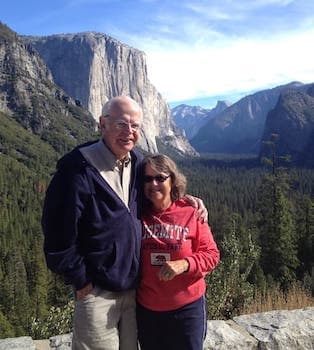
Curated with aloha by
Ted Mooney, P.E. RET
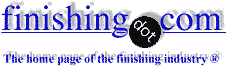
The authoritative public forum
for Metal Finishing 1989-2025
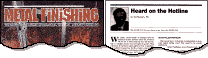
-----
Thickness variation during hard chrome plating in continuous type plant
We are I/c Engine Valve manufacturers. On a valve a stem portion of the component is being hard chrome plated with a @ 6 micron thickness over @ 80 to 100 mm length. Plating plant is of continuous type (Transporter mechanism) having bar type anodes ( @ 500 mm length ). Plating time and currents are being set after calculation. 3 amp / valve with 13 min plating time (11 valves per flag). Valve is being masked on the head portion as well as bottom 20 mm portion with polypropylene caps.
Our problem is that - we are getting variation in plating thickness over the length and the variation pattern is the same. Plating is more at the bottom portion of the stem than the top portion of the stem by 3 to 4 microns, even some times 7 to 8 microns. Valve is being loaded vertically with Head portion at the top. This problem we are facing continuously- Current robbers has to be set in ... is the answer given by the Plant suppliers but how and where is not being told... Kindly guide about any other solution, other than current robbers ... which we can implement..
Manager - Quality assurance - India
2007
In hard chrome plating edges (Top and bottom) draws more current which gives more microns at top and bottom.
To solve your problem, you need to try the following.
1. You need to shorten the anodes length (i.e., 10 to 15 mm lesser then your cathode (Valve) length.If you are loading various lengths of valves, you may try of using plastic caps at the bottom, which will not allow the anode to see the bottom portion of valve. Plastic caps works as a shield which avoids edge build up.For Suitable plastic caps you need to try trail and error method.
2. Realign the anode position (Anode to cathode distance should be around 3"-5".
3. Use round stick anodes.
- Bangalore, India
2007
Could you explain if your equipment is a finger return machine (single file) or a rack machine? Also, what type of chromic acid plating process (sulphate, mixed, or etch-free) is used? We have plated over 24 million valves a year and might be able give you some anode insight to reduce your variation along valve stem.
Tim DeakinNorth Tonawanda, New York
2007
Q, A, or Comment on THIS thread -or- Start a NEW Thread