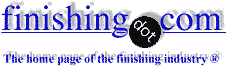
-----
Bright Nickel Chrome finish requirement for brake caliper pistons
2007
We are manufacturers of automotive component parts. A client of ours has requested that we produce disc-brake caliper pistons for them, but we are unsure about the coating.
We gave our factory the client's requirement as follows...
Nickel Thickness (Average) 0.0005-0.0009"
Chromium Thickness (Average) 0.0002-0.0005"
Total Thickness 0.0007
Surface must be free of pits and frosty surface chrome. Also, longitudinal or spiral tool marks, nicks or scores.
As you may know, the brake piston "rides" on a seal which contains the hydraulic fluid in the caliper. the same force which pushes the piston into the brake pads, to activate the braking action, would drive the fluid around the seal, if the piston surface were not (and did not remain) perfectly smooth.
They sent a preproduction sample which we forwarded to a testing facility in the States, along with a sample from a well established and highly respected competitor. The testing results yielded the following...
Our Sample
Nickel Thickness (Average) = 6.8 microns or 0.000268"
Chromium Thickness (Average) = 5.8 microns or 0.00023"
Total Thickness = 12.6 microns or 0.0005
Result: Failed
Nickel layer did not meet required tolerance
Competitor Sample
Nickel Thickness (Average) = 3.9 microns or 0.000154"
Chromium Thickness (Average) = 3.9 microns or 0.000154"
Total Thickness = 7.8 microns or 0.0003
Result: Failed
Nickel layer did not meet required tolerance
Chromium layer did not meet required tolerance
As you can see, our preproduction sample was better than the most trusted competitor's sample.
When we asked our factory to try and meet the required specification, they replied that they tried several platers who all had the same result, the surface "bubbled" when the thickness reached the required tolerance.
Our question...
Has our client set a standard that is chemically/physically impossible to reach?
To your knowledge, is either our preproduction or the competitor's sample test results (or both) adequate to provide long term protection to a steel piston that is sitting in brake fluid and exposed to high temperatures of the fluid and changes in temperature (from hot to cold)?
By the way, can trivalent chrome be substituted easily for the usual chrome used in this process?
Any assistance you can offer is truly appreciated.
brake components and parts - Cupertino, California
First of two simultaneous responses -- 2007
Nickel/chrome plating will protect the caliper pistons, but for how long? Nobody can answer that question because it depends on the number of brake applications, the type and cleanliness of the brake fluid, the amount of water absorbed in the brake fluid, the quality of the seals, the extent to which the pistons rub against the caliper.
A minimum of .0005" nickel is a good place to start. Thicknesses of
.0001"-.0002" are probably almost worthless.
As an alternative, you could use, say .0003" of chrome with no underlying nickel.
Make your platers meet the specifications. There is no reason they cannot do so.
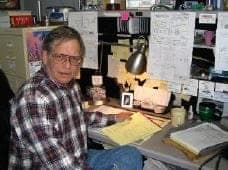
Jeffrey Holmes, CEF
Spartanburg, South Carolina
Second of two simultaneous responses -- 2007
Hi Michael, I suggest getting
ASTM B456
"Standard Specification for Electrodeposited Coatings of Copper Plus Nickel Plus Chromium and Nickel Plus Chromium";
ISO 1456 [affil link on Amazon]"Metallic coatings Electrodeposited coatings of nickel plus chromium and of copper plus nickel plus chromium" is similar.
A standard will aid in specifying the coating and instituting necessary quality controls, such as corrosion testing. Also, note descriptions of the different types of nickel & chromium platings.
A 15 micron minimum (perhaps 15-19 micron range) thickness of nickel is a standard specification. Typically, the top chromium plating is much thinner, but the original specification was perhaps based upon experience with this application. In any event, a "bubbled" surface
(between steel/Ni or Ni/Cr?) is unacceptable.
Trivalent chromium plating has been around for 30-some years. It is usually considered essential to use proprietary solutions.
- Goleta, California

Rest in peace, Ken. Thank you for your hard work which the finishing world, and we at finishing.com, continue to benefit from.
Q, A, or Comment on THIS thread -or- Start a NEW Thread