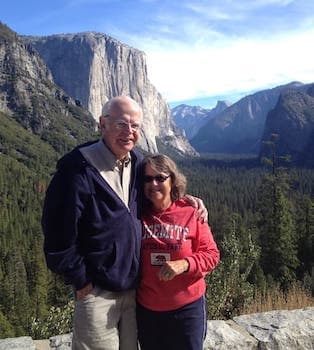
Curated with aloha by
Ted Mooney, P.E. RET
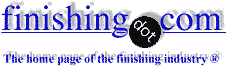
The authoritative public forum
for Metal Finishing 1989-2025
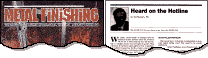
-----
Zinc phosphating on aluminum. Mixed metal phosphating.
Q. I have an assembly where an aluminium ring is pressfit on cast iron. Is it possible to powdercoat the assembly of cast iron and aluminium.? are the pre powder coating processes (i.e., phosphating etc.) the same for both cast iron and aluminium?
Sreeraj MGeneva Innovations International pvt. ltd - Bangalore, Karnataka, India
2005
A. You shouldn't have trouble powder coating it as a unit using normal powdercoating processes, but you will need to have a phosphate that will work with mixed metals. You're chemical supplier would probably be able to give you the best advise with that issue.
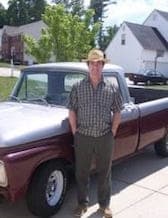
Sheldon Taylor
supply chain electronics
Wake Forest, North Carolina
2005
A. Yes of course, you can powder coat both the part simultaneously. Also, there are special cleaning and phosphating chemicals that can be used for both the aluminum and cast iron parts. Currently, there are many mixed metal lines using such chemicals quite successfully.
Amit Amembal- Mumbai, India
2005
Multiple threads merged: please forgive chronology errors and repetition 🙂
Q. Can we do pretreatment of aluminum components in spray phosphating line if the volume of aluminum is only 0.1 percent of the total volume [MS] of production.
Dinesh ChandraManager Paint shop - India
2007
A. You can spray phosphate aluminum, but dip will work better and faster. The zinc phosphate needs to be tweaked by the manufacturer's specification for the best operation on aluminum.
James Watts- Navarre, Florida
2007
Q. James Thanks for reply
But my question is normally chromating process is recommended for aluminium. If we do the phosphating (zinc tri-cationic phosphate) to aluminium parts then as far as quality is concern what will be the effect.
- India
2007
A. Many people prefer to use a chem-film such as Iridite or Alodine which are trade names for the two largest proprietary brands in the USA, because it is quicker and easier. However, it cannot be used in many countries because of the hexavalent chrome.
Phosphate treatment has been used in the USA for many years on aluminum with steel pins, rivets and etc.
The phosphate process on aluminum requires more attention than on iron or steel. Your vendor should be able to give the parameters for it and any special testing.
If the company that you are selling to authorizes the use of phosphate, then you are fine to use it as long as it meets his specifications. If there are none, then it must just meet his paint specifications.
My personal opinion is that it works very nearly as well as chem-film if applied correctly.
- Navarre, Florida
2007
A. Zinc phosphating chemicals formulated for phosphating aluminium components are available,and used for decades.
S. MEENAKSHISUNDARAM- CHENNAI, Tamil Nadu, India
2007
A. Hi. Zinc phosphating of aluminum has indeed long been done, and it is often the practical answer for a mixed metal assembly, or when production involves only a small percentage of aluminum. As James says, chromate conversion coating is quicker and easier ... but furthermore it's significantly better in terms of corrosion resistance. Please search the site for "phosphate vs. chromate of aluminum", or "chem-film" or "MIL-C-5541" or similar terms to understand how & why chromate significantly improves the corrosion resistance of aluminum.
Regards,
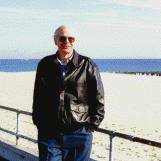
Ted Mooney, P.E.
Striving to live Aloha
finishing.com - Pine Beach, New Jersey
Multiple threads merged: please forgive chronology errors and repetition 🙂
Why phosphate aluminum per MIL-C-10578
Q. Hi,
My name is Sam Rodriquez and I'm mechanical engineer for a aerospace company that overhauls ground base support equipment, structural and electronic components.
My question is what's the purpose of phosphate treating aluminum parts if they do not require a surface protective treatment after. My understanding per MIL-C-10578 [link is to free spec at Defense Logistics Agency, dla.mil], is that the phosphate would be a pretreatment/conditioning for aluminum to clean and provide a better surface for a second protective surface process (chem-film, paint).
Does the phosphate acids form any type oxidation on the aluminum surface for protection in electronic component chassis without a second protective process?
Thanks in advance.
engineer - Chula Vista, California, USA
2007
![]() |
A. The spec you reference is for a phosphoric acid based CLEANER and certainly not intended to lay down a phosphate layer. It's intended to clean and lightly deoxidize the natural oxide - most immersion type deoxidizers contain phosphoric acid. ![]() Milt Stevenson, Jr. Syracuse, New York 2007 A. Specs are a tricky business. I've seen quite a few specs listed/used that really don't do or require anything. CASS comes to mind, but that's neither here nor there. - Pittsburgh, Pennsylvania 2007 |
Q. Sir I am working in Panchkula (india). It is PT and CED coating line on steel and aluminium components of tractors. We are doing steel and aluminium components for phosphating coating in same phosphate tank. Tell me what is the effect on components if we use same tank for both metal and how? Give suitable reason.
I am working here as quality inspector and line chemist. I am getting so many problems here. So I put my question.
Thanks.
Pretreatment and Cathodic Electrodeposition plant - Panchkula, Haryana, India.
December 23, 2015
A. Hi Virender. Although I can't promise "trouble free", mixed metal phosphating is widely practiced as you can see from the thread that we appended your inquiry to.
Is this a zinc phosphating line? Have you worked with your chemical supply vendor to make sure you are using suitable chemistry for mixed metal processing? What is the biggest problem?
Regards,
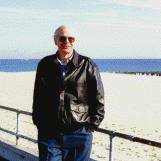
Ted Mooney, P.E.
Striving to live Aloha
finishing.com - Pine Beach, New Jersey
December 2015
Q, A, or Comment on THIS thread -or- Start a NEW Thread