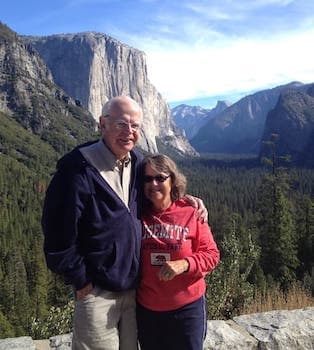
Curated with aloha by
Ted Mooney, P.E. RET
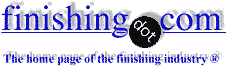
The authoritative public forum
for Metal Finishing 1989-2025
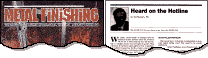
-----
Spider Veining on Powder Coated Aluminum in Coastal Area
2007
We are a metal fabrication shop specializing in commercial handrail located in Central Florida on the space coast. 90% of our work is done in aluminum and 90% of that is powder coated. We use another company to powdercoat our product since our volume isn't sufficient to justify our own PC facility.
We have noticed a phenomenon with the finish on the cap of several coated handrails installed near the ocean. It appears as if there is a raised ridge or vein under the powder coat finish that has appeared over the past 4 months or so. I have asked the Application Company what might cause this.
I was informed that this is a condition known as "spider vein" and is caused by salt air penetrating the coating (which I was told was porous) and oxidizing under the finish. I have been unable to corroborate this on the web. Furthermore we have not experienced this before in over 10 years.
Has anyone had any experience with this problem? Also looking for information on what may have caused this problem and what I can do to avoid experiencing this in the future.
Thank you.
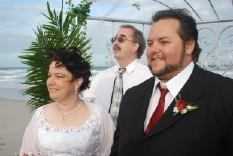
Andrew Benson
metal fab company (buyer)
Cocoa, Florida
I'm sure that the powder supplier would be pleased to work with you and the application shop to resolve this problem; each vendor has multiple kinds of powders. You may also need to investigate the pretreatment. Tiger Drylac is conducting a powder coating class that you may wish to attend.
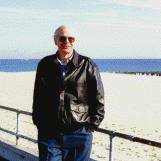
Ted Mooney, P.E.
Striving to live Aloha
finishing.com - Pine Beach, New Jersey
2007
2007
Andrew, there can be a few reasons why powder coating might experience early failure-
1. Wrong pretreatment
2. Powder not cured properly
3. Environmental conditions and paint/pretreatment selection are incompatible.
If you've never experienced this failure before, and making the assumption that you've been using the same coater(s) all along, then something has changed with the painting process. Unless you specified a change, the painter will know what changes he's made. If powder coating was porous nobody would use it for industrial applications.
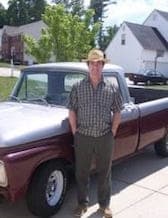
Sheldon Taylor
supply chain electronics
Wake Forest, North Carolina
Search on 'Filiform corrosion of aluminum' for more information.
In addition to investigating the pretreatment procedure, consider corrosion testing. E.g., ASTM D2803, 'Standard Guide for Testing Filiform Corrosion Resistance of Organic Coatings on Metal' comes to mind. Coated specimens are scribed, then subjected to salt & humidity.
See also American Architectural Manufacturers Association (AAMA) standards 2603, 2604 & 2605, conveniently summarized on the Aluminum Extruders Council's Finishes page: http://www.aec.org/techinfo/finishes.html
- Goleta, California

Rest in peace, Ken. Thank you for your hard work which the finishing world, and we at finishing.com, continue to benefit from.
2007
2007
Thank you for the feedback everyone.
I have contacted Tiger Drylac, the powder used was Bengal White a Tiger Drylac product, we have been using this coater for almost 2 years now, and are happy with the service and the quality so far.
Tiger Drylac assured us that the Coating was not porous. They will be sending the local rep around to inspect the job beginning of the week to see if they can help determine what went wrong.
The Powder applicator has earned Tiger Drylac's 3000 hour salt spray certification (or something like that) and tells me that the powder is porous on a molecular level.... and I tell myself .. Well Duh! so is steel or marble ... pretty much everything is porous to some extent on a molecular level.
My greatest concern now is the "blame game". Either Tiger points to the Applicator and says improper pretreatment, and the Coater then points to the powder manufacturer and says bad batch (of powder) etc.
Will keep you updated. And thanks again to all those who have responded.
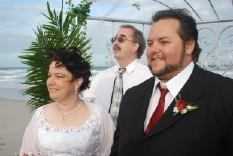
Andrew Benson
metal fab company (buyer)
Cocoa, Florida
First of two simultaneous responses --
What you have is called filiform, or sometimes vermiform corrosion. It can be prevented only by the proper sort preparation and/or primer. The coating manufacturer will be glad to provide the answer.
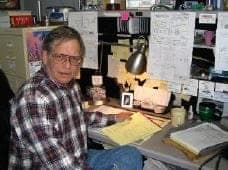
Jeffrey Holmes, CEF
Spartanburg, South Carolina
2007
Second of two simultaneous responses --
A powder manufacturer admitting to defective paint? har har hccccch. I just swallowed my gum.
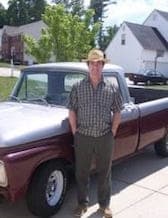
Sheldon Taylor
supply chain electronics
Wake Forest, North Carolina
2007
June 23, 2008
Update:
The coater maintains that it is environmental issues that are causing the powdercoat to fail. The Powder Mfg. is standing by the coater, they claim they are aware and approve the procedure the Coater uses for pretreatment and coating.
For the Record the coater blasts the aluminum railing with a red garnet (media blast) then powders and bakes the product.
They have earned the Powder Mfg. 3000 hour salt spray certification doing this.
What concerns me, now that I have dug much further into this, is that this procedure does nothing to treat the substrate or prevent any corrosion. it simply cleans and profiles. So much for vendor assurances. I feel that our company has been mislead and now we are paying the price.
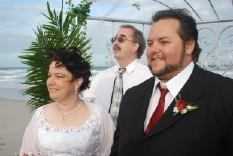
Andrew Benson
metal fab company (buyer)
Cocoa, Florida
Q, A, or Comment on THIS thread -or- Start a NEW Thread