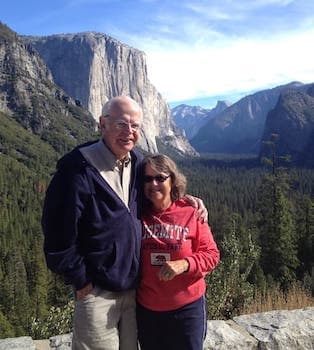
Curated with aloha by
Ted Mooney, P.E. RET
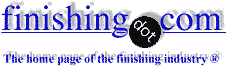
The authoritative public forum
for Metal Finishing 1989-2025
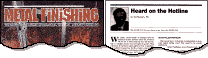
-----
Strip plating thickness problem
Q. We have continuous or reel to reel copper-tin, zinc, nickel electroplating plant. Recently we are giving 4 microns of copper as undercoat and 3 microns of tin to one of our customers but we have enquiries about 6 microns of bright tin. We are using acid tin process. If we reduce the time to increase tin thickness copper also increases. We are using acid copper process.
DHANANJAY SHINDEplating shop - Maharashtra
2007
A. In your case, by adjusting current density and feed speed it is hard to achieve thickness requirement of the copper and tin at the same time. Practical way is lower your feeding speed and shorten copper plating distance by cutting the quantity of copper plating cell (let's say in your process, you have 4 plating cells for copper, but this time you only put current in the last 2 cells.).
John Hu- Singapore
2007
2007
A. Hi Dhanajay. How are you!
Achieving desired result in Continuous reel-to-reel plating is all about:
1. feed speed adjustments
2. plating speed or plating efficiency of the bath
3. no. of plating cells and their length
4. current carrying capacity of the bath (the more the better)
Here in your case as John Hu rightly said
1. reduce (current off) no. of cells of acid copper
2. increase no. of tin plating cells.
3. adjust current.
4. calculate and adjust the feed speed though in this case it may not be advantageous.
5. look for high current carrying (high speed) plating process. There are supply houses who offer high speed tin plating process.
Regards
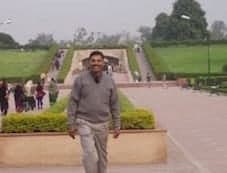
T.K. Mohan
plating process supplier - Mumbai, India
Q. Having issues with plating 96Sn/4Ag in a controlled depth process. Material is phosphorous bronze CDA 510 clad to CDA 770 NiAg. Size .012" x 1.370". Trying to plate one edge top and bottom, .870" wide x .0001" min with the SnAg alloy. SnAg alloy starts to burn with plating above .00005" thick. Any suggestions?
Richard Bodami- Bat Shore, New York, US
November 28, 2012
Q, A, or Comment on THIS thread -or- Start a NEW Thread