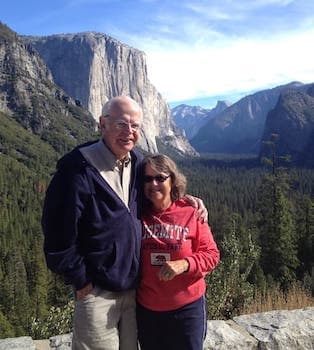
Curated with aloha by
Ted Mooney, P.E. RET
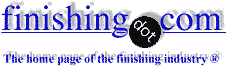
The authoritative public forum
for Metal Finishing 1989-2025
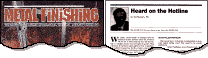
-----
Fire safety of Shot-blasting machines
Q. Sirs,
I'm a production supervisor in a die-casting company in the outskirts of Chennai, Tamil Nadu. After the die-casting process and fettling process, we do shot blasting on our parts to get good surface finish. We use S110 and S170 Steel and Aluminium shots in the ratio of 3:1. We have 6 shot-blasting machines.
Recently, there was a fire accident in our plant due to the dust of the shot blasting machine. This is the second time to happen in the last 4 months. Much of our property was damaged. Luckily no one was hurt or affected.
Please suggest ways to prevent such fires in shot-blasting machines. Also tell about the maintenance and safety related features that we should follow, to avoid such an incident in the future.
Expecting more suggestions from you, sirs.
Thanks.
Production supervisor - Chennai, Tamil Nadu, India
2007
![]() |
A. Fine zinc dust
⇦ this on
eBay or
Amazon [affil links]
is quite combustible if there is a hot enough heat source to get it started. The airborne dust can actually form an explosive mixture with the right ignition source. - Navarre, Florida 2007 A. Good afternoon: - St Louis, Missouri 2007 |
A. Rajkumar, If I understand your working mix of abrasives,you are using steel shot with Aluminum shot in a 3:1 ratio? How well does this abrasive mix presently clean the parts? Using this mix will yield Both FeO and Al dusts and present a fire hazard.
One approach would be to use another abrasive, stainless steel cut wire shot. I have experience where it lasts 20x longer than S70 or S110 and even longer than Al shot, with out the FeO or Al dust issues. The primary dust will be that of the substrate. Its worth a try in one machine.
Could you respond as to the material of the die cast parts? Are they Zinc? Another type of abrasive that may also work on your die cast parts is Zinc cut wire shot. This would eliminate the FeO dust and aluminum dust if the substrate is Zinc.
Some equipment changes to reduce dust fires may be a simple drop out chamber in the dust collector plenum. This would allow dust particles to fall out for easy daily removal.
North Tonawanda, New York
2007
A. We used to have shot blasters to clean our welded steel cabinets prior to painting. We used iron shot on mild steel parts. This dust is also very flammable We installed lime injectors on the system that continuously injected a small amount of powdered lime into the air stream. This helped but didn't cure the problem.
Tom Wardmanufacturing transformers - Jefferson City, Missouri
August 18, 2008
(1994)
by Miles L. Croom
on AbeBooks
or eBay
or Amazon
(affil links)
A. Hello Rajkumar,
Please Add Mineral Abrasive Powder to your shot blasting Machine 0.5 to 1 liter/day/Machine.
This can make your shot blasting machine performance good and can make dust non flammable. We have tried this at many places and results are very good and dust does not catch fire. Also, addition of this powder cleans your machine as well. It has tendency to suck all the dust and remove all the oil, grease and dust on shots and increase the life of coating if any after shot blasting.
You can add this powder in all types of Metal Abrasive.
Regards,
ABRASIVE BUSINESS - Pune, Maharashtra
September 6, 2016
Q. Deepak Singh,
What Mineral Abrasive Powder are you suggesting to add to the shot blasting machine to make the dust non flammable?
Regards,
- Fort Recovery, Ohio, USA
January 25, 2018
April 12, 2018
A. My company is a distributor of shot blast equipment as well as dust collection equipment. I also own another company that builds wet dust collectors for combustible dust applications. That is what we are talking about here... combustible dust. Aluminum, titanium, magnesium, zinc, etc are all combustible dusts. When they are mixed with other metals (especially carbon steel), they become highly combustible. Since shot blast machines often use steel shot on aluminum parts, dust collector fires are very common.
While I have never heard of mineral dust being added to the abrasive (it can contaminate the substrate of the parts being blasted), mineral dust (limestone) is used to help prevent dust collector fires. It is injected into the air stream between the process machine and the dust collector. It coats the filters to help prevent combustion as well as absorbing oils from the dust. It is not a fail-safe, but it helps. A complete prevention system is necessary to completely mitigate fires and explosions:
> Limestone adders
> Spark arrestors
> Deflagration vents (prevent fire/explosion from traveling back to process machinery)
> Powered slide gate on exhaust
Smoke/heat/spark detectors attached to a control panel to shut off blower, pulse board and close exhaust slide gate to shut off fire air supply
Wet dust collectors will perform the same function as the above, however they do not work well in applications that have a great deal of dust that is smaller than 5 micron. Unfortunately, blasting applications always generate large volumes of dust smaller than 5 micron.
- Pomona, California
Q. Dear All,
We are also facing the same issue, can anyone suggest what kind of fire suppression system we can use in this.
Manufacturing. - delhi, India
November 17, 2018
A. Hi Liju. Please clarify what it is that is not clear to you. You say your issue is the same one that has already been answered 6 times, so I'm not sure where the confusion lies. Thanks.
Regards,
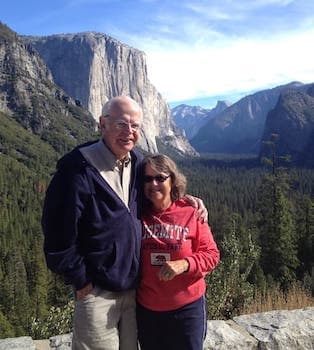
Ted Mooney, P.E. RET
Striving to live Aloha
finishing.com - Pine Beach, New Jersey
November 2018
Q, A, or Comment on THIS thread -or- Start a NEW Thread