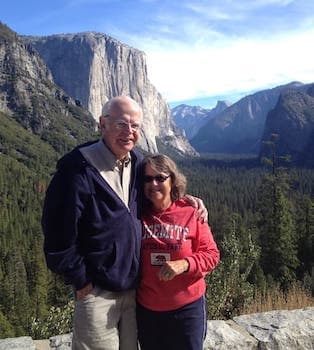
Curated with aloha by
Ted Mooney, P.E. RET
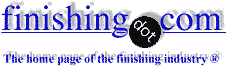
The authoritative public forum
for Metal Finishing 1989-2025
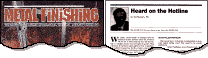
-----
A supreme finish for zinc castings
Hi! We are a lock manufacturer and we would like to be able to supply our customer with a superior product. We would like to know if there are any plating finishes or look-like plating finishes that will give around 1000 hours of salt spray on Hot chamber zinc castings?
Jeff OwensProcess Engineer - Winston-Salem, North Carolina
2007
Hi there,
Have you tried bright nickel chrome finish.
- Durban, South Africa
2007
Yes, We tried Duplex Nickel and obtained 800 Hours. We get about 400 hours with our current copper, nickel, chrome.
Jeffery Reid OwensLock Manufacturer - Winston Salem, North Carolina
2007
2007
Suppliers quote 1000 hours for their EN processes, but that may not mean you'll get it in the real world on your particular parts. If cost were not an object, EN followed by nickel chrome would do it.
However, since you are the manufacturer, a couple of additional thoughts --
1. Salt spray tests are a quality assurance test, not a predictor of real life, because the corrosion mechanism is very different. One quick example: hot dip galvanizing is the most robust finish there is, sometimes lasting 75-100 years of outdoor exposure; yet it performs poorly in salt spray testing where we don't have the slow build of a glassy zinc carbonate skin from reaction with the atmosphere over the months & years. Therefore it is erroneous to use accelerated testing results to select finishes.
2. Different people perceive quality differently, and many customers will prefer a brass component with even a moderately capable finish to a zinc component with a superior finish. Some find a bit of brass tone showing through after a year or two to be no issue, but a salty crusty volcanic eruption from a zinc casting disgusting even on a 10 year old component :-)
3. Zinc is an extremely active metal, capable of galvanically protecting steel, let alone nickel. The tiniest pinhole or slightest porosity and the component is doomed to effusively corrode in an attempt to galvanically protect the nickel. So you may be better off with an organic finish like phosphatizing, followed by e-coating, followed by powder coating. Good luck.
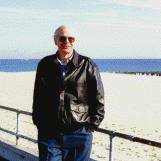
Ted Mooney, P.E.
Striving to live Aloha
finishing.com - Pine Beach, New Jersey
Q, A, or Comment on THIS thread -or- Start a NEW Thread