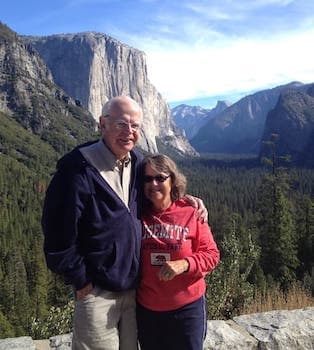
Curated with aloha by
Ted Mooney, P.E. RET
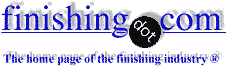
The authoritative public forum
for Metal Finishing 1989-2025
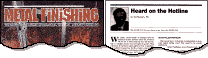
-----
Using 316 vs 316L stainless steel as cryoprobe
I am planning on making a cryoprobe tip out of stainless steel which will be cooled directly with liquid nitrogen. I used 304 stainless steel last time and it started to rust by the third use. I would like to switch to another stainless steel that is more corrosion resistant but yet has good machinability and I thought 316 stainless steel would be good but I don't know if there was a difference in using 316 or 316L stainless steel as far as corrosion resistance. Which is better? Or is there even another type of stainless steel that has even better properties (good machinability and corrosion resistant)? Thank you for your advice in advance.
Dezba CoughlinResearch Scientist - New York, New York
2007
First of three simultaneous responses -- 2007
I see no reason for the 304 to rust. It should be passivated and kept clean before use.
Please describe any corrosive conditions during use or storage.
- Goleta, California

Rest in peace, Ken. Thank you for your hard work which the finishing world, and we at finishing.com, continue to benefit from.
Second of three simultaneous responses --
Try 318 S/steel It is a better grade and machines well.
Ken Foyn- Durban, South Africa
2007
Third of three simultaneous responses --
There is not much difference in corrosion resistance between 316 and 316L SS unless there is welding or some other thermal treatment involved. 316L will be better where manufacturing processes involved elevated temperature conditions in the range of about 800 - 1600F.
316 has better pitting resistance than 304 in chlorides, but may not be much better in very corrosive environments. If 304 "rusted" after a very short time, I would suspect that 316 may not behave much differently.
You may want to find out why the 304 corroded. The environment may not be suitable for 300 series stainless or their may be something in the manufacturing of the probes that inhibits corrosion resistance. Both of these alloys are sensitive to surface contamination during surface finishing. That is why chemical passivation is often specified for parts made from these alloys.
There are plenty of other alloys with better corrosion resistance. Of course, the cost will be higher. Selection of an alternative alloy would be best done after the cause of the corrosion of the 304 is known.
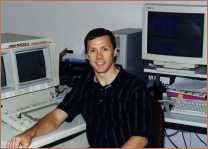
Larry Hanke
Minneapolis, Minnesota
2007
See letter number 14356
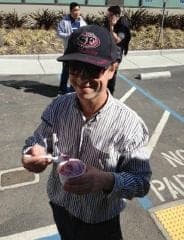
Blake Kneedler
Feather Hollow Eng. - Stockton, California
2007
Q, A, or Comment on THIS thread -or- Start a NEW Thread