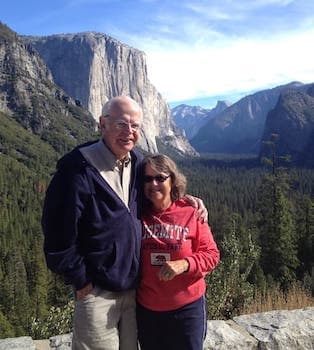
Curated with aloha by
Ted Mooney, P.E. RET
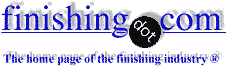
The authoritative public forum
for Metal Finishing 1989-2025
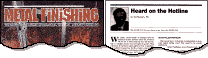
-----
Carbon contamination on stainless steel
Q. I'm a quality control manager at a steel fabrication shop.
Carbon contamination on stainless is a big problem, primarily from the material suppliers. What should I be using to "COMPLETELY" remove carbon/rust from stainless (300 series) without turning my facility into the next superfund site.
Gary Parker- Orlando, Florida
2000
A. If you're not under strip-line style time pressure you can probably use a nitric acid bath to clean and passivate the stainless, that would remove light deposits of carbon and oxide. If you are under high production time constraints or have extremely nasty parts, you'll have to use the dreaded HF-Nitric-Sulfuric milkshake, and deal with neutralizing and disposal. I know citric acid is being used for that purpose, and if possible would represent the best option, but I have no experience with that process. I hope that helps.
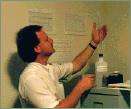
Jeff Watson
- Pearland, Texas
2000
A. Hi Gary ,
All the acid treatments in the world will only heighten the problem if it is "Carbon". To remove the carbon you must treat it with a Alkaline Deruster type of product; these products are usually caustic / chelate blends run warm to hot and in reverse current at between 25 & 50 Amps / square foot. And the stainless steel is best "passivated" afterwards by Electropolishing.
I have yet to see a "Carbon" problem on 300 series S/S are you sure it's "Carbon"?
Regards

John Tenison - Woods
- Victoria Australia
29 february 2000
A. Gary:
There is a new process for cleaning, passivating, and electropolishing that was developed in Australia and is now available in the US. It is environmentally friendly and won't turn your plant into a superfund site.
Dan Weaver- Toccoa, Georgia
2000
2000
adv.
Gary Parker:
Our company offers complete cleaning, deoxidizing, and electropolishing processes. There are several "zero discharge" options for handling the waste products.
Please look us up in the directory on this web site.
Regards,
Ed Bayha
Metal Coating Process Corporation - Charlotte, North Carolina
Gary: I, also, wonder whether it is really carbon on the surface. We see rust on the surface of 300 grade stainless regularly, as received from the suppliers, but I have not seen carbon. There are easy, economical and safe and environmentally friendly ways to take care of your problem with our citric acid formulations.
adv.
When used correctly, CitriSurf is very effective in removing the rust and other contaminants to provide an excellent passive surface. We would be happy to test for you or send samples. Call us or email us for details. Lee
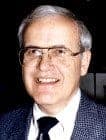

Lee Kremer
Stellar Solutions, Inc.

McHenry, Illinois
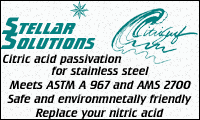
2000
Q. Dear Gary,
I too suffer from almost similar problem. I suspect CARBON. We tried to dissolve it but to no avail... so I guess it must be some inert material... i.e., Carbon perhaps. It managed to get 50% cleaned stainless steel with some acid washing. Then somehow by drying the stainless steel plate, a hardened carbon surface is formed. This can be easily scrapped off (we use high pressure water jet). It won't be 100% cleaned but maybe with more washing, it can be better than before.
Regards,
Kent [last name deleted for privacy by Editor]- KL, Malaysia
2002
A. We use glass bead, and a sandblasting unit to bead blast the stainless. No more nasty acids.
Scott Thomson- Edmonton, Alberta, Canada
(2008)
Q. I've heard that sandblasting, etc. will not completely remove contaminants and the rusting will come back. True?
Jason Harper- Bradenton, Florida USA
December 21, 2012
A. Thanks Scott, for what may be a good idea. But I've personally never heard of bead blasting being able to replace passivation. Have you run any humidity tests or done other controlled testing to indicate that these bead blasted surfaces won't rapidly rust?
Hi, Jason. I don't know for sure, but until some test results or, better yet, field results are in, I'd be very leery of not passivating stainless steel parts before putting them in service.
Regards,
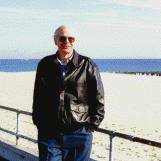
Ted Mooney, P.E.
Striving to live Aloha
finishing.com - Pine Beach, New Jersey
December 21, 2012
Q, A, or Comment on THIS thread -or- Start a NEW Thread