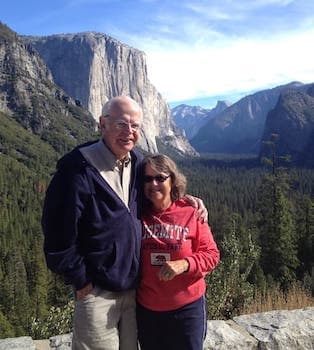
Curated with aloha by
Ted Mooney, P.E. RET
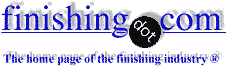
The authoritative public forum
for Metal Finishing 1989-2025
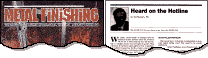
-----
Rust protection and rust removal from steel and stainless bearings
Q. Hi,
We have a problem of rusting on ball & roller bearing OD, ID face etc,. We have identified that the problem was due to inferior rust preventive used. but, how to remove the rust that has already present?
Regards,
S MEENAKSHI SUNDARAM- Chennai, India
2002
A. Most mild acids would work (oxalic, phosphoric, etc.) but you probably don't want to use the rusty bearings anyway. They will have flat spots & pits where the rust was. Not what you want in a bearing.
Tom Gallant- Torrance, California, USA
2002
2007
Q. Hi all,
We are in a Plastic injection molding business. Recently we have an recurring issue with rust developing on SS ball bearing (diameter~0.13 mm) that are auto inserted to the plastic part right out of the molding process. So far our customer has found ~30% of rejects due to this issue. For your info:
- SS grade use on the ball bearing is AISI440C (we outsource this bearing)
- the Bearing is Citric passivated by our supplier
- Plastic Molding temperature may range from 240-300+ °C
- We did not see the rust during our outgoing inspection
At the moment we have not been able to point out the root cause due to the randomness (30% rejects) of the problem. So far we have heard many mixed opinions (degradation of the chromium oxide on the bearing due to high temp of the plastic part it is inserted to; findings of fluoride on the lab test) but none have really explained the randomness of it. I'd appreciate any help I can get. Thanks
Regards,
Ed
Plastics Engr - Singapore
A. Many plastics contain chloride or fluoride, both of which will accelerate corrosion. Then make it very hot and the rate of corrosion goes exponential.
0.13 mm is so tiny that I will not even guess if there is an oil that you might coat the bearing with. Jewelers coat old watch gears with the vapors of kerosene over night for lubrication. Note that this is vapors only, no dipping. It might help if you could coat them before insertion.
- Navarre, Florida
2007
2007
A. Hi Eddy,
What James Watt says is, I feel, very intelligent. If you are using PVC, yes, you sure could get some 'chlorides' due to the high temperature ... and PVC will ignite at 540 degrees (but I've forgotten if that's C or F).
The other point is the citric ... is that diluted at all? Hopefully not with seawater.
Lastly, you live very close to the sea, i.e., good ole chlorides again.
... and I recall Singapore having problems with welding 3l6 L railings abutting the sea due to weld temperatures.
A squirt of 3 in 1 oil might lubricate those bearings.
Cheers ... ex plastics fabricating business.
P.S.I have a gut feeling that James did some training in Singapore
... 500 years ago ?
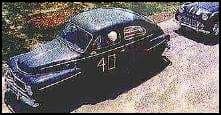
Freeman Newton [deceased]
(It is our sad duty to advise that Freeman passed away
April 21, 2012. R.I.P. old friend).
A. The corrosion resistance of 440C is often reduced by poor alloy chemistry or improper heat treatment. Low Cr content (near bottom of 16-18 wt% range) and high C (near top of 0.95-1.20 wt% range) makes the metal phase more susceptible to Cr depletion via carbide formation.
Heat treatment in air may deplete the surface of Cr (& C) and necessitate material removal. An excessive quenching rate (using water) may cause microcracking; too slow a quenching rate allows excessive Cr depletion from the metal into carbide phases. Too high a tempering temperature increases susceptibility to intergranular corrosion.
Suggestion: Heat in a protective atmosphere + oil quench, or heat in vacuum + use forced inert gas quenching. Stress relieve 2 hrs at 200 °C [The molding process will provide a short, second stress relief].
Test samples from each passivated batch of 440C by either the 24-hour high humidity test or the DI water immersion test (alternate 1 hr immersion & 1 hr air drying, for 24 hrs total). See QQ-P-35C
[from DLA]
or ASTM A967, 'Standard Specification for Chemical Passivation Treatments for Stainless Steel Parts' for details. This way, can avoid using the 440C bearings most likely to corrode after assembly.
Search this site for 440C passivation for more information.
Consider Custom 465® from Carpenter Technology, Cronidur® 30 from Barden Corp. or ES1 from Dynaroll as improved alternatives to 440C.
- Goleta, California

Rest in peace, Ken. Thank you for your hard work which the finishing world, and we at finishing.com, continue to benefit from.
2007
Rust protection for bearings
Q. Hello! I'm an amateur anodizer and was wondering if there is a good way to protect steel and stainless steel bearings from rust. Can they somehow be anodized to protect them? Also wondering if there is a good way to remove rust from crusty bearings. Thanks for any input!
Ryan D [last name deleted for privacy by Editor]Hobbyist, high end fidget spinner collector/finisher - Seattle Washington USA
September 26, 2018
A. Hi Ryan. We added your inquiry to a thread on that topic. Tom tells us how to remove the rust, but warns that ball bearings aren't much good once they've pitted and rusted.
Stainless bearings should be made of good grades and passivated as Ken notes. Steel bearings can be zinc or zinc alloy plated and frequently are.
The normal grease lubricants for bearings can afford some corrosion protection, so keep them well greased, and if you're sloppy about it and get grease on the outside of the bearings, all the better :-)
Regards,
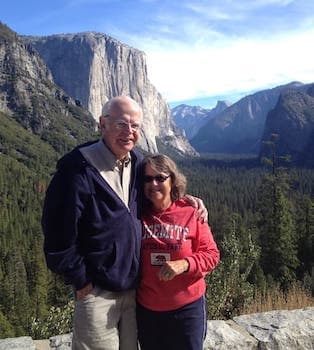
Ted Mooney, P.E. RET
Striving to live Aloha
finishing.com - Pine Beach, New Jersey
September 2018

this text gets replaced with bannerText
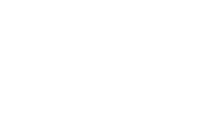
Q, A, or Comment on THIS thread -or- Start a NEW Thread