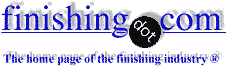
-----
Why a Chrome Dip after Oxidizing Bronze?
Q. What is the purpose of a chrome post-dip for oxidized bronze? We oxidize plated bronze and bronze substrates with a selenious acid/phosphoric acid chemical system. The parts are then immersed in a neutralizer, rinsed and subsequently dipped in the mild chromic acid. The experienced line operators say this step has been always part of the process, but cannot state why it was included many years ago. The chemical supplier is supportive, but cannot explain why some of his customers use chromic acid as well. Also, a small percentage of the oxidized bronze parts are subsequently given a clear powder topcoat and are subjected to a cure temperature of 375 °F. Is the chrome dip protecting these parts from discoloring during the cure cycle? Thank you
Norman LandryFinishing Technician - New Haven, Connecticut, USA
2007
2007
A. Hi Norman,
I am not familiar with the finish, but the chromic dip must improve corrosion resistance. See below. Owing to OSHA & EPA restrictions on hexavalent chromium, contact your chemical supplier for a compatible corrosion inhibitor (triazole compounds are commonly used for copper alloys).
From British DEF STAN 03-12/2 CHROMATE PASSIVATION OF BRASS:
Experience has shown that with certain classes of work, the degree of passivation produced by the process may not meet the specification test requirement... In such circumstances, the quality of passivation may be improved to an acceptable level by immersion in chromic acid solution immediately after treatment in the process solution and washing in cold water. Details of the additional treatment are as follows:
A.4.1 Process solution
Chromic acid: 50 to 100 g dm(-3) [50-100 grams/Liter]
A.4.2 Treatment
Immersion time (with or without agitation): 20 to 30 seconds
Temperature: 15 to 25 °C
After the additional treatment, the parts shall be washed and dried as in clause 9."
[cold water dragout rinse, 2 flowing CW rinses, hot running water for 15 to 30 seconds followed by drying in hot air not to exceed 90 °C.]
- Goleta, California

Rest in peace, Ken. Thank you for your hard work which the finishing world, and we at finishing.com, continue to benefit from.
August 12, 2011
Q. I do a lot of work in textured bronze which I usually bring up to a high polish. After polishing I degrease to remove all the polishing compound. Given that the bronze is textured this usually requires a spray bottle and toothbrush rather than a simple bath. The challenge I find is to be able to degrease, rinse, and dry without getting any oxidation discoloration. It's not too hard for small objects, but for larger ones it seems near impossible. After the object is degreased and dried I will coat with lacquer or wax to protect it.
My question is: After I degrease, and if there is oxidation, can I pickle for a split second then rinse, dry and lacquer or do I have to do a neutralization bath then rinse, dry and lacquer? I'm always afraid if I don't neutralize as well as rinse after a pickle bath then then there will always be a slightly acidic residue that will cause oxidation even under lacquer.
Artist - Carbondale, Illinois, USA
br
A. Hi Jared. We appended your inquiry to a thread which suggests possible solutions. Either a dip in chromic acid or, preferably, a dip in sodium benzotriazole ⇦ on eBay or Amazon [affil links] should deter the oxidation until you are ready to apply the lacquer.
Good luck.
Regards,
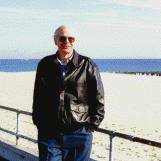
Ted Mooney, P.E.
Striving to live Aloha
finishing.com - Pine Beach, New Jersey
December 13, 2012
Q, A, or Comment on THIS thread -or- Start a NEW Thread