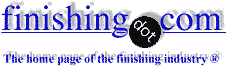
-----
Cold Water Passivation of Nickel Plating
⇦ Tip: Readers want to learn from your situation;
so some readers skip abstract questions.
Q. You mentioned dilute solution of nitric acid, chromic acid, citric or sulfuric acid, etc. could passivate nickel. I want to know what the concentration for each acid, which can form good passivation. Usually, how long will it take to passivate the Ni, and what is the thickness of the passivation layer? Also, is the passivation layer NiO?
Thanks,
Engineer - Santa Clara, California
June 3, 2022
A. Hi Tuo. I think you have misinterpreted Mr. Udofot's posting. In fact he and Mr. Watts say dipping in a dilute acid may weaken the passivation film.
Rather, Mr. Udofot was suggesting electrolytic passivation. Please do a scholar.google.com and patents.google.com search for "nickel passivation process" and/or "electrolytic passivation of nickel" and you should find lots of info on the subject.
But please introduce yourself and the situation, including the thickness of the nickel plating, that prompts you to inquire about this subject.
Luck & Regards,
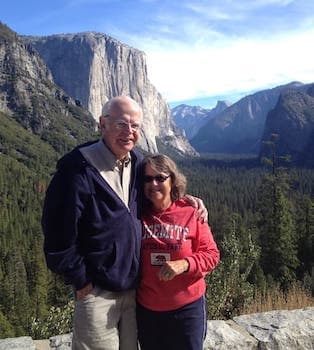
Ted Mooney, P.E. RET
Striving to live Aloha
finishing.com - Pine Beach, New Jersey
June 2022
⇩ Related postings, oldest first ⇩
I am a working supervisor in a captive plating shop. It is my responsibility to troubleshoot our problems. I have taken an excellent course sponsored by my local AESF Branch. I have been in the plating field for about 6 years and still consider myself a beginner.
I have heard/read that nickel can become passive if it is rinsed in cold water after activation or plating. Is this true? If it is, why does it occur? What temperature rinse would be considered cold? What are other possible causes of passivation in nickel plate besides drying?
The process involved uses a Reel to Reel line plating wire. At times due to the set up of the line it is required to activate a nickel alloy (C200 or 205), rinse, pass through air for about 20 feet (30 seconds or so) and then plate in an MSA tin or tin-lead. I have seen the wire dry in this time.
Any help that can be given will be appreciated.
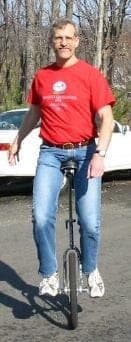
Jerry Smith
- Bloomingdale, NJ USA
2000
![]() |
2000 My guess, strong feeling with no solid evidence, is because water contains dissolved gasses, IE: oxygen in the form of O2 or nascent oxygen. Warm water contains a lot less O2 than cold water. Boiling will remove nearly all of it. If nickel alloy dries, it is virtually guaranteed to passivate, worst case is erratically. Nickel kept wet may last a few minutes, but do not bet on it. The lower the pH, the less likely it is to passivate. On racked parts, you could get away with a longer "storage"time in in the woods nickel rinse tank than the caustic rinse tank. Short of backing the line up and putting a leader on the wire, you probably will need to remove or mark that wire that passivated as bad. James Watts- Navarre, Florida Hey Jerry, The Temperature of the rinse plays two roles: First, the colder the rinse water the lower the rinsing power (or the longer it takes to rinse); Second, the colder rinse leads to lower levels of dissolved oxygen in the rinse water. It's the oxygen in the rinse water and air that passivates the nickel. So it's really a matter of the time (in the rinse and 20 feet of air) between the activation and the start of plating that causes the passivation. If the nickel oxide is not too thick the MSAcid will strip it before plating begins. Normal line speed works fine but delays cause problems, right? You might add a MSAcid (include a wetter so you don't drag-in too much solution) activation step before the plating bath. No need to rinse the MSAcid off before the plating tank. Regards, Fred Mueller, CEF- Royersford, Pennsylvania 2000 |
I've seen passivation occur in EN baths due to algae in the first rinse. There's a lot of fruit acids in the bath that are "yummy" for the small creatures. Sven
Sven- Sweden
2000
Mr. Jerry,
To answer your question, one should first know what passivation is. Passivation is a process or the phenomenon by which a metal surface remains un-attacked by corrosion because the metal surface conditions have been protected. Like Manganese, titanium, Aluminum or steel, Nickel has a strong affinity for oxygen in air or water. Therefore in cold water Nickel can form a stable oxide film on its clean surfaces to become passivated. The formation of passive oxide film on its surface is accelerated when rinsed in clean hot water below a boiling point. In passivation (hard oxide growth film) process, nickel is made the anode and its passivation improved by rinsing it with either a dilute solution of nitric acid, chromic acid, citric or sulfuric acid; for example and then thoroughly rinsing with deionized water. The nitric or chromic acid oxidizes and dissolves any impurities on the surfaces of the Nickel. The deionized water rinses off any remaining organic acid and inorganic impurities allowing the stable oxide film to remain on the nickel for corrosion protection. The part would then be blown dry, leaving the oxide film, strongly bonded on the nickel surface. It is important to note metal that do not form strong affinity with Oxygen, may be successfully passivated.
The key point in obtaining a superior oxide growth film on nickel is proper surface pre cleaning to remove oil, dirt and other metal impurities.
It would be a mistake to finally rinse a passivated component such as nickel from boiling and or strong acid of low pH water since such would etch off or reduce the thickness of the oxide growth film on the metal, rendering it prone to less corrosion protection and so; I do agree with Mr. James Watts of Florida, on this.
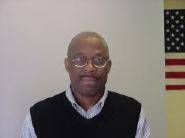
Bassey J. Udofot
Musgegon, Michigan
April 18, 2010
Q, A, or Comment on THIS thread -or- Start a NEW Thread