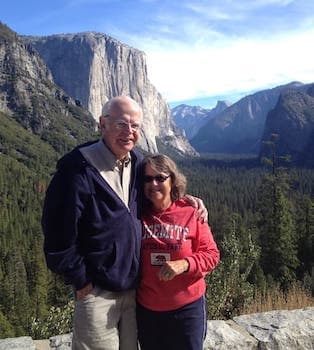
Curated with aloha by
Ted Mooney, P.E. RET
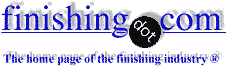
The authoritative public forum
for Metal Finishing 1989-2025
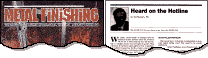
-----
Type II vs Type III Anodizing of 2024 Aluminum
Q. I am experiencing anodize flaking of 2024 aluminum primarily on products that are either dry filmed and baked or that require oven glue cure. Dry film parts are baked at 400 °F for 60 to 75 minutes. The only contributing factor that I have found relates to the time the parts are left in the rinse tank after the sulfuric acid bath. The longer the rinse time the greater the flaking. We currently rinse for 2 minutes which gives the best results. Any suggestions?
Sam AbsherJob shop - Jackson, Michigan, US
2005
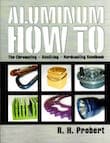
Aluminum How-To
"Chromating - Anodizing - Hardcoating"
by Robert Probert
Also available in Spanish
You'll love this book. Finishing.com has sold almost a thousand copies without a single return request :-)
A. The thermal coefficient of expansion of the anodic film has approximately 0.2 times the aluminum metal. 2024 is worse.
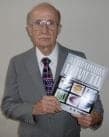
Robert H Probert
Robert H Probert Technical Services

Garner, North Carolina
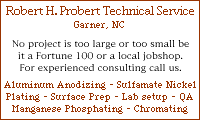
⇦ Tip: Readers want to learn from Your Situation 🙂
many readers skip abstract questions.
? How did you solve this?
Ed B- Largo Florida
November 19, 2024
Tip: This forum was established to build camaraderie among enthusiasts through sharing tips, opinions, pics & personality.
The curator & some readers who publicly share their info will be less likely to engage with those who don't.
Q. Can someone tell me the difference in wear properties between these two:
1. Material: 2024-T351, anodize per MIL-A-8625 / MIL-PRF-8625
[⇦ this spec on DLA], Type II, Class 2, Color Light Gold.
2. Material: 2024-T351, hard anodize per Mil-A-8625, Type III, Class 2, Color Black.
Also, why is 2024-T351 considered more difficult to hard anodize and what similar strength alloy would hard anodize more easily?
engr - Portland, Oregon, USA
2007
1. Bad.
2. Poor. MIL-A-8625 allows hard anodized 2024 to have a Taber abrasive wear loss 7/3 x that of 6061 or 7075, and dyeing + sealing further softens the anodize.
Some effects of alloying are described in the Aluminum Anodizers Council 'Anodizing Reference Guide' http://www.anodizing.org/reference_guide.html ⇩
Simplified technical explanation: The Cu in 2000-series alloys forms intermetallics such as CuAl2 which dissolve rather than anodize. About 7 wt% CuAl2 in 2024, so the anodize is ~7% more porous than on a low-Cu alloy. The intermetallics also increase ohmic heating within the alloy, which in combination with thin spots in the anodize, can lead to a nasty, electrochemically-accelerated dissolution phenomenon known as 'burning.'
Many newer alloys have high strength and anodize better than the 1920's vintage 2024. Some with better corrosion resistance in higher strength tempers than the 1943 vintage 7075. The Metallic Materials Properties Development and Standardization (MMPDS) Handbook lists a number of 7000-series alloys: 7010, 7040, 7049/7149, 7050, 7055, 7075, 7150, 7175,7249, 7475; also 6013.
Yield strengths (ksi) for thicknesses up to 2 inches.
2024-T351 42-50
6013-T6 46-49
6013-T651 52
7010-T7451 61-63
7049/7149-T7351 60-64
7050-T73511 56-60
7055-T7751 85-88
7075-T7351 52-59
7150-T7751 74-78
7175-T73511 52-59
7475-T7351 53-61
All values from MMPDS-01 except 6013-T651 (MatWeb). 7040 (heavy plate only, > 3") and 7249 (Hand forgings) were omitted.
- Goleta, California

Rest in peace, Ken. Thank you for your hard work which the finishing world, and we at finishing.com, continue to benefit from.
Ed. update: The anodizing reference guide is no longer available, but a replacement for it, bulletin #4-13, is included in a compendium available from anodizing.org for $75.
A. Type III anodize of 2024 is a risky venture due to the higher concentration of copper within the alloy. Not to say it can't be done, we do it often, but the risk of material degradation is increased.
To answer your other question, 7075 would be more appropriate for a type III coating.
-Bill
metal finishing - San Jose, California, USA
Q. How to anodize parts made of aluminium alloy 2024 to 25 microns (one mil)?
What is the bath composition, bath temperature, current density and duration?
Finishing employee - Istanbul, Turkey
2007
Treatment &
Finishing of
Aluminium and
Its Alloys"
by Wernick, Pinner
& Sheasby
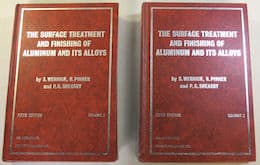
(note: this book is two volumes)
on eBay or
AbeBooks
or Amazon
(affil links)
A. Hello, Erol. The generic bath is 10% by volume sulfuric acid, operated at 0 °C or slightly below, current density of about 24 ASF, and the time is calculated with "The 720 Rule".
More operational info can be found in thread 11365. Still, it's a long trip from making up a generic bath to successfully hardcoating 2024 to that thickness. It is quite difficult to hard anodize (50 microns) or even anodize to a thickness of 25 microns, and it has been the subject of a dozen letters here already. So if you use the search engine to look for "hard anodize 2024" you'll get some very good insights into the issue.
Unfortunately. our readers readily share how to do the moderately easy things, but when they've finally figured out how to do the difficult ones like hardcoating 2024, and earn their living from it, they tend to hold their little tricks close to their chest.
It's probable that pulse rectification, additions of oxalic acid or glycolic acid, and extraordinarily good agitation will be part of the solution -- I can afford to share what I know both because I don't earn my living that way, and don't actually know the little tricks :-)
Luck and regards,
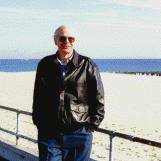
Ted Mooney, P.E.
Striving to live Aloha
finishing.com - Pine Beach, New Jersey
Black Stains when Anodizing 2024 Aluminum
Q. Dear all,
We are into anodizing process shop, I have faced following difficulties during anodizing on 2025 material.
Our anodizing process sequence will be vapour decreasing, alkaline cleaning, deoxidizer (sulpho chrome), desmutting and anodizing.
1. In some parts we have faced black stain marks after deoxidising process. In some batches deoxidizer will come okay, but it will show same problem after desmutting and sometimes after anodizing.
We are totally confused where the problem is arising. It is totally looking in not acceptable condition.
After this we removed anodizing with phosphoric and chromic acid, black strains were not removed. It looks in sticky condition. We have done manual cleaning also after stripping, same problem arising.
Please suggest where the exact problem is arising -- it's in deoxidizer or desmutting or in anodizing? Same problem arising since 3 months. Is it really required to change the bath? Which bath?
And also suggest what exact procedure to follow for the 2024 series material.
I am really worried to clear the parts. Thanks for your valuable cooperation.
Regards,
Sanjeev lamaniaerospace components - Bangalore, Karnataka, India
March 20, 2016
by Larry Durney
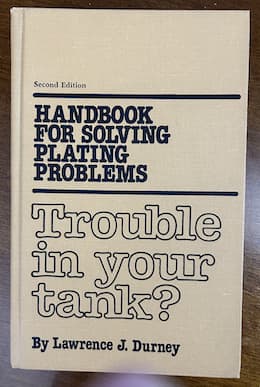
on eBay
(sometimes) or
AbeBooks
(rarely)
or Amazon
(sometimes)
(affil links)
Hi Sanjeev. I I see you've at least included a photo, and hope a reader can help you out. But on-site troubleshooting to establish where the problem is arising is often critical and I don't know if guesses will be much help :-)
There are hopefully anodizing consultants in the Bangalore area who could quickly get you out of this quagmire, but if not, I think what may be missing is a highly orderly troubleshooting plan. Best of luck.
Regards,
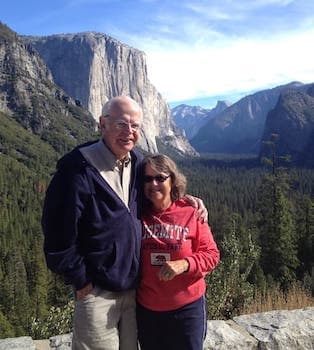
Ted Mooney, P.E. RET
Striving to live Aloha
finishing.com - Pine Beach, New Jersey
Q, A, or Comment on THIS thread -or- Start a NEW Thread