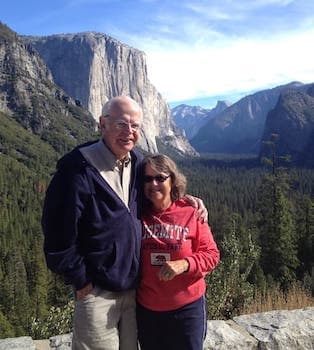
Curated with aloha by
Ted Mooney, P.E. RET
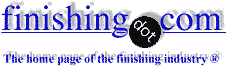
The authoritative public forum
for Metal Finishing 1989-2025
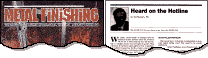
-----
Minimising surface rust on stainless steel through extraction of surface impurities in a marine application
Hi, My name is Jeff Clifton and I am located in Qld Australia
The subject I would like assistance with is: The Minimising of Rust on Stainless Steel:
What I am looking for assistance with is in regard to reducing the ability for surface rust to form on stainless steel hand rails on boats.
I am verbally led to understand that there is a process where introducing an electrical current through the stainless whilst submerged in a vat of some brand of acid (I have been told Phosphoric, but am unsure, or what mixture ratio) that this will extract some of the other metals from the surface of the stainless steel hand rails and in turn give us more longevity for stain free hand rails.
Any assistance that I can receive firstly regarding information around this process and secondly on what do I need to do this.
Regards and looking forward to your assistance.
Shipwright detailer - Yeppoon, Queensland, Australia
2007
First of two simultaneous responses -- 2007
Hi Jeff,
The process is electropolishing. Many formulations include phosphoric acid (relatively heavy, expensive and viscous cf. other common acids), mostly in combination with sulfuric acid; see letter #44029. ASTM B912, 'Passivation of Stainless Steels Using Electropolishing' gives a basic formula; search this site for others. Not really for Do-It-Yourselfers; but see letter 43547 if serious. Production work should be performed in commercial shops with large heated tanks, wastewater treatment, environmental permits, etc. Brush electropolishing can be done using a portable set-up for maintenance work and welding clean-up.
There are also relatively non-hazardous, proprietary electropolishing solutions available from several site vendors below (one such solution originated in Australia).
Browse the Australian Stainless Steel Development Association site
(http://www.assda.asn.au/). Relevant publications include 'Corrosion Resistance in Marine Environments,' Preventing Coastal Corrosion (Tea Staining),' and a group under the 'Surface Finishes' heading.
- Goleta, California

Rest in peace, Ken. Thank you for your hard work which the finishing world, and we at finishing.com, continue to benefit from.
Second of two simultaneous responses --
Jeff,
The treatment you are referring to is electropolishing.
As to my experience this is for the moment the best method to improve corrosion resistance of SS 304 and 316 in marine-and outdoor-applications.
You should contact a specialised electropolisher. This treatment is something you should not try by yourself; to many quality, environmental and safety issues are involved in this process (unless you are familiar with electrochemical treatments).
Kind regards.
- Brugge, Belgium
2007
Electropolishing leads to corrosion prevention by way of smoothing the surface at a microscopic level. Corrosion proceeds much more rapidly on a rough surface where there are microscopic "peaks" on the surface, electropolishing erodes those peaks down. The composition of the metal at the surface is unchanged.
By contrast, passivation leads to corrosion prevention via an acid treatment that removes the free iron from the surface and leaves behind the other elements that do not form rust, i.e. chromium, which then reacts with air to form a protective oxide layer.
The ultimate in corrosion protection is achieved by electropolishing followed by passivation, especially citric acid based passivation.
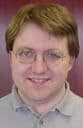
Ray Kremer
Stellar Solutions, Inc.

McHenry, Illinois
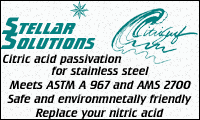
2007
Q, A, or Comment on THIS thread -or- Start a NEW Thread