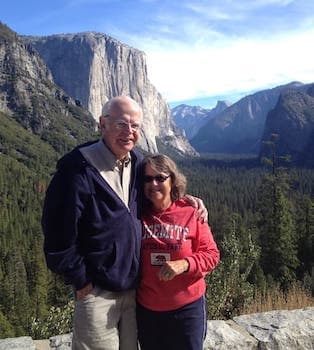
Curated with aloha by
Ted Mooney, P.E. RET
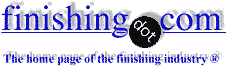
The authoritative public forum
for Metal Finishing 1989-2025
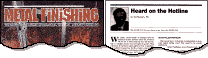
-----
White discoloration of black anodized aluminum - Type 3 Class 2 anodize per Mil-A-8625
I am a Process Engineer at a contract EMS and I have a problem. I have some FR-4 multilayer circuit boards that are bonded to a
MIL-A-8625 / MIL-PRF-8625
[⇦ this spec on DLA] Type II Black Anodized heatsink. We are seeing some intermittent discoloration of aluminum heatsinks after a defluxing cleaning operation. I am running them through a semi-aqueous cleaning solution , Kyzen Aquanox A4520W. It is a mild alkaline solution- a saponifier to remove rosin soldering fluxes from the circuit boards
We spoke with the company doing the anodize and they suggested a duplex seal. Their normal sealing process is nickel acetate and they are following this up with a hot DI water seal for 30 minutes. What process controls can be done on the process which might give some insight to the anodize and sealing processes. What things should be monitored and controlled in the sealing process
I got a sample from our supplier. It received a nickel acetate (?) seal followed by a hot DI water seal. I took a sample and ran it through our semi-aqueous cleaning solution, Kyzen Aquanox A4520W several times. The solution is 150F with a pH of 10. Each wash pass subjects the wash sample to an exposure time of 5 minutes. Ran one of the two anodize heatsinks from Polymetals through the NPI wash today at 0.5 FPM, 150F. After 4 iterations saw some discoloration and photos are after six wash passes. What is interesting is that there is much more discoloration on the top surface (half of board was taped off) of heatsink than on the bottom. Maybe related to more time for the solution to pool and contact the top versus the bottom of the heatsink.
Does anyone experienced this issue before. I took one of the discolored samples and it passed anodize coating weight and corrosion resistance. The anodize seems good but there is some sort of discoloration in the dye. Any ideas of any drag out or other things which might effect a nickel sealing process?
electronics - Tampa, Florida
2007
First of three simultaneous responses -- 2007
Aluminum metal and Aluminum Oxide and Hydrated Aluminum Oxide (the seal), are all attacked to some varying degree depending on time, temperature and concentration of ANY alkali, more so with heat, and certainly including Alconox ⇦ this on eBay or Amazon [affil links] , Florida chloride containing water, etc. . .
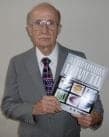
Robert H Probert
Robert H Probert Technical Services

Garner, North Carolina
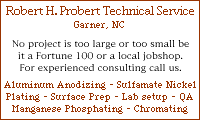
Second of three simultaneous responses --
Anodize is attacked by high pH solutions -- the higher the pH, time & Temperature, the greater the attack. Type, Class, dyeing, sealing, etc. are only minor details. Non-etching soak cleaners for aluminum are buffered to remain below about pH 9.1. See
(www.anodizing.org/html/faq_cont2.html#Cleaning), "CLEANING ANODIZED ALUMINUM"
Can anodized aluminum be cleaned with a detergent that has a pH of 10, or would that result in scaling or other surface problems?
Factors such as concentration of the detergent solution, duration of exposure, and temperature will influence the results. If the anodized aluminum is cleaned at room temperature and promptly rinsed with clean water, then there should be no problem. If cleaned at an elevated temperature or with prolonged exposure without rinsing, then the cleaning solution would start to attack the anodic oxide and etch the metal. Mild soap is generally preferable to detergent for routine maintenance cleaning.
- Goleta, California

Rest in peace, Ken. Thank you for your hard work which the finishing world, and we at finishing.com, continue to benefit from.
2007
Third of three simultaneous responses -- 2007
I am unaware of any exotic solutions to your problem that may be out there.
Basically, you are asking too much from your dyed anodize. Alkaline(high pH) solutions attack the anodize. The higher, the faster. Then temperature increases the rate of attack, again the higher- the faster the attack.
Sealing collapses the very top of the oxide cell to trap some moisture and the dye. Your process is slowly eating away the collapsed portion, allowing the cell to dry out and the dye be exposed to UV light and to leach out. The attack is slow, so you are maintaining good (but decreased)non cosmetic anodize properties.
I am not sure if there is a good answer for your problem. There would be less attack if the pH was 9.5 rather than 10, but then it would be less effective on its primary job and would have to be rerun again--which would probably have the net result of the same amount of attack on the anodize.
- Navarre, Florida
2007
Thanks for the response to my question about anodize. I understand that alkaline cleaners- modified saponifier- and anodize aluminum don't mix well. THe problem I have is the solder paste flux are difficult to clean and are a rosin base and require a saponifier to remove from the board. THe board is bonded to an aluminum heatsink.
What I do not understand is why some pieces do not discolor after a total exposure time of 5 min 30 sec (four passes) at 150F. Other parts do discolor.
The other thing that is perplexing is that I have tried three different chemistries from two vendors on four different in line wash systems. I took one sample and cut it into 8 pieces. On some pieces the anodize developed a dull matte look to the anodize, other pieces developed a white hazy appearance.
What type of questions should I ask the anodize provider about the raw material, pretreatment and sealer conditions? Could changes in the pore size possibly effect the chemical resistance changes I have seen. I will try to at least reduce the temperature from 150 to 130 F and increase the wash belt speed. The effects I see seem to be cumulative- a single pass cleaning cycle doesn't effect the coating appearance but after 3-5 cycles the effects are noticeable.
- Tampa FL
Hi there,
Why not bond the heat sink to the board after cleaning the board.
- Durban, South Africa
2007
In lieu of anodizing, consider e-coated aluminum. It is non-conductive, non-corrosive and up to 10 microns thick. on any raw aluminum.
Mike Dywan- Phoenix, Arizona
January 11, 2008
Q, A, or Comment on THIS thread -or- Start a NEW Thread