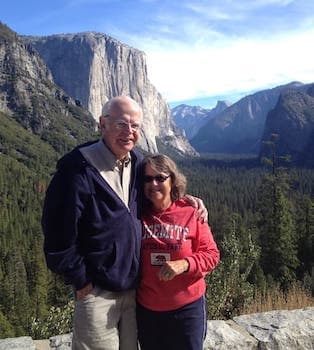
Curated with aloha by
Ted Mooney, P.E. RET
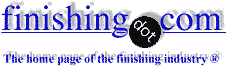
The authoritative public forum
for Metal Finishing 1989-2025
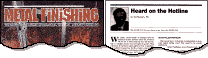
-----
Fractures Observed in Zinc-Nickel Plating
Hello,
My name is Tom Marren and I work in the Quality Department of an aerospace fastener manufacturer. I am not an expert on plating practices but have an issue that is impacting our product and would like to gain an understanding of the observed condition and find a solution.
One of the products we make is a small washer, machined form AMS 6304 bar stock, that requires zinc-nickel plating in accordance with AMS2417. We do not perform the process in-house. Upon receipt of the plated parts we section and mount the parts, in accordance with ASTM B487, to determine plating thickness. We have repeatedly observed fractures in the plating. We have processed these parts at multiple vendors and have observed the same condition.
Is this something you would expect to see in this type of plating and what could be the cause of the condition?
- Fullerton, California, USA
2007
Hello Mr Marren,
There may be a problem in the method of sectioning and mounting the parts. I suggest that you sandwich the plating in between the base metal and aluminum and mould them into one mass before you part the section. After cutting, you may want to highly polish the cut surface very bright and smooth before you look at the microscope.
You may be inducing some fracture into the plating whilst sectioning.
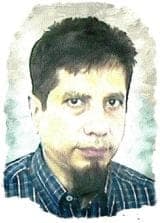
Khozem Vahaanwala
Saify Ind

Bengaluru, Karnataka, India
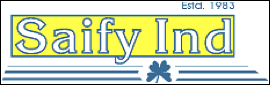
2007
Hi Khozem,
Thanks for your response. We thought that the mounting may be contributing to the fractures also, so we mounted a complete part
(without sectioning) and ground and polished the mount down to view the plating. We still are observing the fractures.
Do you have any other suggestions?
Aerospace - Fullerton, California, USA
2007
Dear Mr Tom,
Nothing I can think of would cause a fractured deposit unless your platers are using two layers of plating.
This would result in your seeing a horizontal fracture and not a vertical one.
Best Regards,
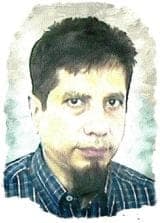
Khozem Vahaanwala
Saify Ind

Bengaluru, Karnataka, India
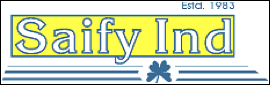
2007
Is your plating parts having a problem of hydrogen embrittlement? HE is a major problem with plated parts.
Prat George- Louisiana
2007
I have used a similar process extensively when I was in industry.
With the zinc nickel co-deposited (5-10 percent nickel) system I have seen vertical cracking running through the full plating thickness. As far as I can tell this is typical of the plating when prepared as you describe. (I know that sounds strange - but it happens every time.) It does not appear to affect performance (salt fog) or adhesion. This plating is characterized by a multi-colored surface, it tends to be relatively hard (compared to say zinc of cad.) I was never able to determine if the "cracked" appearance was characteristic of the "as-plated" condition or a by-product of the sample prep process you described. My suspicion is as-plated.
I have only utilized this type of plating on relatively soft steel parts (less than 38 Rc). Others at my location used it for springs, when properly baked, hydrogen embrittlement was not observed (we tested a large group of springs.) However, the usual cautions about hydrogen embrittlement definitely apply.
Use this plating with caution on threaded fasteners, it has no real lubricity (like cad plate would have) thus preloads developed under torque could be very low. Also under heavy load approaching the elastic strength of the material the material will separate from the thread surfaces. Since it is sacrificial this is not necessarily a big deal, it does however impact re-use and have some interesting effects on pre-load.
- McKinney, Texas
2007

Q, A, or Comment on THIS thread -or- Start a NEW Thread