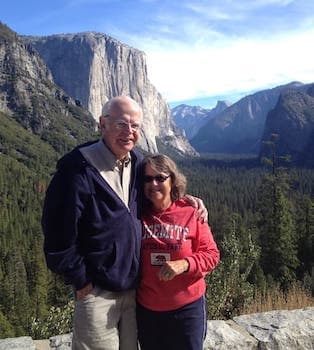
Curated with aloha by
Ted Mooney, P.E. RET
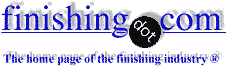
The authoritative public forum
for Metal Finishing 1989-2025
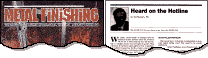
-----
Grit blasting before Nickel plating
2000
We are a job shop performing aerospace overhaul & repair with sulfamate nickel. Our SOP for the parts includes covering with wax stop-off and removal of the wax from the surface to be plated. This surface is then grit blasted to remove residual wax before manually cleaning the surface with a solvent. We have been using the grit blasting step for over 10 years and it is in our SOPs.
We recently had a survey and this one customer stated that grit blasting is not a proper procedure and that it would yield unsatisfactory bond and to cease this process step immediately.
We know and need to prove that grit blasting improves substrate cleanliness and improves deposit bond strength. Does anyone know of any literature or Specifications which site the use and/or benefits of grit blasting for use in this application.
Tony D'Amato- Chicopee, Massachusetts
2000
I am not in favor of using it to remove residual wax, per say, but a light dusting with 220 or 320 AlO3 does a wonderful job of locating missed wax (traces) and has the added effect of roughening the surface which gives the plate more grip area or teeth.
It also removes oxides that can be very difficult. It will remove metalorganics from hot section parts that are difficult to impossible to remove by conventional methods.
The AlO3 is dissolved in the caustic cleaner quite rapidly.
It is hard to argue with a customer. Peel test is the only answer. If it holds, it is OK. SS can be successfully plated by going from the blast cabinet to the strike tank within a minute or two, with no special cleaning or etch. Not my cup of tea, but I have done it.
James Watts- Navarre, Florida
In the early 80's I worked for a plating shop that performed almost all mil spec plating , we used a process called "Vapor blast" which was a wet cabinet blasting system. The plating was mostly aircraft and military applications. However , I do not remember the vapor blast being used as a wax remover , it was more of a prep stage for specific components , mainly for silver plating.
We did use a hot wax mask dip , but areas to be plated were left exposed. not waxed over/then removed. I would believe your customer to be concerned with the bond of the plate , should there be any wax residue , visible or not.
I have seen waxing done , using foil tape to cover the section not to be masked , then the part is dipped , and the tape removed. the tape residue is easily cleaned up chemically ,usually by hand. a slow process at best.
Ron Landretteplating equipment supplier - Bristol, Connecticut
2000
Q, A, or Comment on THIS thread -or- Start a NEW Thread