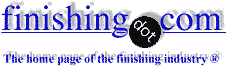
-----
Decorative chrome vs. Cr6->Cr3 transition
2007
Mr. Mooney;
I saw your response to another reader in regards to chromium vs. chromate. My question is somewhat related and is as follows...
The European Union has issued a directive adhered to by automakers, which eliminated the use of Cr6 in zinc/chromate surface treatments. This did not, however, affect the products which utilize a nickel/chrome surface treatment (i.e. decorative chrome). Why were the decorative chrome parts not affected by this?
Thank you.
QC Coordinator/QE, automotive fasteners - Berne, Indiana, USA
Hello, John. Admittedly this issue is very confusing for people who are not personally involved in metal finishing because two very different metal finishing processes use chromium chemicals, and either trivalent chromium or hexavalent may be used in either, and which one was used is important to the end user in one case but not in the other :-)
Let's talk chromium electroplating first. One step in the process is to immerse the part into the chromium plating tank, apply electricity, and electrochemically deposit the bright metal that we see on truck bumpers. Once the part leaves the tank and is throughly rinsed, the only chromium it has on it is metallic chrome. Metallic chrome doesn't have valence, and it makes no difference to the end user whether the manufacturer created that metal deposit by dipping the part into a tank that had trivalent chromium chemicals in it or hexavalent chemicals.
While there are advantages to trivalent chromium electroplating baths (like lower fuming, and reduced operator exposure and water treatment costs) and advantages to hexavalent chromium baths (like lower cost, thicker deposits possible, more consistent color), they don't affect the safety of the product or the end user.
In the case of chromate conversion coatings on zinc, however, the deposit is not chromium metal-- it is a rather complex mixture of "salts" of chromium. At the risk of slight simplification, if the tank it was dipped in had hexavalent chromium salts in it, the deposit on the part is a hexavalent chromium salt, whereas if the tank it was dipped in contained only trivalent chromium salts then it has only trivalent salts on it. And these hexavalent chromate salts that remain on the part are considered hazardous.
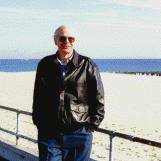
Ted Mooney, P.E.
Striving to live Aloha
finishing.com - Pine Beach, New Jersey
2007
Q, A, or Comment on THIS thread -or- Start a NEW Thread