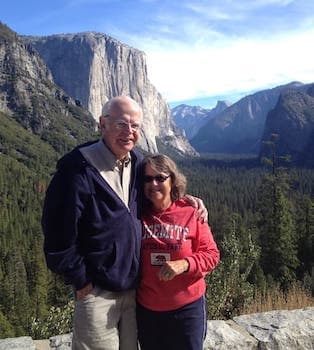
Curated with aloha by
Ted Mooney, P.E. RET
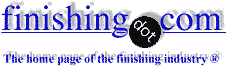
The authoritative public forum
for Metal Finishing 1989-2025
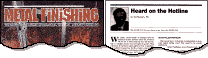
-----
Has anybody built a home-made micro-arc power supply?
Tip: Readers want to learn from Your Situation 🙂
(little can be learned from abstract questions, so many readers skip them)
Q. Arc coating? Is there a method whereby a metal object would be in a negative electrical charge, while a positive (live) powder or liquid could be sprayed at it causing it to attract and weld the coating to the object?
Bill Dakelski- Tulsa, Oklahoma
October 15, 2021
A. Hi Bill. There is arc coating in PVD processes, and in a special type of anodizing, in some flame spraying, and elsewhere. There is certainly electrostatic powder coating, but in most cases the powder doesn't become permanently attached to the substrate until it's subsequently melted on in an oven. Please introduce yourself and the details of your own requirements or situation; I can't figure how to go much further without it :-)
Luck & Regards,
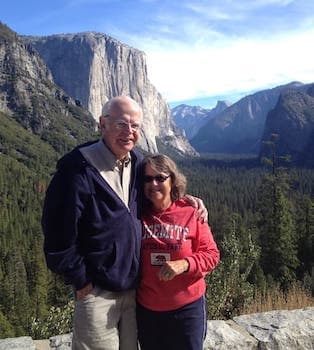
Ted Mooney, P.E. RET
Striving to live Aloha
finishing.com - Pine Beach, New Jersey
October 2021
Q. Thanks for your response. I am a User Reengineer. I regularly reengineer countless things in every way imaginable, and have been doing so for about 26 years. Here is a synopsis of the concept:
appropedia.org/User_reengineering
The basic idea is that things should be designed to inherently last as long as possible, rather than to be disposable. Coatings are by their nature not permanent, the preference is for non-coated things. The coating on many items is not only unnecessary but degrading in usefulness, maintenance and aesthetics (e.g. paint on brick). However, some things may be aided by coating, (fewer than you may think), so my endevour here is to find a coating process for iron, that will improve it in certain uses where rust is undesirable.
User reengineer - Tulsa, Oklahoma usa
October 21, 2021
A. Hi again, Bill. In wanting things to last longer, you and metal finishers are on the same side. We can't stand that lawn furniture, as one simple example, lasts 2-3 years these days when we know exactly how to make it last 20 or 30. We can't stand the price pressure to finish it poorly, nor the fixation of regulators on the ounces of phosphate that shops want to use to protect tons of steel from having to be re-mined, re-smelted, re-rolled, re-fabricated, re-finished, re-packaged, re-shipped, resold, and ultimately landfilled every few years.
The basic purpose of most metal finishing is improved wear resistance, corrosion resistance, and life. And both you and we are usually far more concerned with the life of the original product than the convenient re-usability of the scrap.
There are different corrosion scenarios but, when applicable, hot dip galvanizing is usually the best way to protect steel from rusting. Some bridges and towers have lasted a hundred years. Gold plated pocket watches have lasted 100 years as well, but a lot of gold plating today is about 1/100 the thickness of those old watches :-)
Luck & Regards,
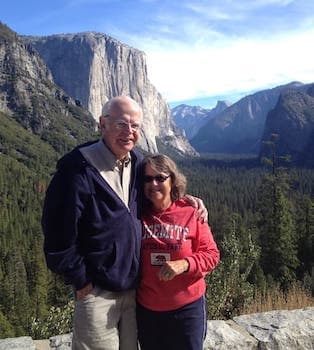
Ted Mooney, P.E. RET
Striving to live Aloha
finishing.com - Pine Beach, New Jersey
October 2021
Thanks for your valuable response; hot dip galvanize, powder coating, porcelain enamel and other such coatings are all superior to available traditional in-service re-coatings that I am familiar with. My endeavor is to by inquisition, serendipity, or adaption find a state of the art surface that may be applicable to things that can not go back to the build stage. Pie in the sky perhaps but not abstract impossibility; the collective savings at stake of material and time is enormous.
reengineer - tulsa, Oklahoma
November 9, 2021
⇩ Related postings, oldest first ⇩
Q. I am a retired physicist/EE interested in a low-cost power supply for micro-arc coating experiments on very small parts in the range of a square cm. The Russians and Chinese seem to concentrate on very large parts.
Does anyone have information on preferred power supply characteristics suitable for workshop or laboratory use? I can build one myself but can't seem to find specs or schematics on what's required electrically.
Many thanks
hobbyist - Longboat Key, Florida, USA
2007
Q. I'm also looking for all the info I can find in regards to building my own power source. Please, any Help is Good help.
David J. BronkSmall private Business wanting to add a Micro-arc Anodizing / Plasma Electrolytic Oxidation line - near Winnipeg, Manitoba, Canada
2007
Q, A, or Comment on THIS thread -or- Start a NEW Thread