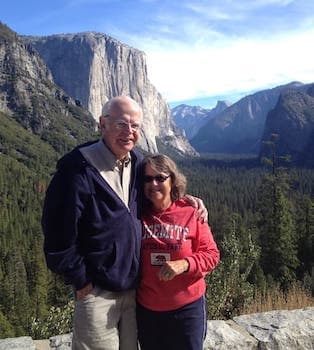
Curated with aloha by
Ted Mooney, P.E. RET
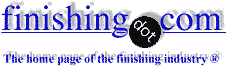
The authoritative public forum
for Metal Finishing 1989-2025
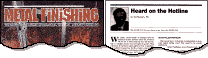
-----
Nickel or Electroless Nickel plating on nitrided steel
Q. We are doing nickel plating 10 µm on nitrided steel surface.
Unfortunately we meet adhesion problem.
What do you recommend in order to improve the adhesion?
For your information, the white layer coming from the nitriding process was removed by sand blasting.
Thank you for your help.
Kind regards,
- Trento Italy
April 13, 2022
A. Hi Gregorio. John Tenison Woods suggests below that even after blasting a Wood's nickel strike is advisable -- but that is before electroless nickel plating, not electrolytic nickel.
John Pease seems comfortable that a nitrided surface that has been blasted should not be especially troublesome. Nonetheless, if you are having adhesion problems on a freshly blasted component where cleaning is obviously not the issue, Wood's nickel probably should be tried.
Luck & Regards,
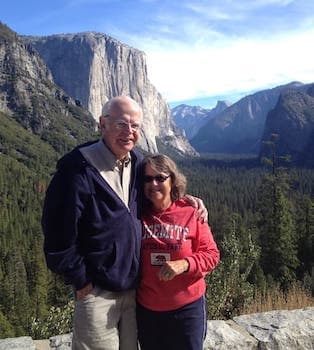
Ted Mooney, P.E. RET
Striving to live Aloha
finishing.com - Pine Beach, New Jersey
April 2022
⇩ Related postings, oldest first ⇩
Q. I would very appreciate if someone know which is the best process for activating nitrided steel for an electroless nickel application.
Do I need to sandblast and give a woods nickel strike before the plating?
Thanks very much
EMMANUEL SCHONWALDMetal-Tech S.A - Buenos Aires
2000
by G. G. Gawrilov
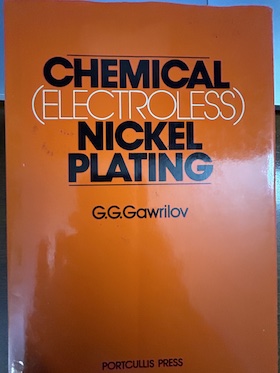
on AbeBooks
or eBay or
Amazon
(affil links)
A. I do not remember doing but a very few nitrided parts, but do not remember any problems.
Nitrided has a high nitrogen and carbon content in the surface of the metal. If you treat it as a high carbon part you should not have a problem. The surface is very prone to hydrogen embrittlement, so avoid long dips in acid. Keep it as brief as possible or use anodic current with it. I think that sulfuric and current works better than muriatic and current.
Blasting will not hurt the follow on plating, but normally you would not blast the area of nitrided surface. Blasting is an effective way of removing surface oxidation.
James Watts- Navarre, Florida
2000
A. Hi Emmannuel,
If you have nitrided parts and access to a sandblaster then use it, but as you suggest it is only half of the problem solved , any "Free" carbon in the surface will not plate with EN thus pin holes in the coating will appear, in my opinion the use of a "Woods" nickel strike is mandatory . You must remember to keep the "Woods" nickel strike in good condition, depending upon usage carbon treatments are necessary on a regular basis, keep the operating parameters within +/- 10% of optimum and all should be OK.
regards

John Tenison - Woods
- Victoria Australia
2000
Multiple threads merged: please forgive chronology errors and repetition 🙂
Nickel Teflon Coating On Nitrided Steel Concerns
2000Q. I require technical assistance and information relating to issues with Electroless Nickel plating of Nitrided Steels. Our company is currently investigating the viability of utilizing the NicoTef process, in an attempt to reduce friction, on plain bearing, shaft journals.
However, we have a number of reservations with the process due to insufficient data which, is not allowing us to reach a conclusive position.
We are hoping that some of the expertise in this forum is able to shed some light on our questions and/or allay our concerns.
Process - Nickel-Teflon (Nico-Tef)
Material - Molybdenum Manganese Steel (Previously Nitrided)
1. Would a chemical reaction be expected by immersing the Molybdenum Manganese Steel material, that has been Nitrided, into any of the solutions used in the Nico-Tef process and or any of the cleaning processes?
2. If a reaction did occur would this cause surface distress/damage to the metal surface?
3. What effect will the Nitrided condition of the material have in the processes?
4. Has any long term detrimental damage been done to the crankshaft as a result of the chemical reaction? e.g. has the Ammonia / Nitriding / Chemical reaction compromised the integrity of the material? Embrittlement?
Thank you
Kind Regards
Peter Vucinic -computerized bearing analysis - Bendigo, Victoria, Australia
2000
A. Peter,
I can't speak specifically about the Nickel Teflon coating process, but can speak about the nitriding process.
It sounds like you are dealing with a gas nitrided steel by your reference to ammonia. This is a thermal treatment process in which nascent hydrogen atoms diffuse into the steel and form nitride compounds with many of the alloys in solution in the steel. Molybdenum, vanadium and especially aluminum are the best nitride formers. This is not a coating at all but a change in the structure to a depth of .010-.015" or so. You don't specifically state depth or the alloy type so that's hard to determine.
Bottom line is that the nitrogen in the nitrided component is not free nor likely to react with a coating. It is present as a compounded aluminum or molybdenum nitride. It's also present in very minute amounts, and present in the diffused layer.
A natural byproduct of gas nitriding is a white layer, which is a surface phenomena, about .0003-.0005 thick. This is pure iron nitride, which acts as a nitrogen "feeder" layer for the diffusion. This is brittle but is typically removed post nitride by mechanical means, although there are commercially available acid salts for removing it.
I would expect no more chemical reaction with the nitride in the material than with the carbides typically present in tool steels or high carbon alloy steels. Nitriding is commonly used on crankshafts and bearing surfaces, and since it's done around 975 °F, embrittlement is not a typical concern.
I hope this information is helpful in allaying some of your concerns for the nitriding process.
John Peaseflight systems - Shelby, North Carolina

Q, A, or Comment on THIS thread -or- Start a NEW Thread