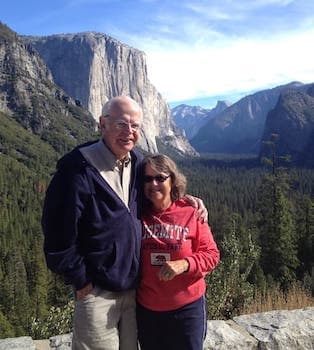
Curated with aloha by
Ted Mooney, P.E. RET
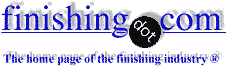
The authoritative public forum
for Metal Finishing 1989-2025
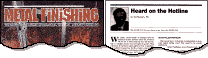
-----
Cadmium plating over aluminum alloys with Electroless Nickel as Undercoat
Q. I looking to see if anyone knows what the thickness of cadmium with olive drab chromate over electroless nickel on aluminum are needed to pass 1000 hour salt spray. Any information provided will be very helpful.
Thank you,
Casey Stein- Tempe, Arizona, US
2003
Q. I am working on a Design Project for the Aerospace Industry which demands that the product (made of die-cast aluminum) be plated with Olive drab Cadmium over suitable underplate and should withstand 1000 hours of salt spray and still exhibit no exposure of base metal evident to the unaided eye.
Can anyone suggest a plating method (the underplate, thickness of the underplate and thickness of Cadmium coating) which can withstand the above requirement?
SOURIAU INDIA - Cochin
2006
A. I do not remember seeing any thickness of cadmium and OD chromate getting 1,000 hours. I have been wrong before though.
My guess is that it would take about 0.0015" of electroless nickel under the cad to get that level of salt spray resistance. I would use a double zincate, an alkaline EN strike, regular EN (high P or boron are best), rinse and immediately go into the cad tank. Nickel passivates very very rapidly.
- Navarre, Florida
2006
Multiple threads merged: please forgive chronology errors and repetition 🙂
Q. Hi,
My customer wants the components which can withstand 1000 hrs salt spray. The base metal is Aluminium. There are two issues here:
1. Whether cadmium plating with electroless nickel as undercoat can withstand 1000 hrs salt spray?
2. If not, what is the best plating with olive green finish to withstand 1000 hrs salt spray?
- Bangalore, KARNATAKA, INDIA
2006
A. Hi Ramesh,
Surface preparation and type of aluminium alloy are two important factors.
With cadmium & olive drab chromate on top of one thousandth of High phosphorous Electroless (25 microns) you can achieve 1000 NSS easily.
- Toronto, Ontario, Canada
2006
A. Hello Sir,
I have five years experience in plating field. I accept Mr. Sridhar's suggestion, but for the component to withstand salt spray test of 1000 hours, undercoat should be alloy plating. High or medium Electroless Nickel is preferable.
I was also facing the same requirement. The past three months we were in a struggle, but we found one process: that is we have to plate high phosphorous electroless Nickel undercoat for 3-5 microns, then do surface coat plating of 12-15 microns. That substrate will withstand 1000 hour salt spray test. We also did the same; now we are happy. Let me know if you try this.
P.KARTHIKEYANconnectors - Bangalore, Karnataka, India
2006
Q. We have been using anodized MIL-DTL-16232 [from
DLA]
electrical connectors, but there is a problem with long lead times. We have looked at other suppliers, but they do not have the insert configurations that we need, nor do they offer the anodized finish.
The standard finish is olive drab zinc chromate primer
⇦ this on
Amazon (affil link)]
over cadmium plating on an aluminum body. In our environment, the connectors can be exposed to salt spray, calcium chloride, hydrochloric acid fumes and wash down with a high-pressure washer. We have found the cadmium plating to be poor protection. Other options include electroless nickel, olive drab cadmium over nickel, olive drab zinc cobalt, non-conductive black zinc cobalt and conductive black zinc cobalt. We have been told all of these finishes are worse than the cadmium plating and like the anodized parts, they are long lead-time.
So we hope that we may be able to find a spray on coating to apply to the standard cadmium plated part to protect it. Does anyone have suggestions?
Thanks,
- Tomball, Texas
2006
----
Ed. note: Hi, Paul. We appended your inquiry to a thread that may answer it. But get back to us with any questions about the previous suggestion of electroless nickel followed by the cadmium plating and olive drab chromate. Good luck.
2007
Q. Dear Sir,
I read your site, it is very interesting. I have some question for regarding my plating line hope you will throw some light on it. I have 20 years experience in electroplating. We are in the field of manufacturing connectors in India.
I want to know cleaning cycle over aluminum & aluminum die castings for Electroless Nickel plating as undercoat & cadmium plating as overcoat followed by olive green passivation. Aluminum die casting used of 6061 grade & 7075 T-6 grade. We are facing Blistering problems.
Please suggest a cleaning cycle for both of the processes.
At present our cleaning cycle is as follows:
1) Degreasing 1) TCE With Ultrasonic 10 MIN.
2) SOAK CLEAN 1) sodium carbonate
⇦ this on
eBay or
Amazon]
:30-35 g/l 2-3 MIN
2) Tri sodium phosphate: 30-35 g/l
3) Teepol: 1.5 -2. ml/l
4) Temp: 40-60 °C
3) Rinse Plain Water 30-45 sec.
4) Desmutting 1) Nitric acid com.: 95% 1.5 - 2 min.
2) Hydrofluoric acid: 5%
5) Rinse Plain Water 30-45 sec.
6) Albond dip ALBOND DIP (CMP): 100 %, Density 10 1 - 1.5 min.
7) Rinse Plain Water 30-45 sec.
8) 80% HNO3 Nitric Acid (80%) 1 min.
9) Desmutting 1) Nitric acid com. : 95 % 1.0 - 1.5 min.
2) Hydrofluoric acid : 5 %
10) Rinse Plain Water 30-45 sec.
11) Albond dip ALBOND DIP ( CMP) : 100 %, Density 10 20-30 sec
12) Rinse Plain Water 30-45 sec.
13) Electroless nickel Atotech 15-20 min. 2.5 -3 micr.
14) Rinse Plain Water 30-45 sec.
15) Rinse Plain Water 30-45 sec.
16) Cadmium plating Metal 22 g/l,T. CN 150 g/l 35-45 MIN. 10-12 micron.
17) 0.5 % HNO3 0.5 % HNO3 30 sec.
18) Olive drab pass., Atotech 35-40 sec.
19) Drying Centrifugal dryer 5 min.
20) OVEN TEST 150 °C 1 hour.
21) Inspection Under 4 x magnification.
I am sorry for asking question without cleaning cycle. Above cleaning cycle for your
information. We have blister problem after oven test. Blisters are very micro in nature,
sometimes we can not see with naked eye. My customer is checking this jobs at 10x
So kindly suggest any specification you have for inspection.
Components have burr inside the jobs. Is it a cause for blisters?
Please STUDY AND GIVE SOME GUIDELINES WHICH WILL BE HELPFUL TO US.
Thanks,
DEPUTY MANAGER - PUNE, MAHARASTRA, INDIA
A. It has been a long time since I have done this, so I may be wrong. I think that your step 8 is too strong an acid and for too long. You only want to remove most of the zincate, not all of it. If you have to go back in the desmut step, then you definitely stayed in the acid step too long and you are probably worse off than if you did a single zincate.
I would run some lab tests on 20, 30, 40, 50% nitric vs. your 80% nitric to see what will work best for you. It seems to me that we used a 25% for 30 to 45 seconds rinsed and zincated again.
- Navarre, Florida
2007
A. Hi Kamlesh,
Yes it is tough to clean aluminium die casts and there is no universal desmutter, for all alloys. They are many proprietary solutions for Preparation.
- Toronto, Canada
2007
A. I too have struggled trying to plate electroless nickel onto aluminium (at a competitor of yours!). The supplier company you mentioned provided an excellent pretreatment sequence. I think you should bear in mind that the fault may be in the aluminium alloy. Do you have blisters on all aluminium components or only on some? I suffered once because someone changed supplier of a free cutting aluminium containing a lead-bismuth phase. The new supplier's lead-bismuth phase was in larger particles and the electroless nickel would not plate over them. I know it is expensive but an SEM examination of a section through your blisters may reveal what is causing them.
Nick Clatworthy- Whitstable, Kent, UK
2007
A. Dear KAMLESH,
I too have struggled trying to plate electroless nickel onto aluminium. But you want to do ELECTROLESS NICKEL STRIKE Plating before ELECTROLESS NICKEL Plating
- Bangalore, Karnataka, India
January 6, 2013
May 2015
Hi. The only thing I can add to this excellent advice, Kamlesh, is that if the aluminum diecastings are poor quality (if they have cold shuts for example), they will blister regardless of the treatment cycle. Good luck.
Regards,
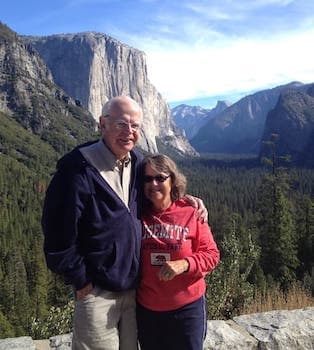
Ted Mooney, P.E. RET
Striving to live Aloha
finishing.com - Pine Beach, New Jersey
Q. I have been reading the string of messages and responses and I have a question. What specification calls for 1000 hrs of salt spray?
Manuel Robles- San Diego, California USA
May 19, 2015
A. SAE AS85049, Finish W is one example of a 1,000 Hr Salt Spray Requirement.
Robert Small- Mooresville, North Carolina
November 6, 2016

Q, A, or Comment on THIS thread -or- Start a NEW Thread