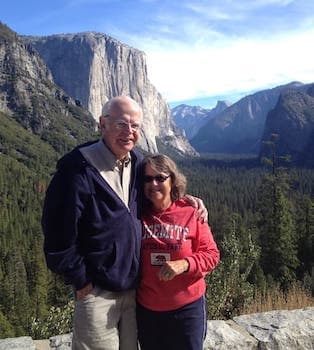
Curated with aloha by
Ted Mooney, P.E. RET
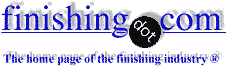
The authoritative public forum
for Metal Finishing 1989-2025
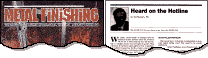
-----
Throwing Power of Nickel Sulphamate plating solution
2007
Q. Hello,
I am running nickel sulphamate plating at the following conditions:
Ni2+ - 100 g/l
NiCl2 - 10 g/l
Boric Acid - 32 g/l
Additive - 4 ml/l
I am trying to increase the thickness of one of my plated parts so that we won't hang around at the lower end of the spec given. However, increasing the concentration didn't help much and now, the current is set at a very high end just to pass the spec given.
Can anyone help? Is this due to the throwing power of the bath? FYI, I am plating stamped terminals.
Thanks.
Process Engineer - Penang, Malaysia
![]() |
A. Increasing current is the least frequent way to increase metal deposition because of the problems associated. Most platers will increase processing time instead. Guillermo MarrufoMonterrey, NL, Mexico 2007 A. If by throwing power, you are referring to macro throwing power or covering power, Why are you in such a rush? Time equals coverage. If you are talking about micro throwing power, getting into crevices, is a whole different game. Typically, this will involve lower ASF (ASD), a higher temperature and much stronger agitation, preferably air, which will require using a low foaming wetting agent like SNAP-AM rather than SNAP. - Navarre, Florida 2007 |
Q. Hi James,
I am in a "rush" because time, besides being equal to coverage like how you put it, also equals output. The machine is set at a certain speed because certain volume of output is expected from the plating line. This is why I cannot increase my processing time as said so by the other gentleman.
I am referring to macro throwing power because I just want to increase the overall nickel thickness so that my parts won't hang around at the lower end of the spec given. We are not failing the spec but it is just that we are always dangling at the lower end. Moreover, my plated part is in a simple hook-like shape so there is not much nook and cranny to get into.
FYI, temperature is set at 55 °C and according to the supplier, 60 is the limit for nickel sulphamate plating solution. So, is there any other way to achieve my objective? Thanks...
- Penang, Malaysia
2007
Hello, Jen. Of course you want to plate at the highest possible production rate. A point that Guillermo and James are implying, I think, is that everybody always wants to do that, so the plating lines & plating processes were already optimized to make that a primary goal.
So when you ask "What simple adjustments do I make to plate faster?" the answer is: "Sorry, that adjustment for maximum plating speed was already made fifty years ago".
Your best hope for faster plating is extreme agitation. But if the terminals are still in a strip, 'jet plating' might do what you wish. Good luck.
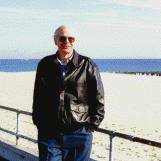
Ted Mooney, P.E.
Striving to live Aloha
finishing.com - Pine Beach, New Jersey
2007
![]() |
A. While violent agitation may not be possible, If I had your problem, I would definitely increase the agitation to the max that the racking and tankage would allow. It is the only option as it allows you to increase current density (amperage) without getting burning. How much you can increase the amperage will depend on how much you can increase the agitation. - Navarre, Florida 2007 A. Hi Jen, Process Engineer - Syracuse, New York 2007 A. Jen Teh. Monterrey, NL, Mexico 2007 |
A. Jen,
What is the current density that you are applying on your part? As I know, for Nickel sulfamate bath, an increase in the additive ( stress reducer ) may allow you to increase your current density, hence , your plating thickness. Check the TDS of your additive.
metals - Penang, Malaysia
2007
Q. Thanks for all the replies.
My CD is at around 8-10 A/dm2.
The nickel sulphamate I am having is already a high-speed one. Does anyone know what is the maximum concentration of a typical nickel sulphamate bath?
By the way, what is the common pH adjustment method for Nickel Sulphamate bath? I am currently adding sulfamic acid
⇦ this on
eBay
or
Amazon [affil links] once to twice a week to keep the pH between 3.5-4.5.
Kindly advise. Thanks.
- Penang, Malaysia
2007
Ed. note: We see that you have thanked the responders not only in words, but by offering your own helpful advice on other threads here, Jen. Welcome to the forum!
A. Sulfuric acid will damage your bath. Use sulfamic acid. Since you want performance, keep your pH as close to 4 as possible. 3.9 to 4.1 is more appropriate. For more speed, I would use 4.0 to no higher than 4.2
Jim
- Navarre, Florida
2007
A. Jen
Recently we observed that replacing half of the nickel with an equal molar amount of NaCl, KCl, or MgCl2 will greatly increase the throwing power and not slow down the plating rate. This could be an attractive solution to getting the nickel thickness centered in the range.
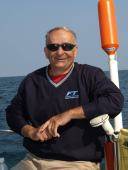
Pat Mentone
St Paul, Minnesota
2007
A. I wish I had your problem. To be honest, if your machine is running at a set rate of speed, and your are achieving your sprec, and your numbers are near the low end of the spec, it sounds like you are doing your job great. With the cost of Nickel at this time, I would think that sticking to the low end of the spec as much as possible would be just fine, if not desirable. Good Luck, and keep doin what your doin!
Michael Berrierplating shop - Addison, Illinois, USA
2007
Q. Hi,
I'm Muhaimin. Would love to know how can I maintain efficiency rate of nickel plating (maintain the speed, current and etc.) but at the same time reduce the usage of Nickel Sulphamate, Boric Acid, Nickel Chloride. I'm using too much of the solution and it costs me a lot. My control range of concentration of solution is as below.
Nickel Sulphamate : 370-410 g/l
Boric Acid : 30-45 g/l
Nickel Chloride : 20-30g/l
Thanks a lot and I really appreciate help from others
Plating - Ampang, Selangor, Malaysia
April 16, 2010
Q. We are Nickel plating small spiral parts and getting problem with leaks in the parts. Looks to me is missing plating area cause leaks. Any one has any idea how to improve plating to get coverage inside out.
Jawed [surname deleted for privacy by Editor]- Edison, New Jersey,USA
December 1, 2010
Is 100 ASF Realistic for Nickel Sulfamate Plating?
Q. Hello,
We plate small rings with nickel from a nickel sulphamate solution. We recently set up a new tank and have been trying to plate at a much faster rate (100 ASF) than in the old set up we had (40 ASF).
The only problem I have found is that the thickness distribution is considerably harder to control. Our chemical supplier is adamant that I will not be able to get good results plating at this speed, and that plating at 100 ASF is only possible in reel to reel plating. However, I have read in several articles (including one on this website) that speeds considerably faster than 100 ASF can be obtained with violent agitation. The eductor system that was originally provided does not provide violent agitation, so I blocked off some of the venturi nozzles to increase it slightly, which has proved to increase the agitation and improve the thickness distribution slightly.
I have now purchased a larger pump for the eductor system
⇦ this on
eBay
or
Amazon [affil links] to increase the agitation more in an attempt to reduce the thickness distribution to the desired level, but am yet to install it in the tank.
My question is, should I feasibly be able to plate at this speed or am I on a wild goose chase?
Thank you
Process Improvement Engineer - Co. Durham, UK
February 10, 2016
A. Amperages considerably higher than 100 ASF are not all that unusual, in some cases up to 400 ASF. I have seen reports of electroforming record stampers at 600 ASF.
Increased agitation is the key, but you'll also want to make certain the bath chemistry is spot on, and run at the higher end on temperature, perhaps 140 °F.
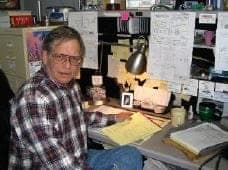
Jeffrey Holmes, CEF
Spartanburg, South Carolina
February 10, 2016
A. Hello Tom, I agree with Mr Holmes that 100 ASF can be achieved. There are a few cautions though. Your thickness distribution will suffer if the bath you are using is not formulated for current density of 100 ASF or more. For example; your Ni metal and sulfamic acid should be at a level to handle those CDs. Vigorous solution agitation alone will help, but your plating thickness will vary across the part. Your supplier is correct in what they say. Your tech data sheet for the Ni bath gives you a current density range (ASF). There is a good reason for this range given. Good things come with time... Good Luck.
Mark BakerProcess Engineering - Phoenix, Arizona USA
February 10, 2016
February 15, 2016
Q. Thank you for your responses.
Just to be clear, I have drifted somewhat from my chemical suppliers recommended concentrations to allow for the higher CD. When you say "For example; your Ni metal and sulfamic acid should be at a level to handle those CDs", is that to counteract any burning that may occur, or to aid in the thickness distribution?
My bath concentrations are as follows:
Nickel Sulphamate (64% conc.): 570 ml/L
Ni: ~100 g/L
Nickel Chloride: 10 g/L
Boric Acid: 40 g/L
pH: 3.8-4.2 (Controlled by additions on sulfamic acid
⇦ this on
eBay
or
Amazon [affil links] )
Is this different to what you would recommend for plating at 100 ASF?
Process Improvement Engineer - Co. Durham
A. Hello again Tom, now that I see your bath make-up I think you can maintain 100 ASF as long as your solution agitation is adequate. I was working with a bath from a MA supplier a few years back that had less of a Ni metal content, and was able to reach 120 ASF. I have also worked with Ni Sulphamate baths for printed circuit boards that we had to keep at 25 ASF. The important thing is being able to replenish fresh Ni ions at the cathode. An adequate Ni metal concentration along with good solution agitation aids in fresh ion transfer. Without it, you will experience poor thickness uniformity and possible discoloration or burning of the deposit. If you have a thickness measurement device, take thickness measurements on different areas of the part. This will tell you where you stand with the higher CDs. Good Luck to you.
Mark BakerProcess Engineering - Phoenix, Arizona USA
February 16, 2016
A. Hi Tom,
That is a typical Ni sulfamate make up. The operating range for a standard sulfamate such as yours is 20-140 ASF (2-15 ADM). Remember, with increasing current density you in turn will have increasing internal stress in the deposit. Nearly all bath parameters will effect the amount of stress occurring during the dwell/growth period. Increasing temperature decreases Stress and increases hardness up to around 130 °F. I wouldn't recommend pushing the temp. much higher then 140 as many sulfamate hardeners and surface tension additives began to cook at or above 140 and create hard to remove contaminants. Contact your chemical supplier to be sure your bath can handle higher the recommended temperatures.
The literature here:
www.finishing.com/library/stein/stresspaper.html
... can be beneficial to you if you do run into problems with internal stress.
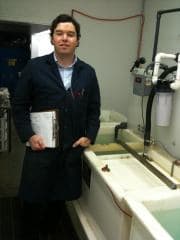
Chance Dunstan
Electroplating/Forming/Coating Manager
Placerville, California USA
April 15, 2016
adv.
"The Sulfamate Nickel How-To Guide"
by David Crotty, PhD
& Robert Probert
published Oct. 2018
$89 plus shipping
Q, A, or Comment on THIS thread -or- Start a NEW Thread