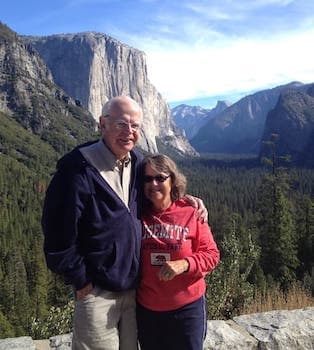
Curated with aloha by
Ted Mooney, P.E. RET
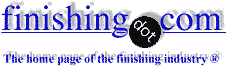
The authoritative public forum
for Metal Finishing 1989-2025
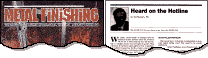
-----
Zinc Plating Tank Construction
Q. I am new to the industry and want to have tanks made for Zinc plating that will be 8' X 3' X 5'. I have a couple of questions:
1. What thickness and type of steel should the tanks be?
2. What size, how many and what location should the drains be?
3. Also am I missing anything else? Any info would be greatly appreciated.
Plating Shop - Dallas, Texas
2007
A. Hello Ben. Steel plating tanks of this size are generally made from 1/4" thick hot rolled steel plates, electric welded inside and outside. They will need an angle iron rim and some amount of girthing (horizontal belly bands) but I cannot do the structural calculation for you in this venue. A great book old about it is Design of Welded Structures ⇦[this on Amazon affil links] by Lincoln Arc Welding Foundation.
Tanks like this usually only have one 2" drain, with any additional piping such as for filters going over the wall. The
Electroplating Engineering Handbook ⇦ this on
eBay,
AbeBooks, or
Amazon [affil links]
has some good tank design ideas like sloped bottoms, but in truth they are usually not implemented for cost reasons. There are lots of experienced tank fabricators who specialize in the plating industry.
But something that I think you might be missing is the possibility of building the tank from fiberglass or polypropylene. Good luck.
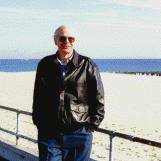
Ted Mooney, P.E.
Striving to live Aloha
finishing.com - Pine Beach, New Jersey
2007
A. Please be aware that some zinc electrolytes require a lined tank. These linings are either from adhesive applied PVC sheets i.e. Koroseal, flexible PVC liners, or welded sheet polypropylene. All the plastic materials need to be of a type compatible with the chosen electrolyte or you will have contamination of the plating solution as a result of leaching the lining. Although some people use unlined steel tanks for alkaline zinc plating it is frowned upon for reasons of electrical isolation and redundancy of integrity. If you have identified a supplier of zinc technology this supplier should be able to provide you with specifications of the types of tank construction recommended.
Gene Packmanprocess supplier - Great Neck, New York
2007
A. Hi Ben,
Not knowing, which you didn't give, the temperature nor the chemistry, I'd go along with what Gene said.
Making the tank from a dual laminate would, in this case, be quite expensive as they sure don't have the strength of a steel vessel. Mind you, I am a great proponent of using the right plastics. PVC:FRP with a largish top flange AND a secondary HEAVY box flange 1/3 up from the bottom.
I'd opt more for the PVC flexible liner because it would be easier to fit, less expensive than PP .... and PP, like Pe, has a VERY high coefficient of thermal expansion and in a large tank like yours, this could lead to failure.
The cheapest bet would be fibreglass BUT if it were scratched at all during loading/unloading, ah, you're going to have a failure as it is not homogenous like the thermoplastics.
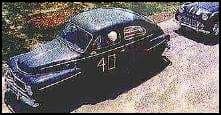
Freeman Newton [deceased]
(It is our sad duty to advise that Freeman passed away
April 21, 2012. R.I.P. old friend).
2007
Q. Hi,
May I know the suitable tank for plating process, especially zinc nickel electroplating process. Can we use stainless steel tank? If we can, why? If not, also why?
- johor bahru , johor. malaysia
October 1, 2014
A. Hi Noya. Stainless steel tanks are usually not satisfactory for the plating step per se, because of attack by acidic plating solutions. They may be satisfactory (but not necessarily cost-effective) for some of the other tanks in the line such as rinse tanks, alkaline cleaners, and post-treat dips. Polypropylene, fiberglass, and PVC-lined plain steel tanks are probably the most popular these days, in about that order. Good luck.
Regards,
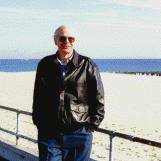
Ted Mooney, P.E.
Striving to live Aloha
finishing.com - Pine Beach, New Jersey
October 2014
Q, A, or Comment on THIS thread -or- Start a NEW Thread