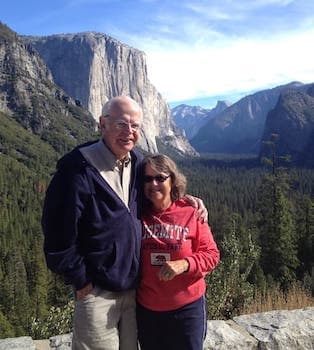
Curated with aloha by
Ted Mooney, P.E. RET
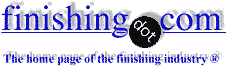
The authoritative public forum
for Metal Finishing 1989-2025
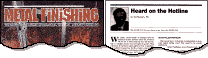
-----
Humidity and rusting in plating shop area
After changing chemical solutions for light plating, i.e.: passivation, cleaning, etch, Alodine etc, there has been a noticeable and detrimental increase in rust of the superstructure and environs of our plate shop, any tips or ideas?
Edward Shouldersjob shop - Willits, California, USA
2007
Such process tanks require ventilation, but even then there may be corrosive fumes. Are you using any HCl in the new process sequences (this is probably the worst offender in causing rust).
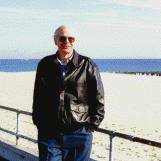
Ted Mooney, P.E.
Striving to live Aloha
finishing.com - Pine Beach, New Jersey
2007
2007
Hi Edward,
The first thought that hit my mind was that there was insufficient ventilation.
The 2nd one was that, as Ted says, it might well be HCl ... or some other reducing acid fume.
Many, many years ago I dropped into a plant owned by Electric Reduction (Now called ERCO) where they had sodium chlorate tanks and a very RUSTED ceiling.
They tried all the paints...some of which are quite expensive.
Their solution? Use asphalt, i.e., tar. l00% success and cheap as wurst.
Then some years later, a refinery in Montreal was exhausting fairly hot sulfuric etc fumes. I couldn't use PVC due to the temperature but suggested Polypropylene BUT in those days a UV resistant PP ducting didn't exist ... so as some of the ducting was exposed on the roof, I coated it with tar.
10 or so years pass by and I got a comment from someone that HECK, SOMEBODY PUT A COATING OF ASPHALT ON THIS DUCTING, WHAT A STUPID THING TO DO.
IPSO FACTO, THE PROOF OF A PUDDING IS IN THE EATING, EH?
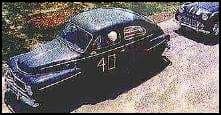
Freeman Newton [deceased]
(It is our sad duty to advise that Freeman passed away
April 21, 2012. R.I.P. old friend).
Q, A, or Comment on THIS thread -or- Start a NEW Thread