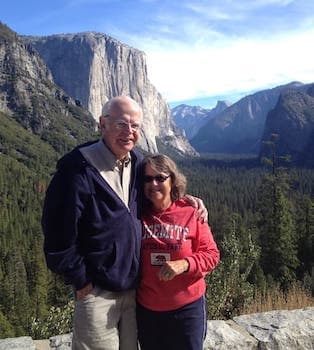
Curated with aloha by
Ted Mooney, P.E. RET
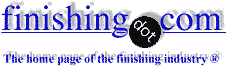
The authoritative public forum
for Metal Finishing 1989-2025
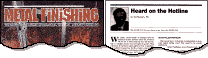
-----
Flaking of chrome plating after finish grinding
We are experiencing flaking of chrome plating at our customer. We heat treat and pre-grind an OD before sending out to our chrome Supplier. He degreases our steel blanks, glass bead blasts, masks & racks, reverse etches and plates the OD (approx. .005"" thick) and sends them out to a centerless grinder. When they return to our plant, we centerless again then plunge grind this diameter. This grinding operation actually goes thru the plated diameter at either end and also thru the diameter in the form of a groove near the middle of the part. We then centerless grind again to establish finish size. Plating thickness remaining on the finished OD is approx. .0035. We do not observe any peeling or flaking at final inspection, but we do have about a .02% reject rate for chipping at these edges.
Do you have any insight as to why the plating adhesion survives a severe grinding operation, yet flakes off at our customer?
Supplier Quality Engineer - Windsor, Connecticut, U.S.
2007
Bob, you don't mention alloy of shaft? If material is heat treated to Rc38 or higher prior to Hard Chrome, you may be seeing hydrogen embrittlement / cracking. Try heat treating 375F for minimum 4 hours (up to 23 hours, depending on shaft alloy and hardness) to stress relieve shaft with in 1 hour of completing Hard Cr plating. This will help drive out entrapped hydrogen under chrome plate. Hope this helps.
Tim DeakinNorth Tonawanda, New York
2007
Two parts out of ten thousand (0.02%) doesn't sound terrible to me. As a matter of fact it sounds pretty good. Anyway, maybe your substrate alloy contains in excess of 2% Cr, Ni, Mo, Va or some other highly passive metals and requires a high fluoride chrome bath or perhaps even a strike in a high chloride woods bath. Also, a careful review of your grinding practice not to remove over two tenths per pass might help.
Guillermo MarrufoMonterrey, NL, Mexico
2007
![]() |
2007 Thanks for the responses. - Windsor, Connecticut Since it only chips where you plunge grind, there is an extremely high probability that you are generating a lot of heat in that area which is causing the chrome to chip. If it were my shop, I would grind the plunge area to near size, especially the width, and mask it off during plating. James Watts- Navarre, Florida 2007 |
Q, A, or Comment on THIS thread -or- Start a NEW Thread