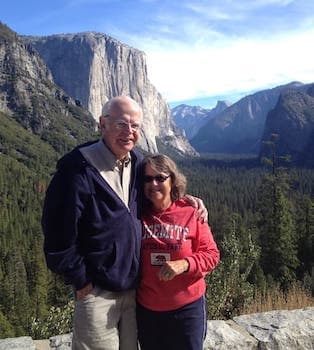
Curated with aloha by
Ted Mooney, P.E. RET
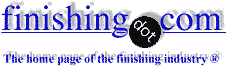
The authoritative public forum
for Metal Finishing 1989-2025
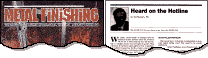
-----
Chrome plating: microcracking & macrocracking

Q. Hello, I have just entered the Hexavalent chrome plating industry and I saw some anomalies during my work. During micro-crack control, there are pit-like areas on the product that appear under the microscope and where the cracks meet at a point. I would like your help in understanding why this might be happening. Thank you in advance.
Guner Giskurlaboratory worker - Turkey
February 26, 2025
⇩ Related postings, oldest first ⇩
Q. Hi all,
We are an Engine Valve manufacturing company and do plating in the stem portion (cylindrical portion) for 3 to 7 microns thickness for a length of 50 to 100 mm.
In our plating component we find micro cracks in the Cr. deposit. As per our knowledge it is unavoidable and often desirable.
But we are not sure that whatever we find is micro-crack or macro-crack and the crack is only because of plating process.
So can you help by sending any sample picture of Cr. Plating crack type and the allowable density? And which is considered micro-crack and which considered macro-crack?
And can you tell me what are the parameters will cause the crack?
Some parameters of our bath:
We are using normal Chromic acid bath.
Composition: Chromium: 250-300 gram/litter
Sulphate : 2.5-3 gram/litter
Contamination: < 6 %
Substrate: EN-52 (Ferrous based alloy)
21-4N (Nickel based alloy)
Employee - Hyderabad
2007
A. Step 1. is to find out what your customer specs for the valve. I doubt if your customer is so small that they do not have specs.
I would absolutely look into porous pot technology for reducing your contaminant level. You get poor quality and slower plating at that level.
- Navarre, Florida
A. Chrome is very hard but its elongation is less than 1%. During plating it shrinks more than that. As a result it cracks. Trying to define what is a macro and what a micro crack is somewhat subjective and conventional. Try to reach an agreement with your customer. Typically, if the cracks do not propagate to the base metal and are well distributed across the surface they are OK. Plating temperature and chemistry influence the crack pattern.
Guillermo MarrufoMonterrey, NL, Mexico
A. Quantity of Micro cracks /unit on hard chrome plated deposits also vary by type of Hard Chrome Process. Could you elaborate on type of Process being used? (conventional sulphate. Mixed fluoride, High speed or other process). Also , what range of cracks /unit is customer spec? We have plated over 24 million IC valve stems /year and may be able to provide some insight.
Tim DeakinNorth Tonawanda, New York
QA Practices for Chrome Plating Hydraulic Cylinders
Q. Hi, I am an engineer working for a company which looks at corrosion issues. We are having some issues with corrosion of chrome plated hydraulic cylinders which appear to be the result of porosity in the chrome plating and would like to come up with some standards and testing procedures to apply to the cylinders and hopefully mitigate the corrosion issues.
Currently, the cylinders lack exact specifications and have no QA testing requirements. Would it be useful to look at using a nickel plating on the steel before chrome plating and changing the thickness of the chrome plating as possible steps to take to solve the porosity issues?
I am also interested in what type of QA practices manufacturers generally use, or should use, for chrome plating operations. I read that surface roughness and cleanliness, gas agitation, and mechanical finishing after plating seem to be major factors in the efficacy of the plating. It seems that those factors should all be closely monitored, but are there others that are crucial to the porosity of the final product?
Finally, we have been using the ferroxyl test to determine the porosity of the plating, but are interested in looking into other effective tests that can be used in the field and do not require highly specialized equipment or extended periods of time (e.g. SEM, spray cabinet, etc). If there are any other thoughts or suggestions on any of these topics, I would love to hear them. This site has been a great resource for me, so thanks for your help.
Corrosion Engineer - Reston, Virginia, USA
November 30, 2010
A. Nickel underplating would certainly help. Truck bumpers would normally use two different types of nickel for even greater protection. Plating thickness is certainly going to have an effect.
Ferroxyl ⇨ is an extremely sensitive test. copper sulphate
⇦ this on
eBay or
Amazon [affil links] is a less sensitive test that works for many applications , has a longer shelf life and is a bit safer to use.
- Navarre, Florida
Q. Thanks for the response, James.
Can you provide any insight into how plating thickness affects porosity? For example, if you were having porosity issues, would you start by increasing or decreasing the plating thickness? It would seem to me that a thicker coating would reduce porosity, but that cracking and other defects might become an issue.
- Reston, Virginia, USA
All chrome is cracked or micro cracked which is far better.This may be giving you the porosity indication.
Grinding is hard on chrome, and most grinding shops push for production rather than quality by using the wrong feeds and speeds, excessive depth of cut and the wrong resin/grit in the wheel. This cracks the chrome even more and when taken a bit further, causes delamination.
Normally, more chrome is better for pores, but if the pore is really a pit, then nothing will help. Pits have many sources from inadequate cleaning. grit imbedded in the part and trash floating around in the chrome tank.
- Navarre, Florida
TAM panel won't crack. Is chrome plating too hard?
Q. Hello,
We are doing some R&D to develop a TAM panel to test the quality of dye penetrant in NDT. The TAM panel description can be found here:
www.ndt-ed.org/EducationResources/CommunityCollege/PenetrantTest/QualityProcess/PerformanceCheck.htm
It consists of stainless steel (around 2 mm thick) panel on which there is about 70 microns hard chrome plating. The stainless steel is indented with hardness tester machines in order to create artificial cracks on the chrome side.
We used 304 stainless steel, MILL FINISH (NOT POLISHED), then conducted chrome plating. Hardness is supposed to be around 75 Vickers.
When we indent, the chrome does not crack. Instead there are a lot of "micro-cracks" that fill all the bulge created by the indentation. However, our objective is to create star-like deep cracks, deeper, wider and more visible than the micro-cracks.
What is the problem with our procedure? Is the chrome plating too hard / not hard enough?
Thank you very much for your help.
- Coventry, UK
April 2, 2014
Q, A, or Comment on THIS thread -or- Start a NEW Thread