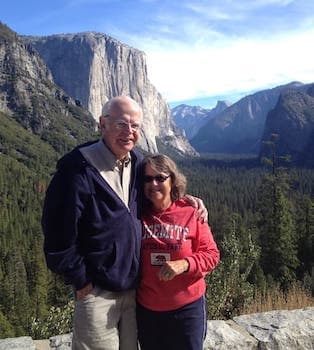
Curated with aloha by
Ted Mooney, P.E. RET
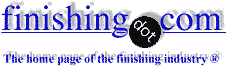
The authoritative public forum
for Metal Finishing 1989-2025
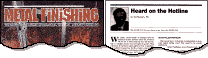
-----
Heating of Flux Bath
Q. We are a manufacturer of Steel Poles based in Jeddah, Saudi Arabia and do our galvanizing in-house.
Currently we are not using any heating for our flux bath which is a solution of ZAC double salt since our mean temperatures are around 35 °C day / 30 °C night in Summer and 30 °C day/ 25 °C in winter.
For the above conditions is heating the flux bath recommended and if so what is the temperature range?
Thanks,
ELECTRICAL POLE FACTORY - JEDDAH, SAUDI ARABIA
2007
A. One of the reasons for heating the flux is to enable better, faster drying of the fluxed steel. The water in the flux will evaporate much faster off warm steel than cool, and this means heated above ambient. This is also dependent on humidity. Having dry steel to immerse in the zinc means less splash and hence less ash (sometimes called top dross or skimmings?). So if your steel is dry before immersion, then this reason for heated flux is discounted.
Another reason is solubility of the ZAC, but at 30 °C that shouldn't be a problem either.
You are lucky with your ambient temps. We have 1 plant where acid temps can go as low as 2 °C in winter - makes for slow pickling. Flux is heated.
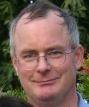
Geoff Crowley
Crithwood Ltd.
Westfield, Scotland, UK
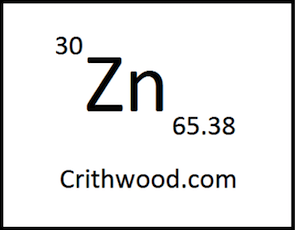
2007
A. Dear Francis,
For your application, quadraflux (See
Metal Finishing) at 71 °C (160 °F) at about 12 to 14 Deg baumé (Density) will give the best results. If you heat with steam the proper coil material is titanium. If you heat with electricity the heater would be inside a quartz tube and correctly grounded. Both heating methods have a long life if you protect the heaters from product with shields. In use, the steel must remain in the hot flux at least 3 minutes to heat up all the way through so as to properly dry before kettle entry. Quadraflux which is a formulation not a product, dries much better than double salt which has more zinc chloride which is hygroscopic (collects moisture from the air). All fluxes require an effective wetting agent, which only one has passed all the requirements. There are seven flux parameters in flux that must be maintained to get best results.
Properly maintained and used, quadraflux delivers about 30%+ zinc savings, quality that rivals electroplate, and almost never "black" (bare) spots. Zinc "clean-up" after galvanizing is minimal. I liked Jeddah when I was there.
Regards,
Galvanizing Consultant - Hot Springs, South Dakota, USA
2007

Q, A, or Comment on THIS thread -or- Start a NEW Thread