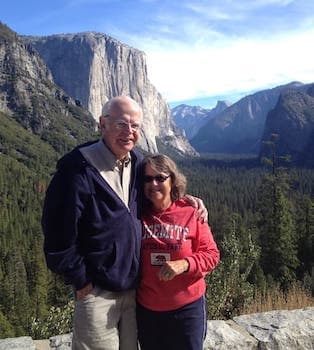
Curated with aloha by
Ted Mooney, P.E. RET
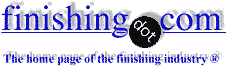
The authoritative public forum
for Metal Finishing 1989-2025
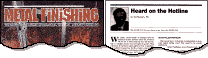
-----
My 316 is rusting! what can I use to passivate?
Q. I installed an exterior stainless steel railing using 316 series 3 months ago in a suburb of Chicago. Homeowner called to let me know that there were orange marks on his house. I figured one of the galvanized screws got rubbed raw going through our stainless plates for connection - not the case... The entire rail is getting spots of oxidation all over it verticals pieces, horizontal- everywhere. The stock shapes are 3/8"x2" top rail and posts with 1/2" solid rod intermediate bars. I've sent a piece back to get tested but all fingers point to a 316 series heat lot. It has no obvious environmental threats, I just don't know. The homeowners probably think I'm some kind of snake oil salesman because I told them it is more costly than 304 but will NEVER rust. Anyway, this has never happened to date and I'm a little confused. I am looking for some sort of paste I've heard about that will take the rust off and coat the stainless. Does anyone know of a brand name or certain chemical I should use? This is installed on a synthetic decking material and has connections into dryvit. I would not want to mess up their home any more than I already have. Please advise. Thanks
- Chicago, Illinois
2007
A. The picture is not good enough to tell, but from the size ,shape and spacing of the spots, I will guess that someone used a wire brush on it. Another guess is that the brush was made out of 400 series SS, which will rust. Tiny tips of the 410 are stuck in the finish of the
316 and form a weak battery of corrosion.
A couple of firms that advertise at this site sell a citric acid based passivation that might work. An outside possibility is that
naval jelly
⇦ this on
eBay or
Amazon [affil links]
might work. A further guess is that you will have to clear coat the ss after you remove the indications of rust.
You may have to wet sand the entire rail with decreasing grit size paper.
- Navarre, Florida
2007
Q. James,
Thanks for your response unfortunately there was no 400 series wire brush used on it. We take great precautions not to mix tools or abrasives in our processes. The last abrasive used was a scotchbrite wide belt on our timesaver. I just got the metallurgical report back from the mill and it is confirmed 316 and everyone I've spoken to is dumbfounded still. It is quite a conundrum.
Joe
- Chicago, Illinois
2007
A. Joe,
Your surprise about the rust-stains on 316 or 304 in outdoor-applications surprises me.
In my region (Belgium/Europe) practically all outdoor SS 316 or 304 is getting stained after some period, if it is not electropolished.
In my experience, electropolishing is the only finish that realises a rust-free surface for many years in outdoor applications in practically all circumstances.
Of course there are situations and applications where simply passivated SS will remain free of rust; regular cleaning with water and soft detergent is a good help to keep SS in good shape.
- Brugge, Belgium
2007
A. Mr. Colosi:
I agree with Mr. Watt's assessment of what could be causing the rust stains. Also, if any of the materials you used to finish or machine the 316 rails were previously used on carbon steel, carbon steel particles could have been transferred onto the rail surfaces, which would then rust. The treatments suggested by Mr. Watts would help in this case. Hope this helps.
Thomas Kemp
- Erie, Pennsylvania, USA
2007
A. I feel for you.
The first thing to realize is that Stainless steel is not stain proof, only stain resistant. it stains less than regular steel.
While I agree with James, keep in mind that its not just tooling that can cause contamination, We do Stainless Steel railing every so often and while our primary focus may be Aluminum, we clean the shop particularly well prior to starting a Stainless Job (to get rid of any steel dust) and enforce a strict anti-contamination policy.
Grinders/ saws/ tables/etc. that have been used on other jobs must be blown clean prior to being used (not just changing the grind/sand disks) Another source of contamination is handling - Make sure that employees do not handle steel and then handle Stainless.. The oils from their hands mixed with steel dust create rusty fingerprints.
Clean up- after finishing wiping the job down with a clean
(new)cotton cloth and a soap and water solution. let that dry and look for stains.. remove any staining and wipe down again with a
acetone
⇦ this on
eBay
or
Amazon
[affil links] Warning! highly Flammable!
or
lacquer thinner
⇦ this on
eBay
or
Amazon
[affil links] Warning! flammable!
cloth.check for stains again, the less you have to do the better off you are.
Starting by Eliminating potential sources of contamination, finish by ensuring no environmental contaminants. - a good clearcoat can help with that.
Passivation - We have a local company that specializes in that for the space industry. Fortunately we have had to use them.
Be aware that passivation and/or pickling can change the color/ finish of the job.
Good luck.
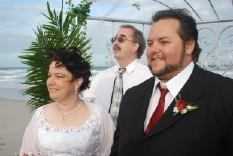
Andrew Benson
metal fab company (buyer)
Cocoa, Florida
A. SS Discolouration,
Only way I know to determine exact mechanism is by X Ray Photoelectron Spectroscopy.
Good Luck from Ireland
- Dublin, Co Dublin, Ireland
February 14, 2008
A. First verify alloy type then verify if passive state.
Stainless steel testing kits are available for both.
Koslow Scientific Company

Englewood, New Jersey
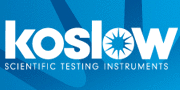
Q, A, or Comment on THIS thread -or- Start a NEW Thread