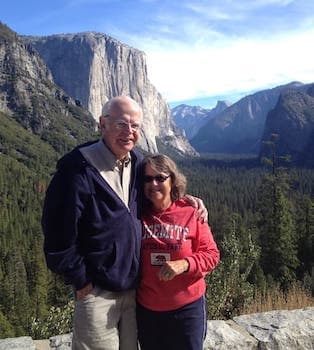
Curated with aloha by
Ted Mooney, P.E. RET
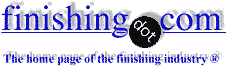
The authoritative public forum
for Metal Finishing 1989-2025
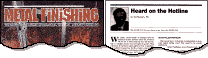
-----
Finishing of Surgical Plates
2007
I am an manufacturer of orthopedic implants situated in India.I need information about a process,by which I can remove the burr inside a 0.8 mm slot cut on the head of a surgical screw.The process I am incorporating right now is very time consuming.Please suggest a better process for the same.
I am also facing a problem on cutting down on my time cycle for the surface finishing of surgical plates.What I am using at present is a 24 hours roughing cycle with 04/04 D-Triangular (quality-RSS) media in in a Vibro with FC120, a 22 hours cycle in finishing ZS-Angle cut Cylinder,size 03/05 media(quality-RP),in RSP6268 POWDER COMPOUND,and a cleansing cycle of 2 hours.
What I am tying out now is to combine a centrifugal machine with my vibro and reduce the cycle time.Do let me know what can be done and what is the best way to do this.
- Pune, Maharashtra, INDIA
Are these basically flat parts and what kind of surface finish? The volume can be processed in a 1/4 cubic foot machine system. For deburring, I suggest plastic media for a wet process and treated organic materials if the parts are flat.
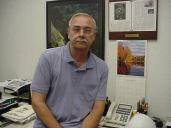
AF Kenton
retired business owner - Hatboro, Pennsylvania
2007
Yes,the parts are basically flat plates of dimensions 70*8*2 mm, which have holes of elliptical shape in it. The surface finish desired is a MIRROR FINISH. Could you please tell me the names of the chemicals used in the wet process,along with the plastic media? and where I can order these chemicals from? I already have a centrifugal machine of capacity 160 liters,and a vibro of capacity 300 liters. Could you please recommend a suitable process to be incorporated for the finish desired?
Shantanu Mangalvedhekar- Pune, Maharashtra, INDIA
2007
2007
There are some problems with your request. First, a mirror finish is kind of subjective. If you could specify an RMS it would be better. The wet process, cut down, should be done with a burnishing compound with good lubricity. If your parts are over 30 RMS, I suggest a 2 step wet process using a coarse plastic followed up with a fine to medium composition plastic. You need to get down to 18-22 RMS before trying a dry system. Our 6A dry organic abrasive should get you down to about 12-14 RMS. Lastly, use our 6E dry organic polishing mix to get down to 8-10 RMS.
A mirror finish can be obtained quicker with shorter time cycles but not smoother. Can't give you time cycles without knowing which machine you are using. If you can not get these materials, please contact me.
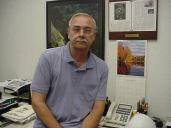
AF Kenton
retired business owner - Hatboro, Pennsylvania
Dear AF Kenton sir, this may sound weird but I don't really know what a RMS value stands for,or how to measure it. We here at pitkar go by the Rosler guide and the term RMS is not something we are familiar with.I have gone through your articles published on your website concerning deburring and finishing and it has not been stated what this RMS value stands for.Please do let me know.Thanking you in advance.
Shantanu Mangalvedhekar- Pune, Maharashtra, India
2007
RMS stands for root mean square. It is a mathematical term used to describe a surface variation from the mean line(average of peaks and valleys, measure with a profilometer). ISO specs use the standard Rq. Measurements are not interchangeable. So which ever you use, do not confuse as being the same.
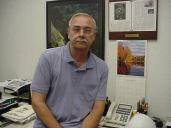
AF Kenton
retired business owner - Hatboro, Pennsylvania
2007
Q, A, or Comment on THIS thread -or- Start a NEW Thread