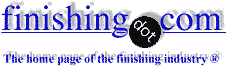
-----
Iron Contamination of sulfuric acid anodizing solution
Q. We are a distributor of galvanic processes and one of our customers has a problem with the anodizing. The parts to anodize are aluminium made but have a little area made from iron. This iron area of the part can't be separated (they are manufactured that way).
Now, the problem is that the sulfuric acid anodizing solution is trapping iron from that area and now is full of it. This iron inhibits the action of the anodizing solution so the effect on the part is not uniform, homogenous.
So the question is, anyone know how to remove this iron from the anodizing solution?
Thanks in advance.
Distributor - Arrankudiaga, Bizkaia, Spain
2007
2007
A. First, it is necessary to mask over the iron prior to anodizing.
You probably can remove much of the iron from the solution by electroplating onto an auxiliary cathode. For this 'dummy plating,' use the anodizing cathodes as anodes, and hang the auxiliary cathode from the anodize workbar. Start with 6 Volts and adjust if needed.
- Goleta, California

Rest in peace, Ken. Thank you for your hard work which the finishing world, and we at finishing.com, continue to benefit from.
Thank you so much. I'll tell my customer to do so.
Thanks again.
- Arrankudiaga, Bizkaia - Spain
2007
2007
Q. We are a distributor of aluminium anodizing processes. One of our customers has a problem with the anodizing. The problem is that the sulfuric acid anodizing solution reaches 250 ppm of iron. This iron inhibits the action of the anodizing solution so the effect on the part is not uniform.
Mr. Ken Vlach advises that we can remove much of the iron from the solution by dummy plating onto an auxiliary cathode by using the anodizing cathodes as anodes. In the process we have lead made cathodes.
My question is:
Can we make dummy plating with lead anodes and aluminium cathodes.
What is a range of the Voltage we need
What is surface ratio we need for dummy plating?
Thanks in advance.
Q.A. manager - Akko, Israel
A. Hi Teddy.
I think steel would be better. Usually corrugated steel sheet, such as is used for roofing, is the handiest material since it affords a range of current density. Ken's estimate of 6 volts is good; I doubt that under 3 or over 9 would be required. Surface area and anode-cathode ratio sounds unimportant since you are not using soluble anodes, but a single sheet almost the size of the tank sounds right. Good luck.
Regards,
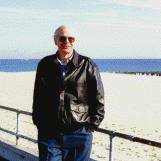
Ted Mooney, P.E.
Striving to live Aloha
finishing.com - Pine Beach, New Jersey
February 9, 2013
Q. The time it takes us to get a good 2 mil hardcoat has been rising lately - from about 45 minutes a month ago to about 2 hours now. When I explained our longer times to a local consultant, he indicated that it could be iron contamination in the bath. That jogged my memory to what I found in the tank about a month ago: During an anodize run, I noticed that a steel clamp spring broke and the clamp fell into the anodize tank. After the run, I dragged the tank with a magnet and found the remains of about a half dozen steel clamps in various states of disintegration.
The consultant subsequently analyzed the iron at 800 to 1000 ppm. He said that he was only aware of a Boeing spec that put a limit on it, but couldn't recall what the limit was. Does anyone know whether there is an iron contamination limit in a hardcoat tank, and if so what it is? Even better, can someone corroborate the "high iron, longer anodize times" theory?
Thanks in advance!
- Gardena, California, USA
February 6, 2013
A. Mike
Dr. Brace recommended a 50 ppm maximum in the Technology of Anodizing Aluminum. Dissolved aluminum effects the process so it is possible that iron does too. Check your amp-hours to see if it matches the thickness for your load size; 1440 amp-minutes for a 2-mil thick coating on 1 sq. ft.
Also consider using SST clamps.
- Colorado Springs, Colorado
First of two simultaneous responses -- February 13, 2013
A. First things first...get those steel clamps off of your line! I use all stainless clamps and/or plastic clamps with SS springs. While they are definitely more expensive (approx. $25 each) it's well worth the investment, as they will last a very long time, and if one inadvertently falls into the tank, you won't have contamination issues.
Secondly, I'm pretty sure the recommended limit for Fe is 50 ppm. Regardless, I'm sure 800 ppm is way too much. I honestly can't say whether it has an impact on anodizing times, but that much Fe in your tank can be doing you no good whatsoever.
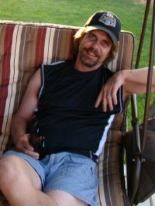
Marc Green
anodizer - Boise, Idaho
A. Both two above are correct. The "work" on iron contamination has not been done up to 800 ppm, but the reason for the 50 ppm limit is that iron lowers the corrosion protection of the anodic film. Moderate low iron does not affect rate of thickness build - again has not been tested to 800, but the guy above who says the aluminum could be the main problem is correct. Reviewing: Rate of thickness build increases with lower acid, lower temp, lower aluminum, AND higher current density AND getting the "current onto the part" around all the resistance in the racking, load bar, and hanging system..
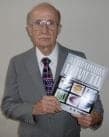
Robert H Probert
Robert H Probert Technical Services

Garner, North Carolina
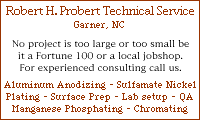
February 15, 2013
Q. Will the iron removal via plate out (after reversing the leads on the tank) technique out work regardless of the anode/cathode materials? My tank is lead lined and that, of course, acts as the cathode.
Mike Palatas [returning]- Gardena, California
February 19, 2013
-- 2nd Request
! Still very interested in input.
Do I need to reverse the leads coming from/going back to the rectifier, and then hook the bare steel sheet up to the normal part load bus work, or is it sufficient to just connect the steel sheet to the lead liner in the tank and then put in some electrodes (can I use aluminum or should I use some other material?) from my copper bus work into the solution, not touching the steel sheet of course?
Any info appreciated! I don't want to dump the entire 1200 gallon tank worth of solution.
- Gardena, California
April 13, 2015
A. I see that there are instructions for plating out iron in this thread. Has anyone actually done it? I am surprised that it is possible to plate iron from a bath with such a low pH and low iron content. We already have a plating cell in the anodizing setup. Is there any evidence of iron plating out on the existing cathodes? If not, I can't see the point reversing the polarity unless the are some specific cathode conditions which are not achieved in the anodizing cell.
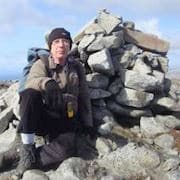
Harry Parkes
- Birmingham, UK
April 15, 2015
Q, A, or Comment on THIS thread -or- Start a NEW Thread