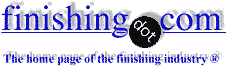
-----
Electroforming Mandrel Build
We do a lot of Ni (sulfamate) electroforming into resist patterns to make screening masks (plated like circuit board processes, etching can't do the dimensions). We encounter various problems as the existing process has been using copper foil mandrels as the conductive base which is then part of the final product (hard to handle, not smooth enough).
There are some significant gains to be made by switching to polished steel as a re-useable mandrel, but we are concerned about the costs. The typical machine shop is not used to polishing a steel plate and it appears the options we have so far seem too expensive (thousands per piece). The ASTM surface finish spec is simple enough, 2microinch RMS and its simply a rectangle of 300 series steel between 9x9in up to perhaps 15x15max. I know this type of process is used so there must be some information on how to build these easily and relatively inexpensively. The copper foil is so cheap that cost is a real issue. thanks
Paul FindeisVerbank, New York
2000
If your object is to make reusable mandrels, is there any reason they can't be electroforms themselves, Paul? This is how vinyl records, videodiscs, CDs, and a host of other precision electroforms are made. It seems, though, that if your electroform is very thin you will have difficulty separating it from a reusable mandrel no matter what the mandrel material is.
In which case, is there a good reason you can't make the mandrel from aluminum and then dissolve it in caustic to get the original foil out of there?
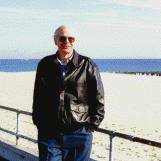
Ted Mooney, P.E.
Striving to live Aloha
finishing.com - Pine Beach, New Jersey
2000
Paul,
have you considered simply bright Ni plating the laminate you are currently using? This will make it reusable and improve the surface finish at a lower cost than polishing stainless.
Best of luck from PlaterB
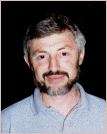

"PlaterB" Berl Stein
NiCoForm, Inc.

Rochester, New York
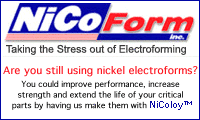
2000
Q, A, or Comment on THIS thread -or- Start a NEW Thread