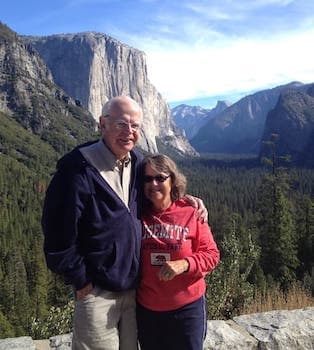
Curated with aloha by
Ted Mooney, P.E. RET
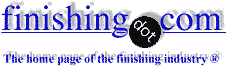
The authoritative public forum
for Metal Finishing 1989-2025
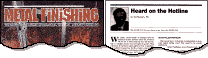
-----
Achieving a specified hardness in nickel plating
Q. The achievement of a specified hardness level (usually specified in the Vickers or Brinell scales) is sometimes called for in nickel plating of components, in my case aircraft propeller components.
My question is how does one control the hardness of the coating? I have seen a number of references to the fact that the hardness level can be controlled but never any details as to how you actually do this. Does anyone have the answer?
- Johannesburg, Gauteng, South Africa
2007
2007
A. Yes, it is possible to control, to some extent, the hardness of electroplated nickel. Among the parameters which influence hardness are bath composition, pH, temperature, current density, agitation, contaminants, and the use of metallic and non-metallic addition agents. All of these things interact simultaneously, and it's a book-length subject.
I'd suggest you do a Google search and also contact suppliers of nickel plating processes.
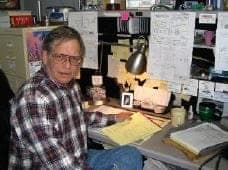
Jeffrey Holmes, CEF
Spartanburg, South Carolina
A. Some nickel bath compositions are easier to control but are more expensive (sulfamate). Some are purposively hard as plated such as the ammonium sulphate-low nickel content bath. Generally, lower current densities and metal concentration, higher pH (above 5) and low bath temperatures favor higher hardness. Get a copy of a good plating book as these are not linear functions.
Guillermo MarrufoMonterrey, NL, Mexico
2007
A. The hardness of a nickel deposit is controlled by the use of hardeners. The most common ones for sulphamate nickel are saccharin and NTS, although there are numerous other ones. Personally I prefer saccharin because it is easier to use and control. You can also use cobalt as an additive to harden nickel. The simplest way to control hardness is to control the amount of hardener you add to the bath. There are some splendid publications by NiDI on the control of nickel plating baths, so I suggest you look at their website for more details.
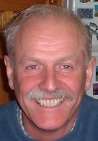
Trevor Crichton
R&D practical scientist
Chesham, Bucks, UK
2007
Q. I am having a challenging time reducing the hardness in our nickel tanks. Our spec. allows us no more then a hardness of 300. But 2 out of 3 tanks are out of spec. One is 306 and the other is 328. I have tried to Platinum dummy the tanks and have had some but very little success. Does any one in your shop know how to reduce the hardness in Sulfamate baths? I also would like to know what drives the hardness levels up. Thanks for your help.
Guy
- North Berwick, Maine. Born in the USA
November 2, 2010
A. All of the above answers still hold true. You have to look at variables that you control; current density, pH, impurities, solution concentration, organics, temperature, addition of wetting agents, and hardeners like saccharin. May want to try a simple carbon treatment first and see how that does. Don't expect to pull out the hardeners though as they don't pull out easily. I would also get the literature that was suggested above by the Nickel Development Institute and keep it on file. Lots of great information in them. I know I review mine every six months or so.
Jim Schwartzmyer- North Tonawanda
November 4, 2010
A. If you are not using a hardener, then you very probably have a trash organic problem. Do some jar testing with a hull cell to see if it will take 2 or 3 carbon treatments to solve the problem. Also, if you are using SNAP A/M or the equivalent, it is easy to add too much which will affect stress and hardness.
How are you doing on your stress tests?
- Navarre, Florida
November 5, 2010
November 8, 2010
A. Dear Guy Boucher,
All reactions so far are right, there is still some more:
Probably your problem is the fact that, due to hydrolysis, the nickel sulphamate slowly decomposes into sulphate.
If the sulphate levels rise, inevitably the hardness of the deposited Ni rises too.
Hydrolysis is enhanced by lower pH, higher temperature and lower [Ni].
Probably the best thing to do for a constant results is renew some of the electrolyte on a regular base as well periodically and reflect this in the cost of the product.
Success,
Harry.
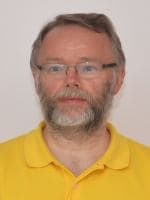
Harry van der Zanden
consultant - Tilburg, Netherlands
Q. I am doing nickel coating on a continuous caster copper mould plate in a concentrated nickel sulfamate bath (Ni speed process). I am getting hardness in the range of 200 - 250HV. My concern is how to get higher hardness (300HV to 340HV) only in the bottom surface of the plates (up to 300 mm from the bottom) where much wear resistance of the coating is required. How can I achieve this without adding any additive or hardener or cobalt in to the bath?
Balram P. Kumba- India
May 8, 2013
![]() |
A. Deposit hardness increases: (1) with lowering metal content, (2) raising temperature above 100 °F, (3) increasing current density (4) raising pH at the expense of brittleness. Cobalt is still the best way but it takes an AA to control it. ![]() Robert H Probert Robert H Probert Technical Services ![]() Garner, North Carolina ![]() First of two simultaneous responses -- May 9, 2013 A. That is very critical application not a trial/error situation. If you are serious, you should hire a specialized consultant. There are just a few in the world knowledgeable in this multi-layered heavy nickel plating. - Monterrey, N.L., Mexico Second of two simultaneous responses -- May 10, 2013 |
A. That's good advice, Guillermo -- no plating is more difficult than the plating on continuous caster molds. But based on some work he and I did together in that industry, I believe that finishing.com's supporting advertiser, Robert Probert, is one of those few who is capable of supervising such a development project.
Regards,
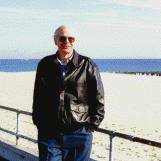
Ted Mooney, P.E.
Striving to live Aloha
finishing.com - Pine Beach, New Jersey
May 10, 2013
Q. Thanks all for the answers... yes, I agree that is critical application and should be careful.
I agree with Mr. Probert that adding cobalt in the bath will give higher hardness and strength. But we get higher hardness distributed throughout the plate, similar high hardness from top to bottom. But I have to maintain lower hardness (200HV) at the top meniscus level of the plate to avoid chances of much cracking and high temperature embrittlement of the coating.
I think that the varied hardness and thickness profile can be achieved by varying the concentration polarization in the vicinity of the cathode. If it is true, then how can I create the varying metal ion concentration overpotential near the cathode ?
thanks in advance.
- Karnataka, India
May 20, 2013
Q, A, or Comment on THIS thread -or- Start a NEW Thread