is it corrosion resistance or mechanical property related issues? Has anyone come across any data which compared corrosion resistance of trivalent conversion coatings over Zn or Zn-Ni coatings compared to hex chrome?
Thank you
- Baton Rouge, Louisiana, USA
2007
A. Hi Prat. A number of OEMs have approached me in the past year because they are having very significant problems now that their plating shops have switched to trivalent chromates. A very common problem is that their subsequent paint no longer adheres properly; in another case the prep cycle for selective e-coating is destroying the salt spray resistance of the non painted areas whereas it was previously fine with hex. The low surface resistivity of hexavalent chromates is no longer maintained with many trivalent chromates and their topcoats, causing resistance problems for some products. But these issues that we already know about are not the ones that bother me most; if widespread unanticipated problems have already showed up in the very short term, the assumption that trivalent coatings will have no as yet unknown problems occur over the decades is a foolish & risky guess.
As you no doubt know, trivalent chromates have existed for decades, but offered nowhere near the corrosion resistance of hex. Breakthroughs in the last ten years changed this to the point where trivalent chromates can (it is thought) match the corrosion resistance of hex; however there are still big differences. Whereas hex chromates are almost a commodity (although they are actually still proprietary, the brand-to-brand differences have become very very small over the decades), broadly different technologies are used by competing brands of trivalent chromates (thick film, thin film with topcoat, thin film without topcoat, etc). One approach may offer subsequent paint adhesion issues and another might not; one may resist an e-coat prep cycle properly and another not (and can it actually resist the real world if it can't resist this?); one may retain good conductivity and another not. And often the OEM has little knowledge and no control because jobshop X may be using brand X trivalent chromate, and shop Y may be using brand Y, and shop Z may be using brand Z. And shop X may switch to brand Z unannounced when an environmental or cost pressure hits them. So one day your parts have thick-film chromate and the next day they have thin-film chromate with a zirconium topcoat or vice-versa. They all have good corrosion resistance in salt spray testing, but they are very different coatings.
This posting is getting long, but here's my opinion: I think we simply don't know what will happen to trivalent coatings over 25+ years, and the fact that they pass a salt spray test offers no reassurance in this respect. So, although I'd certainly be comfortable building many kinds of widgets with trivalent conversion coatings, there are other things (like bridges) where I'm not at all comfortable with switching to trivalent coatings yet.
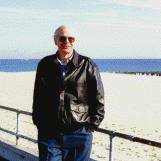
Ted Mooney, P.E.
Striving to live Aloha
finishing.com - Pine Beach, New Jersey
2007
Q.
I purchase hardware fasteners for our company. We have always used a Chrome 6 coating on parts that require black zinc coating and we require a minimum surface protection of 48 hours in salt fog. This forum is fairly new to me, so please excuse me if I misinterpret any information. We sell to big retailers that now require Chrome 3 trivalent. We have tested some new parts and they are failing at less than 24 hour in salt fog. We do call out ASTM standards for parts and must pass 48 hours but we have had two tests fail so far. I am thinking we are not calling this out correctly or it should be combined with a sealer or top coat of some kind. Can you tell me typically what works to get a Chrome 3 coating to go 48 hours in salt fog or more?
Thank you,
- Clearfield, Utah
February 3, 2013
A. Dear Heidi,
There are some C3 black chromates that could work in screws, specially if you are working with alkaline zinc to plate them. If you are using acid zinc plating, you have some other systems to blacken the surface and give some extra corrosion resistance.
There are some duplex processes, blackening and passivating the surface in the first phase, and sealing in the second. This processes achieve up to 144 hours of salt spray to white rust, but are somewhat "discolored" if you compare them with standard Cr6 chromates. Just look for vendors, there are some options in the market.
If you must use that Cr3 chromate, you can try some inorganic sealer or dry film anticorrosive oil. This could help.
Hope this information helps you, regards!
- Cañuelas, Buenos Aires, Argentina
March 5, 2013

Q, A, or Comment on THIS thread -or- Start a NEW Thread