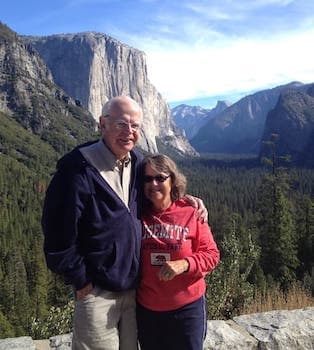
Curated with aloha by
Ted Mooney, P.E. RET
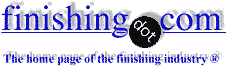
The authoritative public forum
for Metal Finishing 1989-2025
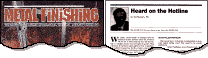
-----
Corrosion resistance of galvanized 1018 steel vs. 416 ss.
2007
I am an entrepreneur building a tool that will be used by fishermen. The tool will get wet from time to time (with fresh or ocean water). I need to use steel that can be easily machined, is hardenable, and shows good corrosion resistance. I can't decide between:
Regular 1018, case-hardened with zinc plating and sealed with black chromate
Or, 416 ss that has been hardened via heat treatment.
Or, 303 ss (only hardenable through cold work?)
My questions are:
Which would be most corrosion resistant?
I've tried to study cold work hardening but I don't understand it very well. Is it more expensive than heat treatment? Can it be used on a finished item without destroying the (fairly precise) dimensions? Does it provide a good level of hardness, akin to heat treatment?
I am open to other material suggestions, but I must keep costs reasonable.
Thanks,
product designer - Irvine, California, USA
I would not advise using A-1 or 416. You might want to try 316.
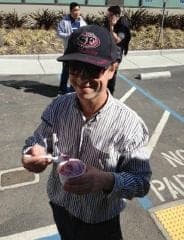
Blake Kneedler
Feather Hollow Eng. - Stockton, California
2007
Among your options, No. 2 eyes closed. Hardened SS416 will be hard and corrosion resistant enough for the described environment. You may also want to consider 1018 case hardened but electroless nickel plated instead. About work hardening it means repeated deformation. You don't want that.
Guillermo MarrufoMonterrey, NL, Mexico
2007
2007
Keep this in mind when considering 416:
- Poor resistance to general corrosion, due to the sulfur addition
- Very poor resistance to chloride pitting and crevice corrosion - not suitable for any marine applications at any temperature
- Low ductility - cannot be bent around a tight radius, or heavily drawn
- Poor weldability - not regarded as weldable
Source: Atlas Metals
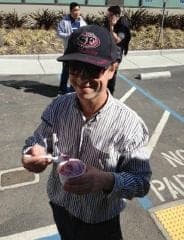
Blake Kneedler
Feather Hollow Eng. - Stockton, California
Q, A, or Comment on THIS thread -or- Start a NEW Thread