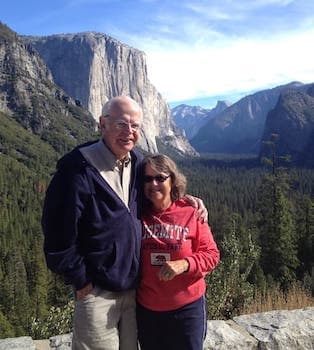
Curated with aloha by
Ted Mooney, P.E. RET
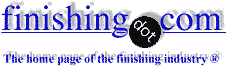
The authoritative public forum
for Metal Finishing 1989-2025
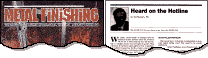
-----
New Plating Facility Treatment Plant
2000
we are expanding our plating facility by 100,000 sq ft. and are looking for a supplier to supply a new up to date waste treatment facility. we have thought to use a conventional system , micro-filitration, and a combination of each. with in mind the new MP&M limits to be placed in effect this october by the EPA
which would best suit a new plating facility?
thank in advance!
chad mazeika- rockford,il,usa
2000
The type of system best suited for a new plant depends upon the type of waste you will be generating.
You need to contact a reputable consultant or supplier who can access multiple technologies. No single technology is best for everything.
My personal opinion is this:
1. Install dragout tanks after EVERY process. Put as much as possible back into the process tank. This won't work with all processes, but is great with heated tanks that lose a lot of water through evaporation. Buy Ted's rinsing program to help with rinse disposal analysis.
2. Use multi-stage counterflow rinsing wherever possible.
3. Recycle some of your rinses through ion exchange. Which ones are best to recycle can be answered by a paid professional after a study, not on the web. You need to grab and analyze samples to make these decisions.
4. Treat the rest of the rinses, any remaining dragout solution, any wastewater ion exchange regenerants, and the concentrated bath dumps and by chemical precipitation. Only an expert can answer what is the best chemical treatment method, again, based on sampling and analysis. Keep this stuff segregated until the best treatment methods are known.
5. Use a microfilter for all wastes after precipitation is complete. You don't need a flocculant and you don't need polishing filtration. A microfilter supplies 100% positive filtration IF YOU GOT THE CHEMICAL PRECIPITATION DONE RIGHT.
6. It may be possible to use RO (reverse osmosis) on microfilter effluent to recycle even more water. This again depends upon testing.
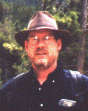
Bill Vins
microwave & cable assemblies - Mesa (what a place-a), Arizona
The previous response by Bill Vins is pretty much on the money. Integrating good rinsing and water conservation techniques up-front at the plating line is a good first step. Proper segregation of the waste streams is another key component. Ion Exchange is good for low TDS rinses, but again, the right segregation of the rinses is critical. Microfiltration is the best choice for meeting stringent limits, and allows you the option of putting an RO system in after the microfiltration system to recycle treated wastewater. This cannot be accomplished with conventional clarifiers. Give me a call if you would like to discuss this in detail.
Stephen Bell- Lowell, Massachusetts
2000
Hi Chad,
I entirely agree with Mr Stephen Bell in that the rinse outlet streams must be segregated-The cyanide dragouts must be transferred to a treatment tank every shift or every day dedpending upon the rate of build up- preferably not more than 5 gms/lit.
The activator/acid dips must be preferaly sulfuric so that the subsaequent rinses after segregation can be batch treated with lime to precipitate the sulphate as calcium sulphate,and after softening may be reused for the same purpose (of rinse after acid dip).
The additional fresh soft water required per day would be for regeneration of the softener daily and this may be mixed with the recycled water so that the TDS of the recycled water remains almost constant and a portion of this water may be used to mix the regenerant chemicals. Likewise rthe DM rinses may be segregated and mixed with the daily quanity of RO water required for mixing the regenerants for the DM plant for every batch regeneration, passed through granular activated carbon to strip the organics/brightener residues and passed through the DM plant.
Use of sulfuric acid in place of hydrochloric acid for the cation resin regeneration facilitates the precipitation of the sulphate by lime for treatment of the regenerant waste,so avoiding the chloride which is impossible to precipitate.
Finally the nonusable High TDS waste comprising of the neutralised regenerant waste and the high TDS RO reject may be evaporated by atmospheric evaporation to achieve zero discharge! Parameswaran Iyer
Paramesaran Iyer- Hyderabad,AP, India
2000
Chad, Our Group can design and supply a system that will meet any need of your facility. We specialize in process recovery applications, as well as end of pipe technologies utilizing microfiltration systems. We can offer you several distinct advantages in ROI for your project, such as on-site recovery of segregated metals for recycling credit (not a "fee", but actual cash back!)
Additionally, through several unique partnerships that we have, we can even offer you a turnkey facility, incorporating not just treatment, but also finishing systems, chemistries, anode materials, and other products. Please feel free to give us a call! And stop by our Booth at SURFIN 2000 to discuss in greater detail.
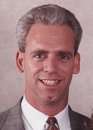
Tom Baker
wastewater treatment specialist - Warminster, Pennsylvania
2000
Q, A, or Comment on THIS thread -or- Start a NEW Thread