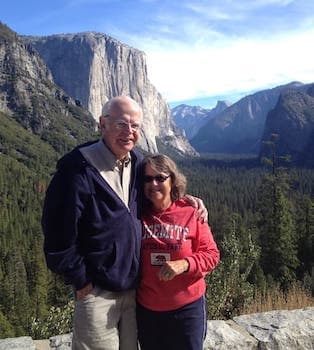
Curated with aloha by
Ted Mooney, P.E. RET
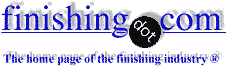
The authoritative public forum
for Metal Finishing 1989-2025
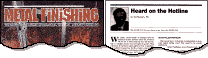
-----
Stay time in phosphated condition
Please tell me maximum time of stay phosphated parts before powder coating and tell us the detail. as per me it is 2hrs maximum within 2 hrs parts should be powder coated.
Please reply,
MANAGER QUALITY - GURGAON, India
2007
I would recommend painting within 24 hours. You might want to ask you chemical supplier what he recommends. If you are in doubt you can phosphate a sample, wait 2 hrs and check the coating weight. Then phosphate a sample, wait 24 hours and check the coating weight and see if there is any variance. You don't really need to re-phosphate until you see a deterioration of the coating weight. This way you can be 100% sure of your knowledge. If you re-phosphate every 2 hours for 6 or 7 hours the coating weight will be so heavy that you will end up with adhesion problems.
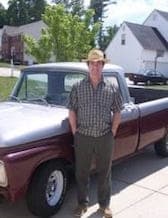
Sheldon Taylor
supply chain electronics
Wake Forest, North Carolina
2007
2007
I maintain that ONE hour is a good safe max limit.
The phosphate coating is a hygroscopic crystal. If there's moisture in the air then it will start absorbing that water as soon as its cool enough (after drying).
The more water it absorbs the more problem you will have.
After powder application, comes curing, and normally at between 200 - 220 °C air temperature.
At this temp, the water absorbed by each crystal will come out, but from a crystal now covered by powder, which is starting to cure. Guess what happens? a little volcano erupts.
It's my opinion that this is one of the major causes of pinholes - water of crystalisation coming out of zinc phosphate during curing.
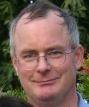
Geoff Crowley
Crithwood Ltd.
Westfield, Scotland, UK
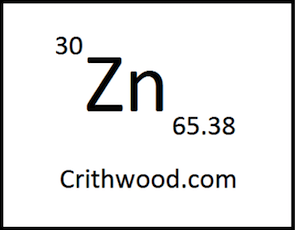
Q, A, or Comment on THIS thread -or- Start a NEW Thread