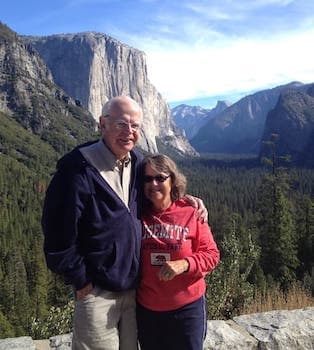
Curated with aloha by
Ted Mooney, P.E. RET
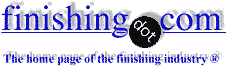
The authoritative public forum
for Metal Finishing 1989-2025
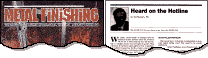
-----
Local serious pitting on heating coils - any thoughts?
2007
Serious corrosive attack seen on the heating coil of a chemical cleaning tank by pitting and through wall perforation.
Tank holds hot caustic solution for de-rusting and de-greasing of ferrous components, heated by steam from coil, solution at 85 centigrade approx, with aeration from tank bottom for circulation. Tank, coil and securing brackets material is 316 stainless, and only 10 months old.
Coil is fastened to side wall of tank, so is vertical.
Attack on pipes is perfectly round pits concentrated along a 20mm band on underside of the pipe, but only on the straight lengths, not the bends, and worse at the top length(hottest?) diminishing towards the bottom (coldest) part of the tank.
Scale is present in most pits, but some are bright and clean. Some scale is present near the pitted areas but none on the rest of the circumference.
Side wall fastening brackets are unaffected but area directly under brackets is partly scaled and partly severely affected by gross pitting. Affected areas here are smooth and bright like a galvanic or eroded finish.
HELP!
My thought for the bracket area deterioration is that there might be local boiling under the brackets, with cavitation/erosion by the collapse of bubbles.
My thoughts for the coil attack are held up by the difficulty of accepting how the attack could become so localised along a 20mm band on the pipe underside.
But I don't think the solution should boil, or the aeration bubbles should 'stick' to the pipe undersides.
All thoughts welcome.
Regards,
Metallurgist (believe it or not) - Plymouth, UK
Ed. note: Sorry for the delay, pictures added 5/15/07
Ed. note: Sorry for the delay, pictures added 5/15/07
First of three simultaneous responses --
Wow, this is a good one. (1) Is there any reason to suspect Sodium Chloride or other chloride in the Caustic Soda Solution? Tap Water?
(2) Even though everything is 316 stainless, some is rolled sheet, some is pipe, some is bent pipe. All you have to do is bend a piece of stainless, plunge it down in an electrolyte, especially in the presence of chloride, and you get galvanic corrosion.
(3) Is any stray a.c. or d.c. coming in on the steam pipe?
Get out your Simpson meter set it on lowest voltage reading, and start looking for some stray induced current or some galvanic current- one volt and 50 ppm chloride and you will corrode.
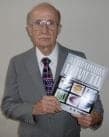
Robert H Probert
Robert H Probert Technical Services

Garner, North Carolina
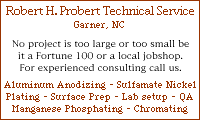
2007
Second of three simultaneous responses -- 2007
Probably, etching of the SS by ferric chloride
⇦ this on
eBay or
Amazon [affil links] where surface overheating occurs within trapped bubbles (either steam or air). Boiling is possible: Low pressure steam @ 248°F (120 °C) is capable of boiling solutions up to 34 wt% NaOH. Also, cheaper NaOH may contain considerable NaCl: 50 wt% diaphragm grade caustic soda ⇦liquid caustic soda in bulk on
Amazon [affil link]
solution contains up to 1 wt% NaCl.
"Where iron contamination or corrosion is unacceptable, epoxy lined steel, 316L and 304L stainless steels are recommended. 316L and 304L stainless is acceptable to 200°F. At temperatures above 200°F, nickel is typically used but Monel®, Inconel®, or Hastelloy® can also be used.
...
Where heating is required, an external heat exchanger with a circulating pump or internal steam heating coils are most commonly employed. The preferred materials for the coils are nickel, Monel®, or Inconel®. Despite this, stainless steel is most commonly used because of cost considerations. (At high temperatures, stainless steel may crack)."
Information mostly from the OxyChem Caustic Soda Handbook:
http://www.oxy.com/oxychem/Products/caustic_soda/literature/caustic%5B1%5D.pdf
Possible solutions:
Add surfactant to minimize the size and adhesion of trapped bubbles.
Switch to purer, rayon/membrane grade NaOH.
Use a more resistant (higher nickel) alloy heat exchanger.
- Goleta, California

Rest in peace, Ken. Thank you for your hard work which the finishing world, and we at finishing.com, continue to benefit from.
Third of three simultaneous responses -- 2007
My guess is electrolytic attack. Try a multimeter between the coil and the tank.
The bottom of the heater "box" appears to have overheated; has the tank boiled dry? Do you have a level controller and cutout?
The dead length of the heater seems to be very short. The heated part should be well below the surface; best near the bottom otherwise the solution is only heated at the top.
What is the red coating inside the tank? Or is it standing on the floor?
You should only need a MS tank and heater for a caustic degreaser. Did you get this from a process tank supplier or the local tin basher?
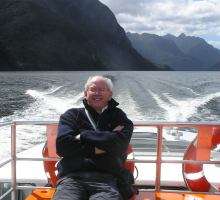
Geoff Smith
Hampshire, England
First of all, thanks for the responses, keep 'em coming.
I'll try to find out if Chloride levels are implicated -might be difficult now since tank is drained. As will stray current effect. Tank has definitely not boiled dry since there are good controls and cut-outs but coil is approx. 3ft 6in in height; tank is approx. 6 ft deep, so coil is highish,(too high?) Pic 1 shows coil is dismantled and lying on shop floor. Any more thoughts on the location of the pitting at the narrow band - Pic 2? and the scale?
Ship Repair - Plymouth, UK
2007
First of two simultaneous responses -- 2007
Sir:
The heater coil and tank should both be made of mild steel. The caustic soda ⇦liquid caustic soda in bulk on
Amazon [affil link]
(sodium hydroxide) almost certainly contains chloride and perhaps fluoride which both attack stainless. Bubbling air in the caustic converts hydroxide to carbonate (due to the carbon dioxide in the air). Thus over time all the hydroxide is converted to carbonate rendering the solution useless.
Regards,
Galvanizing Consultant - Hot Springs, South Dakota, USA
Second of two simultaneous responses -- 2007
I agree with all of the above posters that that looks like galvanic corrosion. Would it be possible to apply galvanic protection to these coils?
Either a sacrificial anode could be attached to them (made of magnesium, perhaps; any metal but aluminum or zinc that is higher in the electromotive series than iron) or the coils made cathodic by an impressed negative potential of a few hundred mV.
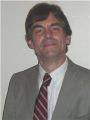
Dave Wichern
Consultant - The Bronx, New York
Q, A, or Comment on THIS thread -or- Start a NEW Thread