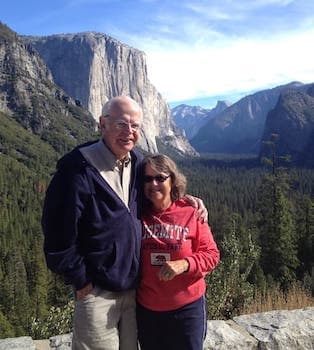
Curated with aloha by
Ted Mooney, P.E. RET
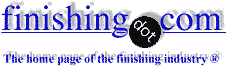
The authoritative public forum
for Metal Finishing 1989-2025
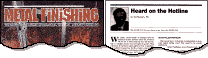
-----
Anodizing nickel on copper on PCB or is there a better way to get electrical conductivity isolation?
2007
Dear finishing.com forum:
I have an application that may require electrical conductivity isolation inside plated through vias in printed circuit board (PCB). The typical metallization used on this PCB is gold on nickel on copper. If anodization is desired to achieve electrical isolation in the through holes, should I be looking at plating and then anodizing aluminum on copper (or on nickel)? Or is it possible to anodize the nickel since nickel is already being used? Anodizing nickel does not seem to be possible from my latest web search.
Any comments or help will be appreciated. Thank you.
Sincerely,
Michael Young
Member of Research Staff
Palo Alto Research Center
Palo Alto Research Center - Palo Alto, CA, U.S.A.
2007
Michael
You cannot electrodeposit aluminium from an aqueous solution. Nickel forms a natural oxide on the surface but it is not thick enough to act as an insulator.
It is difficult to go further without knowing more detail of what you are trying to achieve.
If you cannot easily insulate the bore, then insulating the part going in the hole seems to be the next step.
The usual way of passing a conductor through a PCB is simply to use an unplated hole.
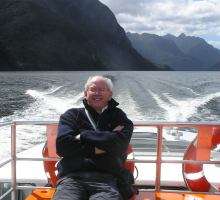
Geoff Smith
Hampshire, England
As Geoff says, the conductor can simply be run through an unplated hole. But if the intent is to produce some sort of capacitive linking, it might make more sense to run anodized aluminum wire through the plated hole than to try to anodize the plating in the hole. Boric acid anodized aluminum has long been used to manufacture electrolytic capacitors.
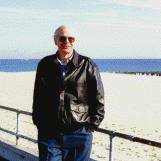
Ted Mooney, P.E.
Striving to live Aloha
finishing.com - Pine Beach, New Jersey
2007
Electrolytic capacitors comprise two sheets of aluminium foil with a paper spacer. The assembly is rolled up and then the paper is soaked in the electrolyte and the anodised film is formed in situ by applying DC to the assembly. A critical part of the design is that the electrolyte remains in place so that the anodic film is self healing. That is why electrolytic capacitors are polarised. Boric acid is a non aggressive electrolyte. Capacitors full of sulfuric or chromic acids could be unpopular when they explode (it does happen)
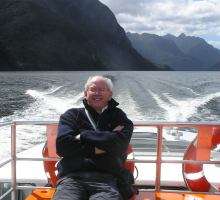
Geoff Smith
Hampshire, England
2007
2007
It was only a wild conjecture about why someone in advanced research might want to run an insulated wire through a plated-thru hole rather than just drilling a hole through an unplated area, Geoff. Obviously, the amount of capacitance of an anodized aluminum wire passing through a hole will be nearly zero by electrolytic capacitor standards, but electronics these days use nearly zero current.
I am interested in the anodize-after-assembly stuff you speak of though, since I was involved in the design of major coil processing lines for continuous boric and tartaric acid ⇦ this on eBay or Amazon [affil links] anodizing of aluminum coil stock for electrolytic capacitors in three different states, representing acres of foil that was anodized before assembly. I am curious to know whether things have changed or whether the material is anodized both before and after assembly.
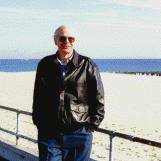
Ted Mooney, P.E.
Striving to live Aloha
finishing.com - Pine Beach, New Jersey
Q, A, or Comment on THIS thread -or- Start a NEW Thread